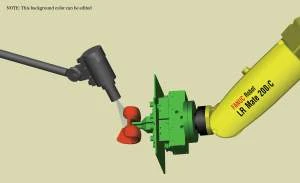
Blast cabinets are a common sight in most medical manufacturing plants where metalworking and machining processes are performed. In some operations, the fleet of hand-operated blast machines numbers in the dozens.
While some people may regard “sandblasting” as an unpleasant, but necessary process, the technology continues to evolve, and there are signs that media-blast equipment is poised for a major shift toward automation and robotics. According to many practitioners, there are compelling reasons for medical product manufacturers to move in that direction.
The prevalence of cabinet blasting is due, in part, to the wide variety of engineered shot and grit media now available, enabling blast techniques to be used for many different purposes. In fact, it is not unusual for an orthopedic implant component to receive selective or overall blast treatment several different times in the course of its production.
One of the most widespread applications in the production of medical equipment, implantable devices and surgical instruments is cosmetic finishing, in which media such as glass beads, ceramic shot or stainless steel beads are used to blend-in tool marks and superficial imperfections to produce an overall satin sheen appearance that prevents glare and reduces the reflectivity of surfaces. In some cases, such bead-blasting is a specified pretreatment for anodizing, plating or other chemical finishing processes.
Nondestructive blast cleaning is a common requirement for investment cast, forged, brazed, welded, heat-treated, laser-cut or laser-drilled medical components. Blasting can also be a fast and effective method of deburring precision components using non-abrasive or semi-abrasive media. Certain high-stress orthopedic components benefit from metallurgical shot-peening, for which specialized automatic blasting equipment is used.
Finally, abrasive blasting is a primary technology used to prepare surfaces for advanced coatings or critical bonding operations. In this type of technical surface preparation work, it is necessary to produce a specified surface texture or a measurable roughness so the blast system may have special features to ensure that the particular surface condition can be generated repeatedly.
Depending on the component and the purpose of blasting, the surface finishing results may be considered non-critical or absolutely essential. In either case, medical manufacturers hold themselves to a high standard of consistent quality.
SURFACE QUALITY
Considering many manufacturers’ reliance on manual blasting processes, a number of factors determine the quality of the blasted surface finish, including the media, the blast equipment and the technique of the operator.
Certainly, the purity and the physical characteristics of the blasting media are of basic importance, since the shot or grit particles actually do the work as they impact the surface. Great care is taken in the selection of appropriate media for each individual blasting application, and the media supply must be consistent to support the requirements of the quality system.
The performance of the cabinet-blasting equipment depends on many details of its design and fabrication, as well as proper adjustment and maintenance. To develop a comprehensive blast system specification, every element that affects media delivery, media reclamation and dust collection is carefully evaluated. Additionally, the blast machine builder is expected to incorporate all the necessary features to yield a blast process that can be validated.
In most cases, the blast system will contain, separate and re-circulate the blasting media, rather than discarding the shot or grit after a single use. The simplest of blast cabinets have the media delivery apparatus – whether suction-blast or pressure-blast – located at the bottom of the blast enclosure. Being the most economical of designs, it relies upon a dust collector to continuously draw off air-borne dust, but it does not have the ability to remove fractured media. So, when blasting performance and finish quality begin to decline, due to the presence of an excessively high percentage of fractional particles and contaminants, it is necessary to dump out and replace the entire batch of media.
To avoid the waste of frequent media change-out and maintain greater consistency in the shot or grit, most industrial cabinet-blast systems include a cyclone reclaimer that helps remove dust and fractured particles from the media mix by the difference in their mass. In the extraction zone of the cyclone separator, lighter broken media and dust are suspended in the central column and drawn-off to the dust collector, while heavier whole particles spiral down the cone to return to the media delivery system. Careful tuning of the air flow and vacuum in the cyclone separator and the dust collector balances the media reclamation system, enabling fines to be removed from circulation while a minimum amount of re-usable media is carried-over to the dust collector as waste.
For critical surface preparation and finishing work, where the greatest consistency in the sizing of media is desirable, the reclamation system can be enhanced by the addition of a vibrating screen classifier that sieves 100% of the media. Located below the cyclone in the reclaim stack-up, the classifier physically separates over-sized and under-sized particles so only shot or grit of the specified size is delivered to the blast gun, yielding a much higher degree of control of the blasted finish.
Advanced media delivery and reclamation systems may include electronic sensing of inadequate reclaim air flow, a full dust drum, detection of a low media level that might interrupt the flow of shot or grit, automatic replenishment of the media supply, and even automatic control of the media flow rate. Such features are designed to ensure that the integrity of the finishing process is not compromised.
BLASTING TECHNIQUE
Assuming the blast equipment is adequate, however simple or sophisticated, the factors that have the greatest effect on surface quality center on “the business end” of the machine, inside the cabinet, where the stream of media is directed at the workpiece.
The blast pressure is a key parameter, both because it determines the kinetic energy imparted to the surface in the impact treatment process and because excessive pressure can dramatically increase the fracture rate and attrition of media. Inadequate air pressure can mean insufficient energy to do the work, and pressure that is too high may result in damage to component surfaces. To ensure that the blast pressure is maintained within an established range, the media delivery system may be equipped with sensors to detect a loss of air supply pressure or advanced features to automatically regulate the blasting pressure.
The distance that the blast gun is held from the target surface has a direct affect on the intensity of impact energy, as well as the blast pattern or area of coverage. Holding the nozzle too close or too far away from the part can make the blast finishing process ineffective or alter the blast exposure time required to produce the desired finish. Whenever the most consistent finishing results are required, it is necessary to maintain a specific offset or stand-off distance between the blast nozzle and the surface of the component.
Another parameter that significantly influences the surface condition produced by blasting is the angle at which the gun is held in relation to the target surface. Media particles that impinge on the surface at the wrong angle can result in shadowing effects, where features of the part interfere with complete coverage. The blasting angle has an especially pronounced effect when grit media are being used to increase surface roughness and produce a specified profile or anchor pattern, since the height of the “peaks” and the depth of the “valleys” in the surface texture is heavily-dependent on the angle of media impingement.
The last factor of blasting technique that has a major impact on the quality of finishing results is surface speed. Assuming the correct blast pressure, distance and angle are maintained, the motion of the blast nozzle in relation to the target surface translates into exposure time or dwell. Close inspection of the surface finish often makes it obvious which areas of an individual component were under-blasted or over-blasted. Excessive dwell can have serious consequences in surface preparation work where sharp, angular grit media are in use, because of the potential for metal removal by the action of the abrasive, and because over-blasting tends to lower the roughness by wearing down some of the “peaks” that were created by earlier media impacts. A perfect surface texture for coating or bonding can be spoiled by one-too-many passes over the same area of the component.
In the case of medical manufacturers who depend solely upon manual blasting cabinets, control of these all-important fundamental parameters of the impact finishing process is, literally, in the hands of the operators.
An experienced employee – who has sufficient training and practice to master the required skills, and one who pays constant attention to blasting technique – can produce finishing results that are of satisfactory quality, especially when performing non-critical surface treatment operations. The big question is whether that result can be obtained on a regular basis on all the parts processed. Using visual inspection methods, it is frequently possible to spot the evidence of variation in angle, offset and surface speed when two identical components are compared side-by-side, or when different areas of the same component are examined carefully.
For the more critical blast finishing operations, manual blasting techniques may be considered an unacceptable source of cost and risks. Some manufacturers’ quality teams are taking aim at manual blasting operations to ensure compliance with ISO13485:2003, Section 8.5.3, regarding prevention of potential nonconformities in processing. To the extent that manual blasting harbors multiple sources of variation, it may be judged a problem area in terms of strict quality control.
AUTOMATED BLASTING
Traditionally, automated blast machines have been introduced when a high volume of components must be processed, when manual blasting represents a bottleneck in the flow of production, or when the cost of hand-blasting operations is excessive. Increasingly, however, medical manufacturers consider automated blasting as a way to eliminate variation in surface treatment processes and ensure consistent surface quality.
Depending on the geometry of the parts, the finishing application, the available cycle time and the flow of work, a variety of different types of automatic blast machines are used in medical component manufacturing, including tumble-blast, conveyor, rotary table and spindle blast systems. Selection of the appropriate type for a particular blasting application is a careful process, based on the user’s requirements.
No matter how the component is presented to the blast, in a conventional automatic air-blast machine, multiple blast nozzles can be pre-set at the correct angles and distances to achieve coverage of target surfaces. In some cases, blast guns in fixed position are adequate to the task. Motion of the guns, either oscillating or linear, allows coverage of a larger area with fewer blast nozzles and a lower compressed air requirement. When a precision linear actuator is used to provide horizontal or vertical nozzle motion under programmable logic control (PLC), the speed and stroke can be programmed as part of the process routine or recipe for each different component.
As compared to manual blasting, an automated blast system brings almost all of the key process parameters under control and provides a high degree of repeatability, so long as the geometry of the components is relatively simple. Bearing in mind the fundamentals of blasting technique, some parts can present a challenge for automated blasting with regard to blast angle, offset and surface speed. Of course, there are many non-critical blast finishing requirements where this limitation is of no consequence. However, when the shapes and contours of the components are complex, and the blasted surface finish is critical, a conventional automated blast system may not be able to meet all the medical manufacturer’s quality requirements.
ROBOTIC BLAST SYSTEMS
Robots have been used for a long time in medical component manufacturing, especially for machine tending and operations such as grinding, buffing and polishing. Indeed, a robot may be used to load and unload one or more automated blast systems in a finishing or coating work cell. The integration of robots into blasting machinery is a more recent development in the medical manufacturing environment, but it is one that may have far-reaching implications for critical surface finishing requirements in the future.
There are two types of robotic blast systems that may be of special interest to medical product manufacturers. In one type, the articulated robot arm manipulates the suction-blast gun, pressure-blast nozzle or an elongated lance nozzle. The end-of-arm tooling that actually holds the blast nozzle is designed to complement the robot’s motions in coverage of target surfaces, and it is robustly fabricated to withstand the action of blast media. The component may be fixtured on a rotating spindle or table that can be controlled as an additional axis of robotic motion, or the part may be mounted in fixed position that enables the nozzle manipulator to follow its contours.
In the other type of robotic blast machine, the robot grasps and manipulates the component, presenting the part to a blast nozzle that is locked in fixed position. This type of system normally requires custom designed end-of-arm tooling in the form of a gripper that will accommodate the full range of components to be blasted, and it utilizes what is called remote tool point motion programming. The gripper assembly typically incorporates a deflector plate to shield the end-of-arm tooling from media over-spray. The part-manipulating robot may be located in an antechamber between the load/unload station and the blast enclosure.
When mated with a blast machine, the robot is snugly fitted with a custom-tailored suit made of abrasion-resistant engineered fabric, to isolate the precision mechanism from the potentially harsh environment of the blasting chamber, without inhibiting its full range of motion.
ADVANCED ROBOT PROGRAMMING
While industrial robots are supplied with a teach pendant for development of motion programs, there is now a faster and more precise methods based on machine tool CAD/CAM technology. This is a significant breakthrough, since the many hours that a robotic blast system is tied-up during laborious, trial-and-error programming would be time that it is out of production.
The current state-of-the-art in robot motion programming utilizes 3D modeling software, beginning with creation of a parametric 3D model of the component that accurately represents all features of the part, as well as the end-of-arm tooling and structural features of the blast cabinet. The programming process is performed off-line, or even remotely, so production continues uninterrupted.
Parameters such as the distance from the nozzle to the part, the angle of the nozzle in relation to the target surface, and the speed at which the surface is traversed are set as rules of the CAD/CAM motion program. Unlike teach-pendant programming, the toolpaths of the blast gun are not based on the care and best reckoning of the programmer, but upon the most efficient execution of all the required nozzle movements. An added benefit is that the computer simulation of the blasting process yields an extremely dependable calculation of the blast cycle time.
BENEFITS OF ROBOTIC BLASTING
Robotic blasting and advanced motion programming will have a dramatic impact on surface quality. Even when blasting components of the most complex shape, the correct angle, offset and surface speed are constantly maintained. Operator errors in blast gun and part manipulation can be eliminated, and the limitations of conventional automatic blast machines can be overcome, resulting in a major improvement in the degree of consistency in quality.
Automated and robotic blast machines that use PLC control to synchronize system functions may be equipped with a variety of electronic sensors and enhanced control features that support compliance with stringent quality standards and simplify validation of the blasting process. For example, in addition to monitoring and display of conditions such as media level, blast pressure, spindle rpm, media flow rate and nozzle motion, advanced systems can be designed with component recognition, data acquisition and logging capability to assist with documentation of critical process parameters.
There are many more advantages of robotic blasting that appeal to those who engineer and produce medical components. One of the foremost is that, once a complete process recipe is established for a particular component, it can be stored and recalled at will, and the need for most blast machine set-up and adjustment procedures is eliminated, no matter if a short or long run of a particular part is required.
Other obvious benefits of the conversion to robotic blasting are labor and re-work savings, and the fact that human operators are freed for other work that demands their intelligence and judgement. By the elimination of wasted motion, process cycles can usually be reduced to a fraction of the time required for manual blasting. For an identical surface treatment, a single robotic blast system can out-produce several hand blast cabinets.
Any process equipment change in medical manufacturing operations entails many costs related to validation, in addition to the investment in new machinery. In the cost/benefit analysis, the value contributed by robotic blasting in terms of product quality and production efficiency compares very favorably for critical surface finishing applications.
Guyson Corp.
Saratoga Springs, NY
http://www.guyson.net

Explore the July 2009 Issue
Check out more from this issue and find your next story to read.
Latest from Today's Medical Developments
- Global Industrie - A meeting to understand, anticipate and contribute to the industry of tomorrow
- Wintriss’ Tracker Hardware Solution for ShopFloorConnect Production Tracking Software
- Protolabs expands end-to-end manufacturing capabilities
- Sunnen’s HTE-1600W Tube Hone
- Researchers invent soft, bioelectronic sensor implant
- HEULE’s DL2 tooling
- Application Park shows off diverse robotics applications
- Join our editors for a look at the manufacturing industry in 2025