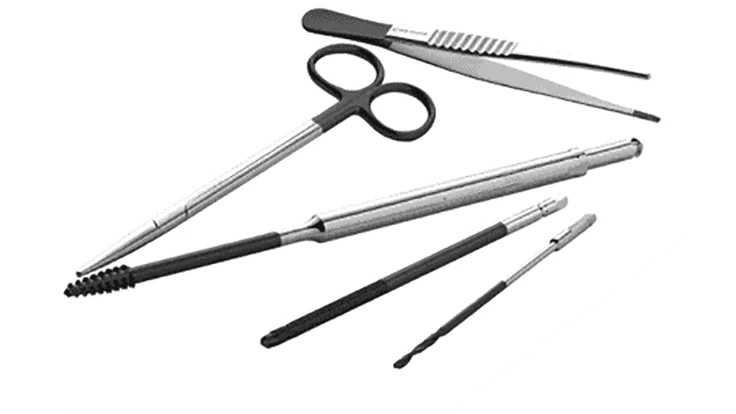
OERLIKON BALZERS

Diamond-like carbon (DLC) wear-resistant thin film coatings can protect instruments and medical devices subject to high loads, extreme friction, wear, and contact with other parts. The high hardness of a DLC coating – along with a low coefficient of friction – can prevent parts from pitting, galling, seizing, and ultimately failing in the field.
DLC coatings can be highly engineered based on hydrogen content (hydrogenated or hydrogen-free), selection of additional metallic and non-metallic doping elements, presence of sub-layers, and choice of deposition and bonding methods. These factors can be precisely controlled to create a broad range of thinly applied (1µm to 5µm) DLC coatings with 8GPa to 80GPa hardness or higher (diamond is measured from 70GPa to 150GPa). The desired coefficient of friction, surface finish, and application temperature can also be manipulated.
Because of the broad range of customizable attributes possible, DLC coatings can play an important role in component engineering early in the design process.
A coating is a sophisticated design element with highly engineered properties, specifically tailored to meet the performance requirements of different operating conditions. As such, coatings should not be a design afterthought.
Hydrogenated amorphous carbon coatings

The most widely known DLC coating type, hydrogenated amorphous carbon (a-C:H), is most often applied through plasma-assisted chemical vapor deposition (PACVD). This deposition method causes a chemical reaction through plasma excitation and ionization that creates a coating hardness of approximately 15GPa to 30GPa.
However, an a-C:H coating can be manipulated further through doping – adding chemical elements to alter performance properties. Silicon, oxygen, or metals can be used as doping elements to achieve different results.
When a lower coefficient of friction is required for mated or sliding parts, or to assist in releasing items from cavities or molds, silicon doping can create an a-C:H:Si coating with 15GPa to 20GPa hardness. Silicon and oxygen doping can also achieve high electrical resistivity and chemical inertness.



Hydrogen-free DLC coatings
Hydrogen-free coatings provide even higher hardness along with a very low coefficient of friction.
Most hydrogen-free coatings are applied using physical vapor deposition (PVD) by arc evaporation, which produces tetrahedral amorphous carbon (ta-C). With a high level of tetrahedral bonds (50% to 60%), ta-C coatings have higher abrasive wear resistance than a-C:H alternatives.
With a typical hardness up to 60GPa, ta-C coatings are an excellent choice for components that are exposed to extreme operating forces throughout long-term use. This includes shafts and seals that must work in tribological environments, where friction can cause them to overheat and fail.
The challenge with hydrogen-free coatings, and with ta-C deposition in particular, is that the application process produces small droplets that contribute to a rougher surface finish. Coating manufacturers must complete secondary polishing processes to smoothen the surface. The material’s hardness makes this a time-consuming and expensive process that requires specialized equipment.
Some hydrogen-free DLCs are produced using a filtered cathodic arc deposition method, in which an electromagnetic filter removes most droplets. Although this creates a smoother surface, secondary polishing is still often required, and process times are longer for the same coating thickness.
Pulsed plasma
When an even smoother surface is required, hydrogen-free DLC coatings can be applied using scalable pulsed power plasma (S3p) technology developed by Oerlikon Balzers. Dense plasma yields hard coatings with high adhesion at a level comparable to arc evaporation. At the same time, the sputtering process – in which atoms are ejected from a target or source material – creates smooth coatings.
The coating is applied at a relatively low temperature – far less than 200°C – compared to up to 350°C for other DLC coatings. This enables the application to bond with aluminum, steel, and other substrates.
Medical instruments and other small, precision tools can benefit from hydrogen-free DLC coatings applied using the S3p process Baliq Carbos.
At the top end of the hardness scale are diamond coatings applied by a chemical vapor deposition (CVD) process in micro and nanocrystalline options, rated at 80GPa to 100GPa. These coatings are mainly used for highly specialized tools for cutting demanding materials, such as carbon reinforced fiber materials, and don’t offer the benefit of low friction.
Coating design
Given the variables involved with DLC coatings, it’s important that OEMs understand the range of options so they can select the ideal solution for an application while also taking economics into consideration. Coatings are effectively an architecture of layers engineered to achieve specific properties. A coating is built layer-by-layer and focused on bonding, hardness, and surface. By modifying the properties of each, the DLC coating family offers an extremely wide range of surface solutions. Additionally, all Oerlikon Balzers’ DLC coatings are biocompatible, making them suitable for medical instruments.
DLC coatings increase a component’s surface hardness and durability and reduce the likelihood that essential parts will fail. Maintenance and unexpected downtime fall dramatically, even in the most demanding environments with high friction, wear, and contact pressure.
Oerlikon Balzers
https://www.oerlikon.com/balzers

Explore the September 2020 Issue
Check out more from this issue and find your next story to read.
Latest from Today's Medical Developments
- Copper nanoparticles could reduce infection risk of implanted medical device
- Renishaw's TEMPUS technology, RenAM 500 metal AM system
- #52 - Manufacturing Matters - Fall 2024 Aerospace Industry Outlook with Richard Aboulafia
- Tariffs threaten small business growth, increase costs across industries
- Feed your brain on your lunch break at our upcoming Lunch + Learn!
- Robotics action plan for Europe
- Maximize your First Article Inspection efficiency and accuracy
- UPM Additive rebrands to UPM Advanced