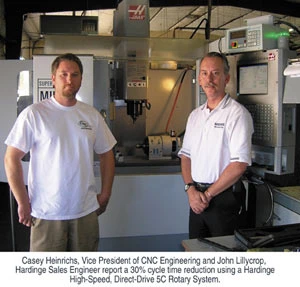
CNC Engineering, Lake Elsinore, CA, manufactures tight tolerance, high quality parts for industries requiring high precision work. Some production runs are for 10,000 pieces or more. The company has been in business for 21 years, performing both CNC milling and turning.
Recently, CNC Engineering purchased a Haas Super Mini Mill and was using an existing Haas indexer on one of the jobs running on this mill. Dave Ahlberg, the local salesman for Hardinge's distributor, Machinery Sales Co., introduced Hardinge's new High-Speed Direct-Drive 2,150o/sec rotary system to Casey Heinrichs, Vice President of CNC Engineering. Heinrichs expressed an interest in knowing more about the machine. John Lillycrop, Hardinge's Western Region Workholding Sales Engineer, explained, in detail, the features and benefits of the new Hardinge DD100 Direct-Drive Rotary System with an A2-5 5C colleted spindle.
Features that interested Heinrichs were the 2,150o/sec indexing speed; the rigidity of the spindle provided by the high precision cross roller bearing system; the high accuracy provided by the +/- 2 Arc Second Renishaw encoder that is directly mounted to the spindle; and the ZERO backlash that is made possible by the spindle mounted direct-drive rare earth torque motor. Hardinge developed the high-speed system to match the fastest axis travels available in the industry on high-speed mill/drill machines so that these high-speed machines would not have to waste time waiting for the indexer to position.
PRODUCTIVITY GAIN
Heinrichs shared the productivity gain he has experienced with Lillycrop and with Joe Colvin, Hardinge's Vice President of Workholding. A particular job was being run on the Haas Super Mini Mill using the Hardinge DD100 Direct-Drive System, being controlled by Hardinge's Programmable Digital Servo Control Box, and being coordinated with the CNC control through the use of an M-code for start and finish signals. By using the Hardinge DD100 Direct-Drive System, the cycle time on this part was reduced from 30 seconds to 23 seconds from the 2,150o/sec indexing speed. This reduction in cycle time saves CNC Engineering 19.4 hours on a 10,000-piece production run.

Hardinge 100/5C Direct-Drive High- Speed Rotary System accepts collets,step chucks, expanding collets, faceplates and jaw chucks to grip most anypart.
Heinrichs is pleased with the Direct-Drive Rotary System and believes that he will be able to reduce cycle times on the majority of his other jobs. He is also impressed with the accuracy and zero backlash of the system. He clearly sees the benefits of those features on many of his jobs. Colvin states that there will be no accuracy loss over time because there is no worm and gear to wear in a Direct-Drive System.
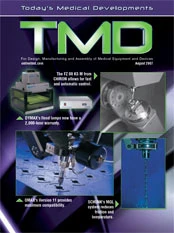
Explore the August 2007 Issue
Check out more from this issue and find your next story to read.
Latest from Today's Medical Developments
- LK Metrology acquires Nikon Metrology’s laser scanning and Focus software assets
- Flexxbotics’ robot compatibility with LMI Technologies 3D scanning, inspection products
- IMTS 2024 Booth Tour: Behringer Saws
- UNITED GRINDING Group to acquire GF Machining Solutions
- Mitutoyo America’s Metlogix M3 with the Quick Image Vision System
- IMTS 2024 Booth Tour: Belmont Equipment & Technologies
- Krell Technologies launches Photonics Outreach Program
- Hurco’s TM8MYi lathe