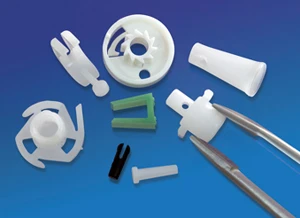
The miniaturization of components in a broad range of polymers gives medical designers greater flexibility in designing devices such as fluid delivery systems, diagnostic equipment and endoscopic devices for minimally invasive cardiovascular and orthopedic procedures. Meeting these demands and needs, Minnesota Rubber QMR Plastics provides custom molded components as small as one millimeter in diameter and weighing under .01g.
Minnesota Rubber molds these miniature components in a full range of advanced polymers, including: custom blends of PEEK, polycarbonate, polysulphone, Nylon, polyethylene and polypropylene. All are designed specifically to meet the needs of the medical device industry. The performance benefits of these polymers include: sterilizability, chemical compatibility, biocompatibility, durability and hydrolytic stability at elevated temperatures.
Get curated news on YOUR industry.
Enter your email to receive our newsletters.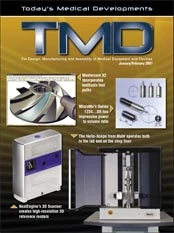
Explore the January February 2007 Issue
Check out more from this issue and find your next story to read.
Latest from Today's Medical Developments
- The manufacturing resurgence is here – are you ready?
- Workholding solutions for your business
- ZOLLER events will showcase the company’s cutting-edge innovations
- THINBIT’s MINI GROOVE ‘N TURN Acme threading inserts
- CMMC Roll Out: When Do I Need to Comply? webinar
- Metabolic research uses Siemens gas analyzers to deliver results with 99.9999% resolutions
- Mazak’s SYNCREX 38/9 Swiss-type production turning machine
- Current economic and geopolitical realities demand decisive action