
Known for their superior-yet-flexible strength in bond, foam tapes have been replacing screws, rivets, welding, and other permanent bonding solutions. They are lightweight, soft, conformable, versatile, durable, aesthetically pleasing, easy to use, and cost-effective – offering adhesion and meeting intricate, specialized bonding needs for countless medical devices.
And, foam tapes aren’t going anywhere. According to the recent “Medical Adhesives: Markets and Opportunities” report by Technology Assessment Associates, the medical industry’s use of adhesives – including foam tape solutions – is dramatically growing. The report suggests medical device manufacturing is currently a $44 billion market and is growing annually by 12%. As medical devices become smaller and more complex, greater demands are being made on the materials and components used in medical devices. So, as one of the more flexible adhesive components available today, foam tapes will continue to be a solution of choice in medical device assembly – especially double-coated foam tapes, one of the fastest-growing attachment methods.
Double-coated foam, which features adhesive on both sides, offers a strong bond – connecting irregular surfaces and low-surface-energy substrates such as polyethylene and polypropylene. It can also offer benefits such as resistance to heat, chemicals, ultraviolent (UV) light, and water as well as added cushioning, dampening, and sealing. Tapes allow flexibility in device design to meet varying adhesion requirements.
However, with so many foam tape options, choosing the most ideal tape can be challenging. Additionally, some tapes may appear to be a good choice on the surface, but when factored more closely into the application, they may not be the optimal choice. To ensure product development success, medical device manufacturers should invest in strong supplier partnerships that include:
1. A trusted adhesives supplier – Medical-grade adhesives for foam tapes are not typically off-the-shelf products. An ideal tapes/adhesives supplier will offer product customization. For example, some of the latest foam tapes are more biocompatible than others and certain adhesives can better withstand autoclave, gamma, and ethylene oxide (EtO) sterilization.
To achieve the exact formulation and combination required for a specific medical device application, manufacturers should work with an adhesives supplier with expertise in medical-grade adhesives. The supplier should offer flexibility when it comes to custom-matching adhesives to foam materials. The best suppliers are those who are not limited to stock products, can change adhesive configuration quickly and cost-effectively, and can meet the medical industry’s varying regulatory standards – following strict process guidelines such as current Good Manufacturing Practice (cGMP), International Organization for Standardization (ISO), and Food and Drug Administration (FDA) guidelines for direct-skin adhesives.
2. Experienced converter – The converter supplier should be able to deliver advice in materials selection and identify the best foam tape for the application. Based on an application’s need, a converter should be able to recommend whether or not a single- or double-coated tape would be better and which adhesive liner would be best.
To meet the specifications of medical device components, ideal converters should offer a selection of die-cutting processes, such as rotary, laser, and waterjet. Waterjet technology can deliver cleaner edges and minimized distortion. Other die-cutting considerations for medical applications include laser, kiss-cutting, slitting, and laminating. To garner additional benefit, manufacturers should seek a converter that can print tamper-evident labels and custom pressure-sensitive labels for medical devices.
3. Industry players who partner with one another – Selecting suppliers who meet device assembly needs and can partner with one another can prove extremely beneficial. In medical device assembly, these important partnerships specifically include adhesives suppliers and designers, as well as designers and packaging suppliers. Design and packaging are on opposite ends of the medical device assembly spectrum, but when considered together, they can enhance problem-solving abilities, increase speed-to-market, and smooth the product development process.
Packaging solutions should consider a product’s fit, form, function, and design. If suppliers are abreast of packaging requirements early and often throughout development, they can increase product flexibility and identify pre-existing issues. For example, recognizing the needs of device components throughout their shelf life is critical in both the design and packaging phases of development. An electrocardiogram (EKG) pad, for instance, commonly features a foam tape and often contains a hydrogel or a polymer that expands in water, allowing the components to conduct electricity. Moisture stability in packaging is crucial because if the hydrogel loses too much moisture, the conductive process is impaired and the pad cannot accurately monitor a patient’s heart rate.
Other special packaging needs may include protection of internal device components or oxygen or light barriers. While foam tapes are often resistant to UV light, the tapes’ release liners may not possess the same qualities. UV light can cause polyester-release liners to degrade and polyurethane liners to change color.
Sterilization is another consideration. Often determined in the design phase, sterilization methods impact heavily on the type of packaging materials used. For example, a flexible film packaging solution will not perform well for products that require ethylene oxide (EtO) sterilization, where the chosen substrate needs to be more porous for effective permeation.

Reliable partners
Knowing that foam tapes will continue to be a driving component of medical device assembly for years to come, medical device manufacturers should continue looking ahead – and seek out reliable industry supplier, design, and converter partners.
Teaming up with reputable, trusted partners can avoid adding expense through over-engineering, can provide quality assurance by cultivating and demonstrating good process controls and strong customer service, and enhance product resources and capabilities, reducing overall costs and improving final product design.
Mactac LLC
www.mactac.com
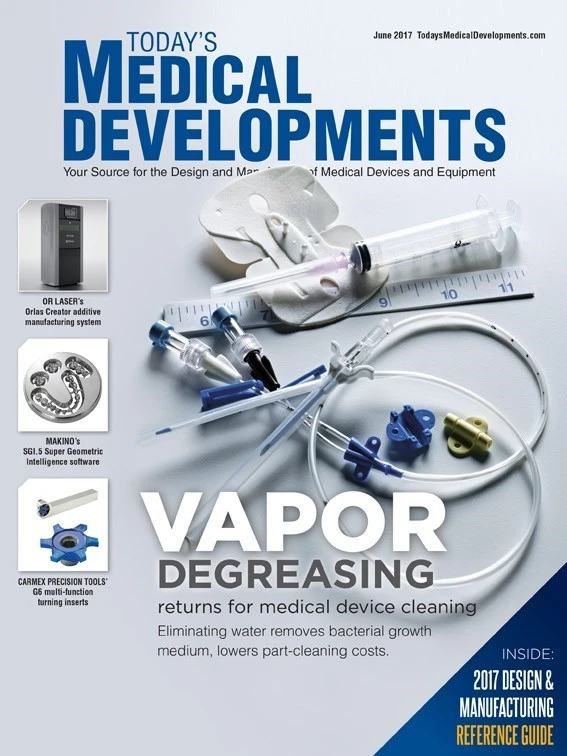
Explore the June 2017 Issue
Check out more from this issue and find your next story to read.
Latest from Today's Medical Developments
- Incredible Machine works on the Rube Goldberg principle
- FAULHABER’s metal planetary gearhead family
- Aerospace Industry Outlook - Spring 2025, presented by Richard Aboulafia
- World’s smallest pacemaker is activated by light
- FANUC America’s ready-to-deploy cobot web tool
- #42 Lunch + Learn Podcast - Quell Corp
- Siemens accelerates path toward AI-driven industries through innovation and partnerships
- REGO-FIX’s ForceMaster and powRgrip product lines