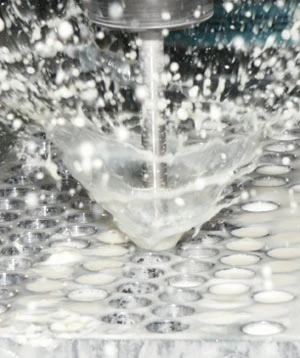
There are several factors to consider when a part requires an accurate hole. To determine whether a boring or a reaming process is more applicable, manufacturers must take a closer look at what they need as an end result. Understanding the differences, advantages and disadvantages of each process is vital to choosing which one would be most efficient.
Reaming vs. Boring
Boring, also called internal turning, is a process used to enlarge the inside diameter of a hole, increasing the size, straightness and concentricity of the hole. Reaming is another way of enlarging existing holes smoothly and accurately by removing small amounts of material. Single-point boring tools consist of a boring bar with an insert or solid carbide on the smaller diameters and a chip-breaker with the cutting edge ground into it. High-performance reamers consist of an insert with multiple flutes or "teeth" used to remove material. Throughout the years, the technology for both reaming and single-point boring has advanced – continuously improving to create closer tolerances and straighter holes with better surface finish.
Many materials used in medical applications today are high-temp alloys or hard, expensive metals like titanium. In addition, parts made for the medical industry, or any industry making highvalue parts, typically save the hole-finishing process for last, other than perhaps a deburring process. Therefore, reaming is generally a more efficient method because the tool is ground specifically for the customer application with their tolerances for the hole already figured into the design and size of the insert, according to Greg DeVore, product manager for Command Tooling Systems.
Less setup time and cycle time is also required with reaming, which is beneficial during the machining of an expensive part.
"It takes a little more experience to set fine boring heads, because the operator has to kind of creep up on the final size and not put too much adjustment in at one point to avoid excessive tool pressure," DeVore notes. "If they're in a hard material, they have to really be careful because it's going to take more tool pressure to cut the material, which can lead to deflection, especially on very small diameters. With reaming, you get less operator intervention to control the hole size, and as long as the tool is dialed in on run-out, the operator can take a new insert, put it in the shank, and run a good part. It is much easier to maintain quality throughout the process."
In situations where an operator runs into interruptions in the hole, it poses a challenge to maintain roundness and straightness, depending on the percentage of engagement through the interruption. When there is less than 60% engagement, the reamer will be deflected. Under these circumstances, single-point boring will usually be more accurate while going through the interruption.
Single-point boring and reaming can provide similar surface finishes, but slightly different surface textures. Single-point boring produces feed lines because the operator is feeding into the material with one cutting point. The result is fairly sharp peaks and valleys. While reaming also produces peaks and valleys, the peaks have a flatter surface and the valleys aren't quite as pronounced. Therefore, reamers tend to produce flatter surface textures.
On the other hand, single-point boring can be much more flexible than reaming. If a manufacturer is running short runs or lower-value parts in shortrunning lots, there will be a lot more flexibility with the single-point boring head than with a reamer, because the reamer is going to cut the size that it's ground to, whereas the boring head may be able to be used across several different operations that vary in diameters.
"It comes down to weighing the advantages and disadvantages of both kinds of operations," DeVore says. "If it is quality control, size control or surface finishes that are most important, reaming will often be the best choice. If it is flexibility that you need, and you have highly skilled operators, then singlepoint boring may be the better choice."
Chip Control
Command Tooling designs and manufactures custom and standard toolholders, as well as shrink-fit toolholders. Command also is the exclusive source for Urma modular boring systems for North America. At IMTS 2006, they introduced Urma's next generation Circo-Tec RX Reamers, available in a diameter range from 11.9mm to 100.6mm, and in various tool lengths.
During the time that the Circo-Tec reamers have been on the market, they have been used to complete parts made of a variety of materials: everything from Inconel to various irons, aluminum and all forms of steel, according to DeVore. The large library of geometries and flute configurations that Command Tooling can enter into a project assists in accomplishing effective results for the customer. For example, the left-hand helix flute reamer that Command offers pushes chips forward in a through-hole condition, keeping stringy materials out of the cutting interface during the reaming process.

Selecting the correct reamer for your precision machining requirements makes all the difference in the success of the application.
"In high-speed reaming, chip control just becomes paramount," DeVore says. "You have to have control of the material you're cutting; otherwise, you'll just be re-cutting it and destroying your tool. Getting the chips out of the cutting interface is probably the most important factor next to controlling the runout of the tool."
Harder materials, in general, are more forgiving in terms of reaming a hole. Although occasional mishaps can cause slight deviations in runout, the reamers will still produce an accurate hole. With soft materials, runout can cause the tool to want to dig in a little more, rather than center itself, making tight tolerances more difficult to hold. As far as the Circo-Tec reamers, surface finish, roundness, cylindricity and straightness have proven impeccable, according to DeVore.
Due to the geometry and the materials used in the reamers, especially for the carbide inserts, the Circo-Tec tool is very robust, allowing for accurate repeatable hole quality. Other advantages include the number of flute configurations, and the fact that quite often, the Circo-Tec reamers have more teeth in the cut than comparable reamers.
Another advantage that Circo-Tec reamers offer to the medical industry is shorter setup times. After the initial setup of the tools, the operator can go through a whole size change of reamer inserts on the same reamer shank.
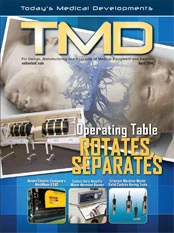
Explore the April 2008 Issue
Check out more from this issue and find your next story to read.
Latest from Today's Medical Developments
- Humanoid robots to become the next US-China battleground
- Air Turbine Technology’s Air Turbine Spindles 601 Series
- Copper nanoparticles could reduce infection risk of implanted medical device
- Renishaw's TEMPUS technology, RenAM 500 metal AM system
- #52 - Manufacturing Matters - Fall 2024 Aerospace Industry Outlook with Richard Aboulafia
- Tariffs threaten small business growth, increase costs across industries
- Feed your brain on your lunch break at our upcoming Lunch + Learn!
- Robotics action plan for Europe