
Linear motors offer a combination of high force, speed and accuracy that makes them ideal for applications such as grinding machines and large mold-making machines. Linear motors are also ideal in material handling applications where their quiet operation, reliability, economy and efficiency are highly desirable. Getting the most out of a linear motor often goes beyond basic motor sizing and selection skills. Here are a few hints on cooling linear motors to optimize their performance.
Linear motors, like other direct-drive motors, are built directly into the machine slide or machine mechanics to eliminate mechanical powertrain links. Because the motor is built directly into the machine and not hanging at the end of a slide, it requires proper cooling to avoid temperature influences on the machine's accuracy.
Therefore, the designer must choose the appropriate cooling method, depending on how the motor is used. In most cases, a closed-loop, liquid cooling system with a chiller unit is required. Providing liquid cooling to all motors on a machine optimizes machine performance and motor sizes.

A number of items must be properly selected to ensure proper coolant flow.
The chiller capacity must be properly selected for the number of installed motors, their locations on the machine, and their respective loads. These factors determine the energy that must be dissipated. With this data, you can determine the expected maximum temperature of the motors.
The overall height, tube diameter and length of the cooling system will influence the pressure drop of the coolant, so these variables must also be considered when sizing the coolant pump. Appropriate pressure regulators and manifolds must be used to assure proper coolant flow to each motor. Installing flow meters in the cooling return pipe from each motor, in order for the controller to monitor the flow, is recommended.
The chiller unit should have a maximum and a minimum temperature setting for the coolant. The nominal temperature should be set to the maximum ambient temperature of the motor, or use a temperature sensor to monitor the ambient temperature. In either case, the temperature of the coolant should not be cooler than 9°F below the ambient temperature, especially when the relative humidity is high, as condensation will form on, or even in, the motors. This could cause damage to the motors.
Water- or oil-based coolants can be used, as long as the coolant system is closed and the coolant is filtered and used solely for cooling of the motors, meaning do not use tap water, and especially not service water. Never use machine cutting coolant to cut corners.

IndraDyn from Bosch Rexroth.
Such attempts at saving money almost always cost more in the long run, as the chemical composition of the coolant will result in precipitates building up and blocking the coolant flow. This, in turn, will cause the motors to overheat. Improper coolant can also cause chemical reactions between the different materials that are in contact with the coolant. This could result in corrosion and eventual leakage.
To prevent such issues from happening, appropriate additives in the coolant should be used and a pH sensor should be installed to monitor the coolant itself. The machine controller can then inform the machine operator to properly maintain the motor coolant.
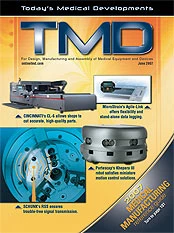
Explore the June 2007 Issue
Check out more from this issue and find your next story to read.
Latest from Today's Medical Developments
- Zimmer Biomet to acquire Paragon 28
- Industrie 4.0 award for Paul Horn GmbH
- CMMC requirements and your business
- Stryker exiting spinal implant business
- Perfecting the manufacture of microscopically thin films for tech, medical applications
- Find out what 2025 holds for design and manufacturing
- Montagu to merge Tyber Medical, Intech and Resolve Surgical Technologies
- Americhem’s EcoLube MD PFAS-free internally lubricated compounds