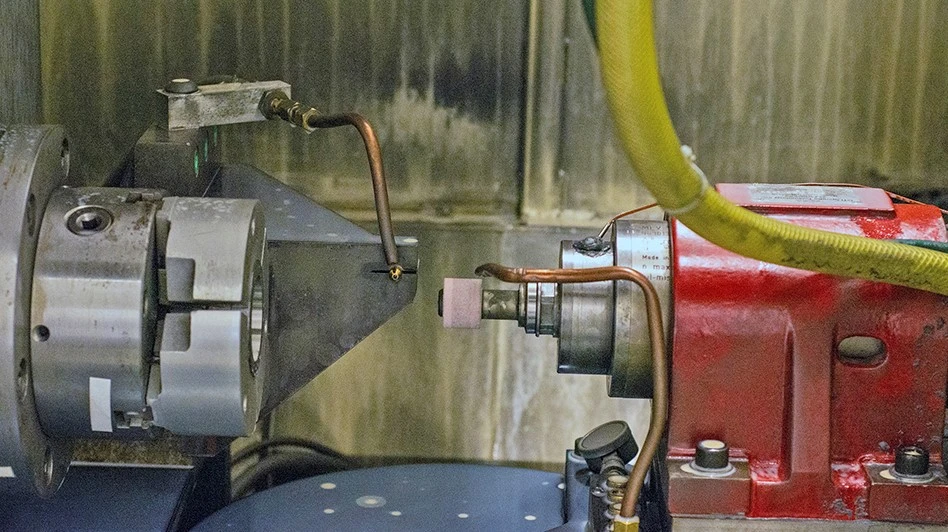
Coventry Associates

Shrewsbury, Massachusetts-based Coventry Associates has developed a 3-axis system for a variety of machining operations. Called the Eccentric Positioning System (EPS), this fully electric system, eliminates pneumatics and hydraulics, reduces setup and cycle time, uses less energy, has a smaller footprint than any existing system of machining, and is offered at a competitive cost, according to Craig Gardner, president of Coventry Associates.
EPS is a mechatronic system that consists of a stack of three eccentric rotary tables. By controlling the rotation of each rotary table, the precise position and angle of a tool is achieved. The positioning accuracy and adaptive performance of the EPS system is enabled by the Siemens Sinumerik CNC.

EPS has already been incorporated into an ID grinding machine where it has demonstrated that it can do three things that no one else in the industry can do. First, it can dress or grind any shape without the use of diamond rolls or special dressing attachments. Second, it can grind by adaptively controlling the normal grinding force rather than the feed rate which dramatically improves material removal rates. Third, it compensates in real time for deflections that result in workpiece diameter and/or taper variation, improving both quality and throughput.

“It has potential applications in all grinding and turning operations for the machine tool industry,” Gardner states, further observing that the EPS will be made suitable for any machining operation that requires a combination of high positioning accuracy and controlled force.
Coventry’s launch product, EPS SingleTool, is designed for bearing ID grinding operations, using a single wheelhead. A shoe or chuck workhead can be used, with single point or rotary dresser for shaping any contour. Power consumption is 10kW max. and the weight is 630kg, with exterior dimensions of 305mm x 660mm x 560mm.

Coventry validated the positioning performance of the EPS SingleTool using a laser interferometer to measure its resolution, accuracy, repeatability, and straightness capability. Because of the unique kinematics of the EPS, all motions are three axis interpolated moves. The results of these measurements are shown in Table 1. These measurements show state of the art positioning capability with a repeatability of 52nm. The system also has high static and dynamic stiffness as well as the ability to grind with large forces and make rapid motions to minimize the time required to make non grinding motions.
Figure 3 shows accurate steps and repeatability without backlash in 0.125um steps over a total travel of 5µm

Figure 4 shows the X deviation or “straightness” achieved during three back and forth (six passes total) Z-axis moves. This data shows that the difference between the maximum and minimum values for all six passes was less than a micron over 200mm of travel.
Similar results were obtained for the X axis straightness as shown on Figure 5.
Coventry worked closely with the Fraunhofer USA offices in Boston, Massachusetts, plus two key partners, Saint Gobain Abrasives and Siemens Industry Inc., to develop the initial SingleTool ID grinding application.

“Our business strategy is to bring the EPS to market as a hardware and software solution, either as a complete machine to end users or as a platform for machine builders. Our solution features all-electric operation, using no pneumatics or hydraulics. We typically see resolution less than 0.12 microns with 0.05 microns repeatability, plus linear accuracy to 0.12 microns with consistent static and dynamic stiffness to a maximum grinding force of 3.34kN. Rapid motion, including acceleration and deceleration, is tracking a 203mm movement in 1.16 sec,” Gardner explains.
Latest from Today's Medical Developments
- Ferrocene becomes first Rust toolchain to achieve IEC 62304 qualification
- Germany expects a major decline in production in 2025
- Learn what you need to comply with CMMC requirements
- VersaBuilt’s CNC automation possibilities
- ROBOTICS AWARD 2025
- There’s still time to register for this week’s manufacturing industry webinar!
- Arterex acquires Phoenix S.r.l., a leading Italian medical device solution provider
- FAULHABER’s expanded portfolio of high-performance DC motors