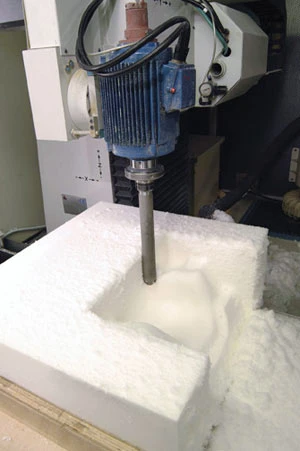
Through the use of advanced CNC machine technology, one manufacturer of prosthetic and orthotic devices is making substantial improvements to its production. Otto Bock, a leading supplier of these devices based in Germany, worked in cooperation with the CNC carving machine builder, Bornemann, to produce a series of machines, two of which currently produce prostheses and seat cushions in the Otto Bock facility in Plymouth, MN.
Because of the unique nature of this field, the majority of devices produced at this facility are custom, one-off productions. According to Otto Bock Vice-President Bill Clover, this creates operational challenges at every turn. "Otto Bock has operated in Minneapolis since 1958, acting as a sales and distribution location for the company's many product lines. In the case of the prosthetic and orthotic devices, we quickly realized the need to manufacture here, so we constantly evaluated the available technologies for machining. We were using ABT carvers, then we were using Thermwood routers for our foam products. Our biggest challenge is how to remain flexible in our manufacturing, given the constant flow of one-off work. We knew something was needed."
This led to the development of the Bornemann machine alliance and the development of carving technology, utilizing the latest CNC protocols. Since the product lines at Otto Bock run the gamut from orthotic support seating to various prosthetic shapes, cosmetic covers, and neck-to-pelvis body jackets, it was critical to have machines that will not only run efficiently, but also have the flexibility for fast changeover and interpolation of large data files.
The company uses its Bornemann carvers, each equipped with Siemens SINUMERIK 840D CNC technology, to cut proprietary rigid and flexible polyurethane foams into the seat cushions used to support spinal injuries, as well as the various upper and lower limb prosthetic devices and supports produced at this Otto Bock facility.
Otto Bock's facility in England provides the software used to capture the patient's particular characteristics, such as limb length, circumference, and degrees of soft tissue containment.
Once the prosthetist or orthotist collects the data, Otto Bock's fabrication software support engineering supervisor, Dennis Miller, enters the picture. "It's critical to have the data accurately interpolated into the tool path for cutting these blocks of foam and rigid materials. You might draw some analogy to the aerospace industry and the contours of a wing. The human body has no straight lines, so the movements of the cutting tool are extremely complex machine programs," Miller explains.
Clover details the previous carving method for the seating systems produced at Otto Bock, contrasting that method with the Bornemann robotic 5-axis milling machines now used. "Previously, a plaster cast would be made, then that mold would be used to reverse engineer the cutting path on the router. It was very slow and very imprecise. Today, we've developed the OBSS, Otto Bock Seating System."
As Clover explains, the patient is seated in something similar to a bean bag chair; the bag is then evacuated and the bag surface is digitized, using Otto Bock proprietary software, developed in cooperation with Polhemus, originators of the FasTrack 3D contact scanning system. This version of a CAD program is then translated through ProfiCAM into the Windows-based, CNC machining program.
Clover further describes the work done by Otto Bock in conjunction with Polhemus, a manufacturer of various devices used for digitizing. Polhemus, located in Colchester, VT, provides 3D position tracking systems. Polhemus supplies a complete range of these high-quality 3D motion tracking and digitizing systems for various industries including medical, military training and simulation, computeraided design, and virtual reality.

The Siemens SINUMERIK 840D, the CNC running the Bornemann machine, is also equipped with a Siemens SIMODRIVE 611U drive package for precision motion control.
Clover explains that through the use of this advanced, clean, and non-invasive laser scanning technology, an extremely accurate image can be made of the patient's torso from the seat bag surface used to initiate the design process. The software is then manipulated from CAD to Proficam and finally to the CNC on the machine, through the proprietary Otto Bock Shape System (OBSS.)
Miller notes, "compared to the old toolpath generation method, the same path that took two to three hours now takes perhaps 10 minutes. A wheelchair cushion that used to take 90 minutes on the old system, takes less than 20 minutes to produce."
In terms of overall productivity, both Miller and Clover tell how a typical month's seat cushion output was once about 20, but now averages about 250. Clover further states, "We could never have achieved these levels without the Bornemann machines and Siemens CNC technology."
In a typical manufacturing operation for a seat cushion, a 26" x 26" x 14" H-block of material is secured in the vacuum bed on the Bornemann machine. A probe determines the zero offsets on the blank. For a prosthetic device, a rotary axis, two-ribbed, cone-shaped arbor is mounted on the machine. A predetermined coordinate fixture is used to verify the offsets and rotation angles. For foam cutting, a 12" long hollow tube of tool steel and 40mm ball end rasp are used. On the rigid polyurethane blanks, the same design of cutting tool, only 7" in length with a ball endmill, is utilized.
Once made, a prosthetic device is checked, using a specific diameter check ring, as well as digital calipers, to verify the contour surfaces as accurately as possible.
The machine operators at Otto Bock generally do not require extensive Gcode programming skill as the program is directly downloaded to the NCU on board the Siemens CNC. Since the part programs are usually quite large, they run directly from the NCU on the machine.
Miller also notes the service contract on the machines have worked well for his staff, with phone support quickly provided to troubleshoot both Bornemann's and the CNCs. "This support is especially critical," Clover notes, "as there are currently only seven such machines in operation worldwide."
Siemens Energy & Automation
Elk Grove Village, IL
SiemensCNC.com
Otto Bock Healthcare
Duderstadt, Germany
ottobock.com
Bornemann-Werkzeugtechnik GmbH
Delligsen, Germany
bornemann-werkzeugtechnik.de

Explore the January February 2008 Issue
Check out more from this issue and find your next story to read.
Latest from Today's Medical Developments
- April Manufacturing Lunch + Learn with Iscar
- April Manufacturing Lunch + Learn with Insaco
- Laser cold marking for plastic medical device manufacturing
- Paperless Parts’ BOM Builder
- #58 - Manufacturing Matters - 2024 Metrology's Latest Advancements with Starrett
- Strategies to improve milling and turning for medical components
- Being proactive about your business despite uncertainty
- 10 challenges facing the manufacturing industry in 2025