If you are looking for gear manufacturing equipment – such as gear cutting, forming and finishing, as well as broaching, shaping and slotting machines, you must visit the Gear Generation pavilion. In addition to traditional applications, gears are finding even greater importance in a large range of markets. » North Building |
Tool Grinder with Integrated Linear Motor
Engineered to profitably manufacture comp lex cutting tools, the Star PTG-6L tool and cutter grinder is a 5-axis, CNC controlled cutter grinder for grinding, sharpening, and reconditioning a wide variety of cutting tools. Manufactured in the United States, and equipped with a 6-station wheel pack changer, the PTG-6L is built for high productivity and precision. The PTG-6L features:
- Integrated linear motor and direct drive rotary technology
- Traveling tool platform for CNC steady resting and workholding adjustment
- Next generation NUM Flexium controller
- Latest enhancements in tool grinding software from NUMROTO
- Proven high volume loader
- Grinding wheel
auto-sticking
for unmanned operations
Also on display will be single-flute gundrill machines, multiple diameter carbide drills and reamers, the Bourn & Koch 100 H horizontal hobbing machine, and gear cutting tool solutions.
IMTS Booth N-6924
Star SU LLC
Hoffman Estates, IL
www.star-su.com
Turning, Grinding
The VL 2 P vertical turning machine can machine workpieces up to 100mm in diameter. It has two spindles, allowing one spindle to machine the workpiece while the second spindle automatically loads itself.
The VL 5i turning machine produces workpieces measuring up to 250mm in diameter in a single clamping operation. In addition to the pick-up working spindle with a rating of 28kW and a torque of 300Nm, the machine has an automation system with a revolving belt containing drag frames.
Also shown will be the VSC 400 DDS vertical grinding and turning center, which can machine complex chuck parts with a diameter of up to 400mm. Within a single clamping operation, the center can complete scroll-free turning as well as subsequent grinding processes.
IMTS Booth N-6846
EMAG LLC
Farmington Hills, MI
www.emag.com
Stick Blade Tool System
Featuring a carbide metal cutter for producing bevel gears and other internal gearing systems, the stick blade design offers optimal cutting geometry. In addition to the free design of the tool, tooth flank modifications can be applied by superimposing additional movements during the skiving process. The cutting edges move across the tooth flanks quickly and often, achieving a different surface texture than hobbing or shaping.
Arrangement of the tool and workpiece spindle is vertically, on both the Oerlikon C29 and C50 bevel gear milling machines, simplifying chip removal.
IMTS Booth N-6930
Klingelnberg AG
Saline, MI
www.klingelnberg.com
Sawing, Machining Center
The ACS + CFMcurve integrated sawing and machining center, features a proprietary sawing algorithm with a servo motor-controlled feed to continuously adjust critical sawing parameters during each cut. The CFMcurve machining center simultaneously machines each workpiece end using 12 independent servo-controlled axes. Machining options include: threading, boring, profile turning, grooving, radius edges, and angled chamfering. Bundles of mill length stock, up to 16.5m long, are placed in an automatic loader, individually separated, and fed to the sawing process.
IMTS Booth N-6737
Rattunde Corp.
Grand Rapids, MI
www.rattunde.com
Grinding Machines
The KX 500 FLEX incorporates a direct-drive work spin dle, tailstock support, and dressing spindles. The ZX 1000, the big brother of the KX 500 FLEX, shares common machine elements and software with the KX 500. The large ductile iron bed and torque motor for high-load capacity allows high-speed grinding of frac bull gears with a dressable worm tool.
IMTS Booth N-7036
Kapp Technologies Boulder, CO
www.kapp-usa.com
Range of Gear Hobbing Machines
Genesis models 210H hobbers accommodate gears up to 210mm in diameter, including those with shaft lengths up to 350mm. Features include: Siemens 840D controls, integrated chamfering and deburring, and a high-speed loading system to reduce load/unload cycles. Various cutting tools, including high-speed steel and carbide hobs, as well as a tool sharpening service are available.
IMTS Booth N-7000
Gleason Corp.
Rochester, NY
www.gleason.com
Gear Cutting
At maximum speed, the grinding and workpiece spindle positions are controlled with the precision drive electronic gearbox, enabling the use of multiple start grinding wheels for planetary pinions, which typically have a relatively small number of teeth, resulting in high workpiece speeds and tooth meshing frequencies. In addition, new grinding wheels make the RZ 60 possible to increase the cutting speed from the previous limit of 80m/sec to 100m/sec.
IMTS Booth N-7018
Reishauer Corp.
Elgin, IL
www.reishauer.com
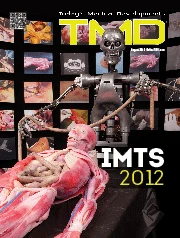
Explore the August 2012 Issue
Check out more from this issue and find your next story to read.
Latest from Today's Medical Developments
- Montagu to merge Tyber Medical, Intech and Resolve Surgical Technologies
- Americhem’s EcoLube MD PFAS-free internally lubricated compounds
- German robotics and automation in a downturn
- Blueshift’s AeroZero
- November USMTO grow from October
- Platinum Tooling’s custom and special tooling
- Top 5 global robotics trends 2025
- Accumold’s micro molding innovations