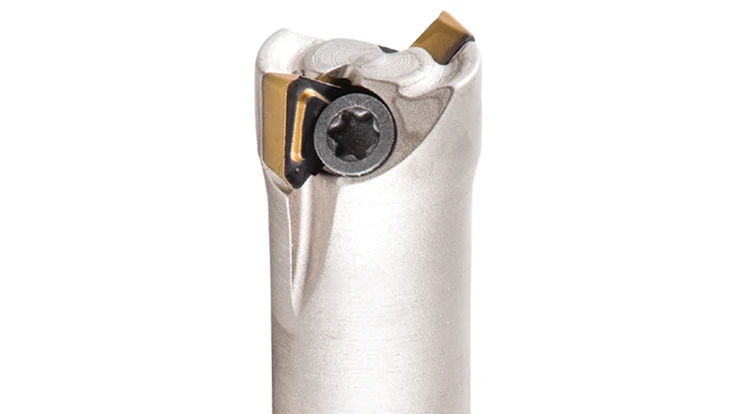
Iscar
Many medical devices are currently produced on a Swiss machine due to the ability to effectively turn, drill, and mill. Although the materials being used to produce medical components have, for the most part, remained the same for some time now (cobalt-chrome, 17-4PH, titanium), recent cutting tool developments are improving overall productivity related to milling applications used in the production of medical devices on Swiss machines.

1. How can manufacturers address the tight space challenges that go hand-in-hand in Swiss machines/ applications?
One solution comes from Iscar’s Multi-Master system. Shanks designed with the typical ER collet back end have been built as an integral component. The result is a highly rigid and accurate milling assembly, with extremely short gage length, excellent accuracy/repeatability, and quick-changeability.
2. What sort of accuracy/ repeatability can be expected from the Multi-Master system?
Axial accuracy is controlled to 0.0004" and radial total indicator reading (TIR) does not exceed 0.0007". This is due to a ground connection, combining a conical taper and threads which seat (or pull) the interchangeable/replaceable head into a connection designed for a slight interference fit. This is a big difference between many modular tooling systems that have to rely on a clearance fit between connections.
3. How does Iscar address milling extremely small part features on medical components?
There are two solution categories: solid carbide and indexable. Solid carbide end mills that could be categorized as micro sized have existed for years. Typically referred to as rib-processing mills, they offer a wide selection in diameter range – from 0.1mm to 6.0mm (0.0039" to 0.2360") – and varying lengths of cut to keep tiny tools working as effectively as possible. For example, a 1mm tool has eight different length options. Indexable tools are now available from Iscar with nano and micro inserts. These inserts will prove to be an excellent fit for the Swiss environment where small depths of cut are the norm and the use of a solid carbide end mill is wasteful.
4. How easy are small indexable tools to change in extremely tight spaces in Swiss machines?
One of the main strengths of the Multi-Master system is quick changeability. For example, a redundant head can be in queue. When the end of tool life is reached, the machine operator quickly switches to the new head, and the head with used inserts is taken to a bench where insert indexing is easily performed. This approach keeps the Swiss machine up and running with a much lower chance for errors.
5. What other cutting tool developments have positively impacted the ability to mill difficult medical device materials?
One of the biggest changes/impacts I’ve had recent experience with was the implementation of an end mill with a new coating, that we call IC702. The coating and substrate form an extremely hard and wear-resistant combination when compared with typical coatings. Without giving away too much information, we replaced our own product with the new technology and, without any changes to cutting parameters, the customer produced double the amount of parts.
Iscar USA
https://www.iscarusa.com


Explore the August 2018 Issue
Check out more from this issue and find your next story to read.
Latest from Today's Medical Developments
- Tariffs threaten small business growth, increase costs across industries
- Feed your brain on your lunch break at our upcoming Lunch + Learn!
- Robotics action plan for Europe
- Maximize your First Article Inspection efficiency and accuracy
- UPM Additive rebrands to UPM Advanced
- Master Bond’s LED415DC90Med dual-curable adhesive
- Minalex celebrates 60 years of excellence in miniature aluminum extrusions
- Tormach’s Chip Conveyor Kit for the 1500MX CNC Mill