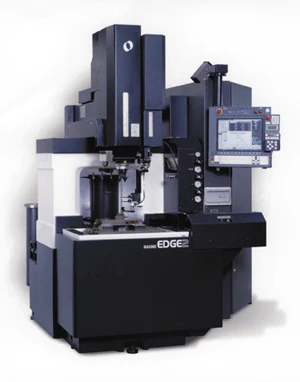
Makino's EDGE2 Ram EDM machine with a fine-hole option is capable of burning holes as small as 0.0012-in. using tungsten rods that are 0.0008-in. in diameter. With the use of 0.0008-in., sapphire die guides and a high-speed spindle, length-to-diameter ratios of 10-1 and 15-1 are achievable. Furthermore, with Makino's high-pressure pump system capable of pressures up to 1,450 psi, the EDGE2 Fine Hole machine provides reliable flushing through copper pipe electrodes as small as 0.004-in., making it possible to achieve length-to-diameter ratios greater than 25-1.
The machine can be converted from a fine-hole function to standard RAM EDM functions in less than 5 minutes without changing dielectric fluid. In addition, the EDGE2 Fine Hole machine is capable of 60 amp burning with full orbiting capabilities.
The orbiting capabilities make it possible to size and shape specific hole diameters. This allows users to generate tapered or flared holes that can be square at the opening and round at the exit. According to Makino, in a recent test, a series of 6 holes were burned 0.100-in. deep with a 0.004-in. diameter copper electrode, resulting in holes having an entrance burn of 0.0048-in. and an exist burn of 0.0045-in.
The EDGE2 Fine Hole machine can be ordered with an 8, 16, or 24-station automatic tool changer, which is capable of changing electrodes with diameters as small as 0.004-in. The machine can also be ordered with an automatic guide changer having the capacity to hold 6 different die-guide sizes. This allows users to program the burning of up to 6 different hole diameters with 24 different tools.
Other standard features of the machine include an MA rotating head capable of standard 10 to 1,000 rpm rotation; a high-performance Z-axis spindle capable of a 400-ipm high-speed jump; an automatic fire extinguisher to protect the operator, workpiece, and machine; and a fixed table that eliminates dielectric weight shift during machining and improves servo reaction and precision. According to the company, rounding off these features is Makino's drop-tank design with zero fill time and dielectric chiller. The drop-tank improves many aspects of the EDM process, as the retractable tank walls provide wide-open table access for safe, simple slide-on loading and faster, more accurate setups. In addition, the adjustable tank depth allows optimal matching of dielectric fluid level to workpiece size.

Explore the November 2005 Issue
Check out more from this issue and find your next story to read.
Latest from Today's Medical Developments
- You can still register for March’s Manufacturing Lunch + Learn!
- HERMES AWARD 2025 – Jury nominates three tech innovations
- Vision Engineering’s EVO Cam HALO
- How to Reduce First Article Inspection Creation Time by 70% to 90% with DISCUS Software
- FANUC America launches new robot tutorial website for all
- Murata Machinery USA’s MT1065EX twin-spindle, CNC turning center
- #40 - Lunch & Learn with Fagor Automation
- Kistler offers service for piezoelectric force sensors and measuring chains