Patients suffering from chronic disease need to self-inject medication on a regular basis, often a painful, anxiety-ridden, time-consuming task. That is the task the 30-person development team at Cambridge, Massachusetts-based Portal Instruments is seeking to eliminate. Its needle-free device is one-sixth the diameter of a regular needle and syringe, injecting the exact dose of medication required with consistent, minimal sensation – administration is about the size of a strand of hair and goes through the skin in less than half a second.
Needle-free, self-administration of biological medicine is the focus of the clinical-stage medical device company founded in 2012. Founders of Portal Instruments include Ian Hunter, a professor of mechanical engineering at Massachusetts Institute of Technology (MIT); Patrick Anquetil, who has nearly 20 years of experience in nanotechnology with a Ph.D. in bio-instrumentation from MIT; Andrew Taberner, Ph.D. from the University of Auckland; and Cathy Hogan, Ph.D. from MIT.
Portal Instruments CEO Patrick Anquetil took time to explain more about the design and development of the Portal injection device.
Today’s Medical Developments (TMD): What need prompted the development of this injection system?
Patrick Anquetil (PA): There is an unmet need for patients suffering from chronic conditions that require regular injections to manage them. The most powerful drugs to address these conditions can only be administered with a needle and syringe, leading to tremendous patient anxiety in many, and in some cases, patients are not able to reach a successful outcome.
TMD: How long did it take to develop the injection system?
PA: The original platform was developed at Massachusetts Institute of Technology (MIT) throughout five years. Portal Instruments licensed the technology from MIT in 2014, and since then, our engineers have gone through seven generations of the device, including two clinical-grade devices. Our strategy as a company is to equip our engineers with state-of-the-art tools so they can design, build, test, and then iterate. On average, we have a new platform every six months.
TMD: What design features were considered during development?
PA: Key design considerations have been: ease of use, comfort, and giving a positive emotion about the overall therapy/treatment.
TMD: Describe the various components that go into the system.
PA: The internal components are a linear actuator, battery, and power management system – a logic controller based on an ARM [Advanced RISC (reduced instruction set pmputing) Machine] processor platform. The injection button is easy to press, and the housing is made from plastic. The cartridge is a pharma pre-filled, single-use, disposable that is easy to fill, fitting the standard format for filling on a typical aseptic fill/finish pharma line.

TMD: Are any parts manufactured in-house or are contact manufacturers used for components manufacturing?
PA: We only manufacture prototypes in-house as part of our rapid prototyping strategy. Our strategy is to partner with leading contract manufacturing organizations for all our components.
TMD: What processes and equipment are used for prototyping?
PA: In-house prototyping we use standard mills and lathe with glass scales; a CNC production-grade turning center; a 3D printer; and a laser cutter.
TMD: Is the piston in the system standard or specific to the device?
PA: The device includes a custom piston and there is a standard, off-the-shelf rubber stopper in the piston.
TMD: How is the piston controlled to administer the drugs to the patient?
PA: Control of the piston is through a computer-based, closed-loop feedback control with a feedback control loop running at 10kHz. The control loop makes sure that the device injects the right volume at the right time. It is a bit like cruise control where a car can maintain a pre-set velocity, irrespective of terrain. In the case of the Portal device, the controller makes sure the drug is administered in the same way, irrespective of the drug’s viscosity.
TMD: How is medication injected?
PA: We pressurize the drug to form a very fine jet that is one-third the diameter of a typical needle and syringe. The jet comes out at high speed (200m/s) and creates enough pressure on the skin to pierce it. Our control algorithm is such that we control the pierce phase to dial in injection tissue depth. Once we are at the right depth, the device slows down the jet and fills in the drug at that particular tissue depth.
TMD: How long does it take to deliver the injection through the skin?
PA: It takes 0.3 seconds to deliver 1mL – equivalent to doing 2 to 3 vaccines.
TMD: Are there specific body locations where this is designed to be used?
PA: At this time we’ve tested our device in the abdomen.
TMD: What is the difference between Portal Instruments’ injector and other needle-free systems in development?
PA: We have the only closed-loop feedback, needle-free, drug-delivery device. It is also one of the only few devices that can perform a 1mL needle-free injection. Legacy devices typically are only able to deliver 0.2mL to 0.5mL.

TMD: When do you hope the device will make it through the U.S. FDA approval process and on the market?
PA: We hope to launch a device in the market in the next two years.
Portal Instruments
www.portalinstruments.com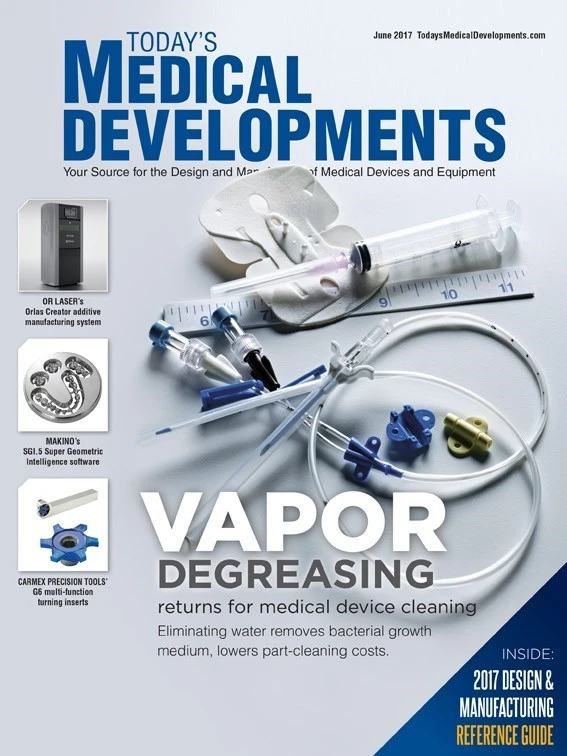
Explore the June 2017 Issue
Check out more from this issue and find your next story to read.
Latest from Today's Medical Developments
- The manufacturing resurgence is here – are you ready?
- Workholding solutions for your business
- ZOLLER events will showcase the company’s cutting-edge innovations
- THINBIT’s MINI GROOVE ‘N TURN Acme threading inserts
- CMMC Roll Out: When Do I Need to Comply? webinar
- Metabolic research uses Siemens gas analyzers to deliver results with 99.9999% resolutions
- Mazak’s SYNCREX 38/9 Swiss-type production turning machine
- Current economic and geopolitical realities demand decisive action