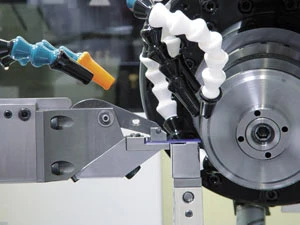
Bone cutting is one of the oldest surgical procedures, including trepanation of the skull plate. Today, one of the most commonly used cutting procedures is drilling holes into bones for inserting orthopedic implants to hold fractures and prostheses. Surgical cutting tools, which are ground on a CNC tool grinder, usually have a positive cutting geometry and can be divided into rotary and flat tools. Most rotary tools are powered instruments, while the flat surgical cutters are used manually.
The basic shape of the tool is often machined on Swiss-type lathes in a more pliable state. This includes the driving notch, which is the quick-disconnect and driver feature at the end of the shank. This operation is followed by hardening or by centerless grinding.
Centerless grinding is useful in preparing the cylindrical land on bone drills, and is mandatory for longer shanks on burs and drills. Unlike all other grinding operations that can be ground on a multi-axis tool grinder, shank grinding has to be carried out on a centerless grinder using a through-feed method.
TYPES OF TOOLS
Drills and twist drills:
Metal cutting knowledge has helped to shape the different geometries for drill points and flute shapes suitable for drilling into bone. The main goals in engineering medical drills are minimizing the thermal injury to the surrounding bone and reducing the cortical penetration. Studies have shown that temperatures of more than 50°C are associated with irreversible changes in the structure and physical properties of the bone. Many orthopedic operations involve drilling and tapping before inserting screws into the bone.
There are several types of drill points, such as conical, split points, 3-flute points and trocar points. Available drill bodies include solid stainless steel, tubular drills for removing drill debris, and cannulated bodies with trocar points. Other drill bits cover fixation stakes and trepanning tools.
One distinguishing feature of a surgical drill point is the point angles, which are lower in comparison with industrial drilling tools. Point angles range from about 90° down to 75°.
Special software with 3D simulation is available to design the flute shape, the outside diameter clearance, the point, and the point thinning. VirtualGrind by Rollomatic is a software suite that allows extensive free programming in order to accommodate the specialties in surgical tools and user-defined features.
Bone taps:
Bone taps can be produced completely by machining alone, but the more demanding surgeons prefer to use a tap that has precision-ground points for better penetration. These taps can be manufactured on a multi-axis grinder including the flutes and the thread form. Such taps are extremely high-quality and are usually reusable. Taps are used to pre-thread the bone. The depth of tapping is relative to the density of the bone; in very dense bone, about 2/3 of the screw length should be tapped, and in very loose bone, just a few threads are sufficient.
Burs & spherical burs:
Materials used for surgical burs are highgrade stainless steel and high speed steel grade.
Typical shapes include oval, acorn, barrel (cylinder-ball), round (spherical) and pear-shaped. The head diameter ranges from 0.5mm to 10mm, or larger. The number of teeth that the bur has is relative to the level of recommended rpm. Most surgical burs have a cross cut that acts as a chip breaker. Some burs are left-hand spiraled, so that the surgeon can use the other hand and still experience the same cutting behavior.
The available shank types are tubular, solid, welded or a two-piece construction, where two tubes are laser-welded together.
Perforators:
Trepanning is a form of surgery in which a hole is drilled into the skull. Then a router is inserted into the hole and routes a larger plate that is then temporarily removed, providing surgical access to the brain. These drills are called perforators, and come in solid version for use with a hand drill, or in a two-piece construction for use with a motorized device. In the case of a powered handpiece, a mechanism will prevent the perforator from touching the brain tissue.

The Rollomatic GrindSmart620XS toolgrinding machine has three linear axes andthree rotary axes.
Reamers:
In typical reamer applications, the reamer hole is pre-drilled with a bone drill; a guide wire is then inserted into the hole. A cannulated hip reamer is used to over-ream the guide wire up to the depth needed. There are also stepped reamers to prepare the bone to accept specially-shaped implants. A spherical cutter, also known as a reamer, is used to shave the inside cup of a hip socket. This spherical reamer has the shape of half a sphere and has multiple teeth, similar to a bur.
Shaver Blades:
Rotary shaver blades are used to remove tissue and debris, and for bone resection. They always run on powered handpieces. They consist of an outer stationary tube with a small window towards the front of the tool, and an inner rotating tube with a smaller window in the identical position. Both windows have the shape of cutting teeth, and when they are moved against each other, they perform the desired "grabbing" action. The debris is then moved up the tube by suction assistance.
Rasps:
Rasps are used for bone surgery, bone correction, hump removal and other orthopedic procedures. The terminology "diamond chip cut" in rasps comes from grinding a cross cut across the already angled main cut, creating a diamond pattern. Those cuts usually run perpendicular to each other. Other patterns only have a small chip breaker in the main cut. Some of the types of rasps with narrow tooth profile are disposable and cannot be used repeatedly, since they may harbor harmful debris that clinical cleaning does not fully eradicate.
Another category of rasps are hip broaches. These are a set of shaped rasps which progressively increase in size and are used to internally shape the femoral canal during hip replacements.
Saw Blades:
Bone saws or bone saw blades and reciprocating blades are used in many medical devices for orthopedic procedures, amputations and removing casts. These blades oscillate back and forth only a few degrees at a very rapid rate, causing the cutting action. For removing casts, this type of saw will not cut flesh, it just jiggles the skin.
To grind surgical cutting tools, a CNC tool grinding machine with 6 interpolating axes is necessary, such as the GrindSmart 620XS by Rollomatic. The same tool grinders are used to manufacture carbide and HSS industrial cutting tools.
The demand for flexibility when grinding surgical tools is very high; therefore, 6 CNC axes are essential for cost-effective and fast grinding. Three of the six axes are linear axes and three are rotary axes. Due to the competitive nature of producing these tools, rapid setups, short cycle times and extended wheel life is crucial.
In addition, two separate wheel arbors, each with four multiple wheel mounts, are running on a double-ended grinding spindle. The grinding spindle is a directdrive spindle and does not have any belt transmission.
Because most surgical tools are small in diameter and long in length, their straightness is not always guaranteed. Heat treatment of these instruments induces warping, which often has to be corrected manually before grinding.
The way the blank is held in the CNC grinder is of utmost importance, since the parts are "bent", it is best to hold them short in a collet system which acts as a driver.
For drills, an excellent solution is to use a half-round steady, where the round blank can be positively seated. This ensures good geometry and allows increased feedrates. Vibration typically caused by the grinding process is reduced, prolonging wheel life.
Bushings are difficult to use when grinding surgical tools. The diameter tolerance on surgical blanks is too large, making it impossible to employ the bushing in a useful way.
For grinding stainless steel and HSS steel, superabrasive wheels, know as cBN (cubic Boron Nitride) wheels, are used.
There are two types of cBN wheels in use. The more common type is the resin or metal bond, where the cBN particles are baked into a bonding matrix. The other type is the electro-plated cBN wheels, which have a single layer of chemically attached cBN particles on a steel body. Standard abrasives are rarely used on CNC grinding machines for surgical purposes.
When grinding stainless and HSS blanks, it is imperative to consider the substantial influence that the right choice of coolant oil, filtration and chilling has on the performance of a cBN super-abrasive wheel.
Lean manufacturing in medical tool grinding basically refers to smaller lot sizes and quicker setup. This can only be achieved with a suitable software package.
VirtualGrind by Rollomatic, is a grinding software suite that includes flute, 3-D tool and machine simulation. The tools can be designed off-line on a Windows-based PC using individual standard and special grinding operations.
The operator or tool designer can generate these specialty grinding modules on their own. All modules have pictorial association, and a PDF file can be launched to give more detailed grinding instructions.
The 3D simulator has the ability to export a STEP file (.stp format) in 2D or 3D format, which in turn can be imported in any commercially available CAD software.
A 3DViewer package is also available, which can be sent to the customer together with the 3D file at the quotation stage.
Both the 3D simulation software and the 3DViewer have the capability to zoom, rotate, section, pan, and measure distances and angles. Efficient networking, standardized file management and file sharing are other areas where the VirtualGrind software is appropriate for surgical tools in terms of functionality and performance.
Short batches in CNC tool grinding have traditionally been a problem, due to insufficiency in software and general machine drift.
New systems are now available to make short runs more attractive, so that some of the philosophy of lean manufacturing can be transferred to CNC tool grinding. Workflow and workplace organization, standardization and waste reduction are now properly addressed in surgical tool manufacturing, and making surgical tools is no longer looked at as an "art", but rather as a "standardized process".

The Rollomatic GrindSmart 620XSoffers a half round steady rest, giving fullsupport during fluting.
An important aspect of cost-effectiveness is unattended production, for both rotary surgical cutting tools and for blades and rasps. A pick-and-place loader, which is part of the basic Rollomatic machine design, holds the tools vertically in a cassette.
This vertical storage works well with tool lengths up to 12 in. Hydraulic grippers transfer the blank from the loader compartment to the grinding area. A pickand- place loader has a cassette table that lifts hydraulically. If the blanks are longer than 12 in., a horizontal magazine loader is recommended. This magazine loader has a larger capacity than the pick-and place system and is mainly suitable for long-shank bone drills.
The quick-disconnect features or driver part of a surgical tool is usually machined on a Swiss-type machine before hardening; however, some of the notch tolerances are such that grinding has to be used to achieve these close requirements. Notch features include flats, hexagon with corner radius, plunges and recesses. Each handpiece manufacturer has a different design.
Using a 4-axis controlled CNC automated grinder with any number of linear and circular interpolations, notch designs can be produced with an astonishingly fast cycle time. As a dedicated system, the Rollomatic CNC235NM machine is extremely flexible for any plunge and flat grinding operations on shank ends of medical and dental instruments.
With the onset and spread of applicable CNC grinders, the manufacturing of surgical cutting tools has become competitive. This type of business has stayed in the USA, and there is little evidence of a wide-spread import of these tools. Automation, multiple machine cells and intimate knowledge of cBN wheel technology will further reduce the risk of this business going abroad, and if it does, it will only be for the purpose of supplying those markets directly.
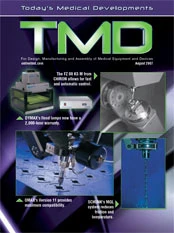
Explore the August 2007 Issue
Check out more from this issue and find your next story to read.
Latest from Today's Medical Developments
- How to Reduce First Article Inspection Creation Time by 70% to 90% with DISCUS Software
- FANUC America launches new robot tutorial website for all
- Murata Machinery USA’s MT1065EX twin-spindle, CNC turning center
- #40 - Lunch & Learn with Fagor Automation
- Kistler offers service for piezoelectric force sensors and measuring chains
- Creaform’s Pro version of Scan-to-CAD Application Module
- Humanoid robots to become the next US-China battleground
- Air Turbine Technology’s Air Turbine Spindles 601 Series