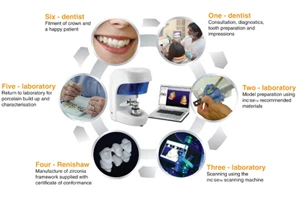
Renishaw plc may not come to mind when thinking of dental technology, but that is all about to change. This UK- based metrology company has developed a unique process for creating certified, all-ceramic copings and frameworks for crown and bridge restorations.
Established in 1973 by David McMurtry, now Sir David, and John Deer, Renishaw now stands at the forefront of automated metrology with accurate measurement products that also generate traceability. In 1987, Renishaw began investigating the metrology requirements of dental processes. After gaining experience from participation in multiple successful dental scanning systems and from further research and development, Renishaw developed, and recently launched, a unique, computer aided design and manufacturing process called incise.
For more than a century, most fillings were composed of silver and copper alloy, which were made into an amalgam with mercury. However, the use of mercury has caused concern for patients, resulting in a number of countries restricting the use of mercury-based fillings. While several other metals are associated with unpleasant allergic reactions and even toxicity, gold has withstood the test of time. Another key point of failure and of poorly-fitting crowns, causing reduced longevity and a host of adverse complications for patients is the cement gap between restoration and tooth.
Because of these concerns, there is a growing belief that metal-free dentistry will soon be in such demand that dentists will devote much of their time to removing metal restorations from the mouth and replacing them with biocompatible ceramics. The advent of the high-performance ceramic zirconia, which can only be used in conjunction with computerized technology, is transforming the practice of dentistry and the manufacturing of prosthetic appliances. Developed for use with this high-performance material and precision manufacturing processes, incise ensures an outcome of excellent fitting crowns that are cemented in place quickly, accurately and efficiently.
Knowing that it is essential to ensure the quality of the finished products, Renishaw's engineers define and control each step of the manufacturing process involved in the production of all-ceramic dental restorations. This is demonstrated in the 6-step process for all-ceramic crowns:

Preparation guidelines for creating space for the crown.

Impression of a patient's dentition.
1) Dentists will prepare a tooth for a crown by removing between 1mm and 3mm of enamel and dentine thickness, creating space for the crown. Renishaw assists dentists by providing preparation guidelines to avoid shortcomings. They also specify the type of tray to be used for the impression and the impression materials, ensuring that the impression is a precise record of the patient's dentition.

Replica of the patient's impression.
2) At the laboratory, a model is cast from the impression. Renishaw has tested and approved die stone materials which provide consistent and quantifiable results, creating an accurate replica of the impression.

Renishaw incise contact scanner.
3) Following trimming, the prepared tooth is scanned by a Renishaw incise contact scanner.
According to Renishaw, the contact scanner is the most accurate type available for this task, and its performance is traceable to a recognized international accuracy standard.
4) At the Renishaw milling center, the coping is machined from densely-sintered, medical grade YTZP zirconia, a key feature of this product. By perfecting a means of machining the zirconia billet in the sintered condition, problems associated with shrinkage are eliminated.

Table of typical material properties.
Other CAD/CAM systems normally machine the zerconia billet in a soft or pre-sintered condition and the process software therefore has to estimate the shrinkage that will occur during sintering.
This can be of the order of 20% and is non-uniform due to density variation, which represents a significant challenge and source of error.
Copings are analysed for accuracy of fit to the model and a certificate of fit analysis is produced. Margin error values are generated by computer aided analysis of the internal face of the coping aligned to and compared with the scanned preparation.
The certificate illustrates the cement gap on a 3D color coded image.

5) A porcelain veneer is applied by the technician to create the morphology and other characteristics required. It is important to use only those porcelains that are compatible with zirconia; Renishaw provides information to their labs on approved porcelains.
6) At the dentist, patients will receive the crown, and following try-in and acceptance, it will be cemented in place permanently.
Poorly designed or manufactured crowns can lead to gingival disease, loss of tooth vitality, secondary caries, bractures, de-bonding of cement and/or porcelain and unsightly restoration.

By specifying and controlling each part of the process, Renishaw's incise system has substantially reduced the possibility of errors, time consuming and expensive remakes and unnecessary risks to patients' dental health.
tmd
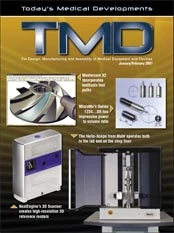
Explore the January February 2007 Issue
Check out more from this issue and find your next story to read.
Latest from Today's Medical Developments
- The role of robotics in precision medical device manufacturing
- Swiss Steel Group’s UGIMA-X machinable stainless-steel sets
- #51 - Manufacturing Matters - The Impact of M&A in MedTech 2024
- Visual Components: 25 years of simulation and programming software innovation
- Zimmer Biomet announces definitive agreement to Acquire Paragon 28
- Discover an innovative technology for EMI/ESD/TVS suppression
- Teleflex to acquire BIOTRONIK’s Vascular Intervention business
- Innovation at Global Industrie 2025