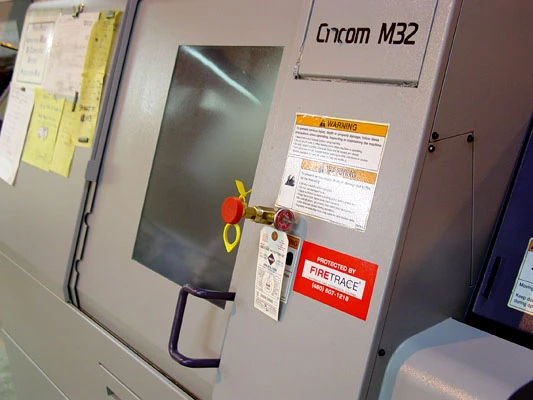
CNC machines have become a fixture in medical manufacturing facilities worldwide. However, many manufacturers are finding that fires while turning in titanium remain a constant, and all-too-common, danger.
However, for those manufacturers who are turning these parts in high-speed, hydrocarbon-cooled applications, there is a misconception that the fires are occurring in the titanium.
While a small percentage of these fires begin with the titanium, the vast majority of fires actually begin in the coolant oils, where the flash point of the oil is typically less than half of the flash point of titanium. Typically a fire starting in the coolant oils will grow and become hot enough to ignite the metal. The key is to catch the fire quickly, before the heat can build.
Local fire authorities often dictate sprinkler systems in shops, however building sprinkler systems were not designed for machine-level protection. In most cases, a machine will be fully engulfed in fire (and with it the titanium) before a building system will activate, and of course adding water to a titanium fire creates an explosive situation.
The trick is to bring the fire detection and suppression into the micro-environment within the machine itself. In the 90s a movement began in the fire industry where the concept of protecting critical, high risk enclosures was beginning to be embraced, and with the acceptance of the concept came new way of thinking about fire detection and suppression systems.
Most fire equipment manufacturers simply scaled down versions of their larger systems, however the cost of the systems ultimately could not be reduced in proportion of the size of the system in part due to reliance on components such as control panels and detectors. Ultimately, the cost of these systems still made them impractical for most shop owners, and manual suppression remained the primary mode of fire control. Thanks to some out-of-the-box thinking by engineers, new approaches were sought to protect these spaces cost-effectively. One of these solutions, by Firetrace , relies upon a fire-sensitive tube as detection for a fully pneumatic fire suppression system that can react in under 10 seconds with suppression in less than 15 seconds using a clean agent such as CO 2 or FM-200.
With this quick detection and suppression, the oil fire is quickly suppressed, inhibiting the ignition of the metals. Additionally, the clean agent used requires no cleanup and will not contaminate the coolant oil. After rectifying the cause of the fire, most machines can be immediately returned to service. Now these new systems are not designed to replace code-mandated sprinklers -- these systems are known as supplementary fire suppression systems. However, those who have experienced the damage done by a machine fire, and perhaps the collateral damage of a sprinkler system will see machine-level suppression as necessary rather than supplemental. Between job deadlines, insurance costs, productivity issues and safety, more and more shop owners are opting for suppression systems that not only protect the facility, but also machines as well. Be certain that you are aware of the options available to your to protect your shop.
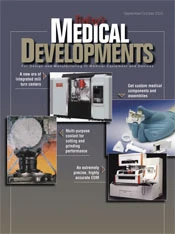
Explore the September 2005 Issue
Check out more from this issue and find your next story to read.
Latest from Today's Medical Developments
- Turnkey robotic systems are already behind the times
- You can still register for March’s Manufacturing Lunch + Learn!
- HERMES AWARD 2025 – Jury nominates three tech innovations
- Vision Engineering’s EVO Cam HALO
- How to Reduce First Article Inspection Creation Time by 70% to 90% with DISCUS Software
- FANUC America launches new robot tutorial website for all
- Murata Machinery USA’s MT1065EX twin-spindle, CNC turning center
- #40 - Lunch & Learn with Fagor Automation