
Rauland, a subsidiary of AMETEK, is an American manufacturing company based in Mount Prospect, Illinois, producing workflow and life-safety solutions for hospitals and schools worldwide. They recently set internal mandates to increase manufacturing capacity by 30%, while initiating a more data-driven approach across their business. To do this, the Rauland factory team of 350 workers had to address day-to-day challenges such as labor and inventory shortages, increasing changeover times, and unknown scrap rates while working with 4,000 unique parts across four surface mount technology (SMT) lines. The Rauland team also wanted to improve their overall manufacturing productivity, efficiency, and controls.
To achieve their goals, Rauland looked to Panasonic Connect North America to provide the company with automated manufacturing technology to turn its factory – and its workforce – into a data-driven operation. With Panasonic PanaCIM manufacturing execution system (MES) software, Rauland achieved what it set out to do. Rauland worked with Panasonic Factory Solutions consulting service to walk through the technology they would need and set internal goals – from reducing scrap to preventing wrong parts being placed as well as including enhanced traceability of placed components onto the printed circuit – and answer challenges as Rauland introduced new technology to employees. The Factory Solutions team integrated Panasonic PanaCIM software into Rauland’s existing software products networked to solve key production challenges. The PanaCIM software applications work to meet Rauland’s objectives of reducing defects, scrap, and rework; eliminating wrong part placement; improving process throughout; and reducing change over time.
Once Rauland walked through its business goals with Panasonic and the software was in place, they began to see positive results immediately. At one time, Rauland was placing wrong parts into its line every week. Once the PanaCIM software was installed that number dropped nearly to zero.
With the data presented by the MES software, the Rauland team has also saved money by eliminating incorrect material counts due to virtually non-existent scrap rates as a direct result of installing the PanaCIM Material Verification and Material Control modules. These verify the correct components are loaded in the correct location, and track and update the estimated current quantity of material items with information obtained from production machines and handheld scanners. The team also created a common and fixed carriage plan and sequencing, which reduced changeover time on a particular SMT line by 63%.
Transforming operations
Founded in 1929, Rauland transformed its business from manufacturing throughout the Great Depression to, in 1979, establishing itself as a leader in nurse call communication, then, in 2017 being acquired by AMETEK Inc., a global manufacturer of electronic instruments and electromechanical devices with manufacturing, sales, and service locations across the United States and globally.
Working with companies such as Panasonic, Rauland digitally transformed its factory operations. Before Panasonic introduced Rauland to its PanaCIM solution, workers relied on fully manual processes. As workers once stood at machines writing performance data, critical pieces of information were frequently accounted for inaccurately or not at all. As the new PanaCIM software shares critical data automatically, Rauland has significantly reduced scrap by 33%, reduced the time it takes to count inventory from seven to two days, and eliminated downtime due to low inventory in the machines.
“We want to do more with less – just as everyone else wants to,” says Jimmy Crow, manager, manufacturing engineering at Rauland. “The data that PanaCIM provides allows us to monitor and control virtually the entire manufacturing environment in our SMT department. Data-driven is the key to our newfound success. We know exactly what’s going on at all times, and this real-time data provided by PanaCIM Production Analysis module helps us not only improve operations, but also impact the bottom line of our company. The decisions we make now are made on facts – not just a feeling, tribal knowledge, or anecdotal pass-down as it once was. Having a notification system like the PanaCIM Production Monitoring & Dispatch module, which uses real-time data to identify events that can impact production and to dispatch tasks and activities to the necessary labor resource, is critical to our continued progress.”Removing waste
Prior to implementing the PanaCIM modules and with manual processes in place, the team at Rauland would order 15% extra product in case there was more waste than anticipated. Within a short time of using the new technology, issues of over-ordering were nearly eliminated. Using warehouse data and material control services, Rauland now has consistency an d an ability to repeat best practices, which has eliminated the wasteful variability.
“Not only has the PanaCIM software changed our physical business processes, but it’s also helped change our company culture,” Crow says. “Today we can be so much more confident and proactive in what needs to get done and when. There’s a strong cohabitation between the automation technology and our workers, who have become much more technical than we ever imagined possible.”
Crow also highlights Rauland’s ability to “take ownership” of PanaCIM while allowing the solution to provide exception handling for out-of-control conditions based on machine data collection and analysis, citing it as the major contributor to their success.


Overall benefits
Between the increased accuracy and productivity offered by PanaCIM and Rauland’s reinvigorated workforce, the Rauland team was able to seamlessly integrate a newfound culture and confidence into everything they do and see, an additional benefit to its customers.
“Our relationship with Panasonic is extremely professional, courteous, and productive – that’s just the way they do business,” Crow says. “As shops get leaner and we continue to put out more product, embracing automation technology will be critical in helping the business case of our customers. It’s great getting to work with Panasonic to help us and our customers enhance bottom lines and user satisfaction.”
Panasonic Connect North America
na.panasonic.com/us/panasonic-connect
Rauland
www.rauland.com
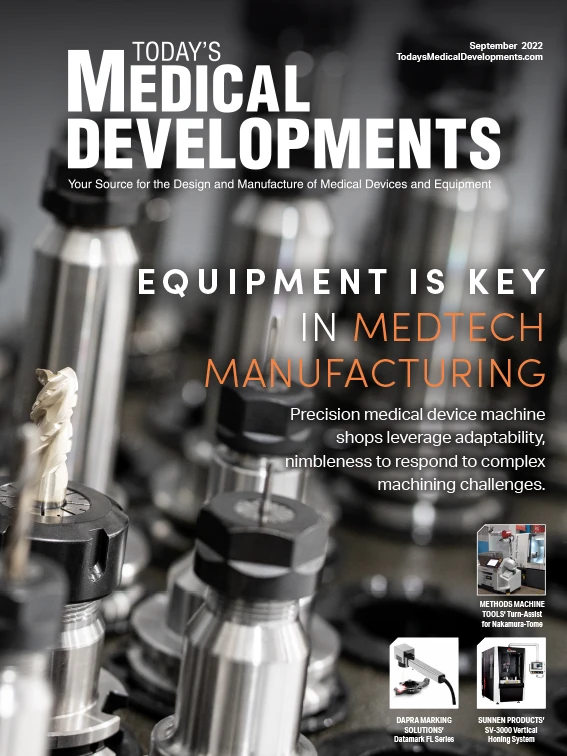
Explore the September 2022 Issue
Check out more from this issue and find your next story to read.
Latest from Today's Medical Developments
- Kistler offers service for piezoelectric force sensors and measuring chains
- Creaform’s Pro version of Scan-to-CAD Application Module
- Humanoid robots to become the next US-China battleground
- Air Turbine Technology’s Air Turbine Spindles 601 Series
- Copper nanoparticles could reduce infection risk of implanted medical device
- Renishaw's TEMPUS technology, RenAM 500 metal AM system
- #52 - Manufacturing Matters - Fall 2024 Aerospace Industry Outlook with Richard Aboulafia
- Tariffs threaten small business growth, increase costs across industries