
Rifton Equipment designed and brought to market a seating system called the Activity Chair. Used in therapy, feeding, and activities, the chair features a height adjustable base, allowing vertical position changes while the person remains seated.
Though Rifton has been making chairs for those with disabilities since the 1970s, its first production models – though unique at the time – were primitive plywood box frames covered with slots and knobs for adjustment. Through the years, as therapists’ input and suggestions flowed in, company designers continued to modify and improve on the original idea.
Using this methodology, Rifton’s designers determined early in the design process that they would need to separate the seat from the base so they could offer options that would meet a range of needs from children needing minimal support up to children and adults needing full support. They worked through the mechanical details and developed design prototypes of what they thought would work well. Each revision of the prototypes required additional field-testing and input from therapists.
Enhanced activity, durability, safety
At Rifton, the critical goal is a product that enhances activity and motion for people with disabilities while offering durability, ease of use, and safety. Every major component goes through a battery of tests designed to replicate the life cycle of a typical special-needs product in the field.
Design of the Activity Chair was to provide many support options while allowing as much freedom of motion as possible. An emphasis was placed on forward leaning, dynamic seating, and ease of transfer to standing. The Activity Chair’s base allows the caregiver to make adjustments quickly and easily, depending on the activity required.

“One of the required features was a base that allowed height adjustment with a 225 lb client in the chair,” says Kirk Wareham, Rifton’s director of product design.
This was done using a foot-operated hydraulic linear actuator pump, which was ultimately outsourced to Carr Lane Roemheld Mfg. Co., after an initial period with another supplier.
“After acquiring samples and submitting them to an exhaustive validation/testing process, we determined that the new product was actually an upgrade on several fronts,” Wareham says, adding that it offered a smoother, more consistent operation, as well as better paint quality and a higher success rate. “Prior to making a final decision, we then paid a visit to the Carr Lane Roemheld facility in Fenton, Missouri, in the hopes of establishing a strong and long-term relationship.”
Keeping costs down
Another strong determining factor was price. While the pump from the original supplier functioned well, it was costly.
“We felt it was only responsible to reduce our costs where possible, and ask for a price reduction commensurate with the dramatically rising sales of the Activity Chair,” Wareham says. “Also, since we pay our bills promptly, we are typically granted an early-pay discount. We were disappointed to find that the previous supplier would not even entertain a discussion on either point. There were also some minor quality issues. An additional driver of the project was the hope to reduce the amount of inventory held in our warehouse.

“Carr Lane Roemheld offered a price that would save us a significant amount of money. They also made some minor design modifications to meet our requirements, including custom packaging specifications. Because Carr Lane Roemheld agreed to hold stock for us, and to deliver on a one-week lead-time, we were able to reduce our inventory by more than $100,000. We also received a visit from an engineer from their manufacturing plant in Germany, to review quality expectations and design features,” Wareham comments.
The linear actuators were integral to the Activity Chair’s ability to provide key range-of-motion advantages to children and adults with disabilities.
“The most rewarding part of the design process comes at the end when we make our final round of field trips just before going into production,” says Sam Durgin, Rifton’s project design leader. “I’ll never forget watching a little girl in New Jersey smile when she had access to a sink for the first time, or the appreciation from the teacher who could quickly position her child with special needs to join her peers for circle time at floor level.”
Many similar stories about enhanced abilities have continued to make the Activity Chair a big advantage to caregivers as well as disabled patients of every age. Wareham appreciated the value Carr Lane Roemheld brought to the design process.
Supplier relationships are often critical to the advancement of any product line, and the two companies found success by working together to provide a high quality product, while finding ways of value that did not lessen that quality.
Carr Lane Roemheld Mfg. Co.
About the author: David Vilcek is the manager of workholding and assembly at Carr Lane Roemheld Mfg. Co. He can be reached at 636.386.5307 or dvilcek@clrh.com.
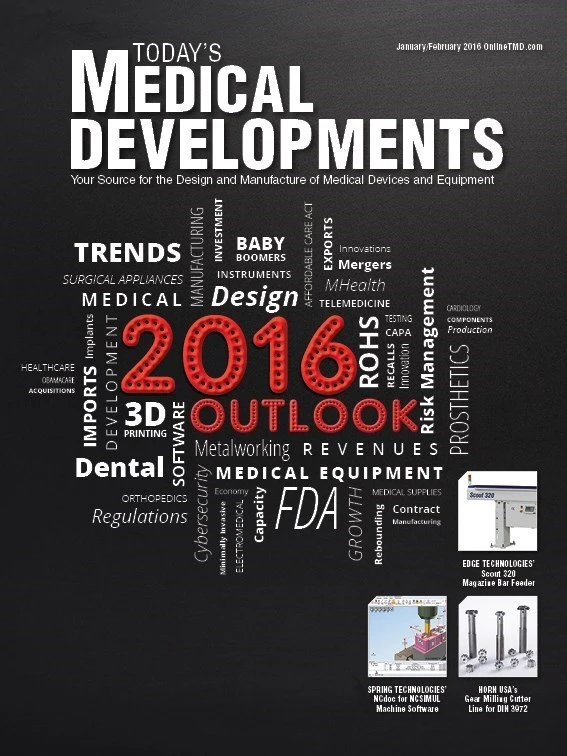
Explore the January February 2016 Issue
Check out more from this issue and find your next story to read.
Latest from Today's Medical Developments
- Best of 2024: #4 Article – Sticking to the basics
- Best of 2024: #4 News – Point of care manufacturing
- Best of 2024: #5 Article – Accelerating medical device development with freeform injection molding
- Best of 2024: #5 News – Complexity, the enduring enemy of medical cybersecurity
- Best of 2024: #6 Article – Closing the global product information gap
- Best of 2024: #6 News – NUBURU enters medical device market with order Blueacre Technology
- Season's greetings
- Best of 2024: #7 Article – Synchronized machining processes for medtech