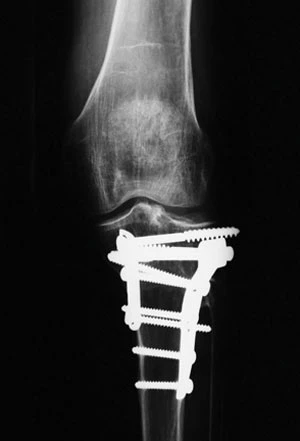
Although productivity is key to any profitable plant floor operation, it can never be a trade-off for delivering a quality product. Nowhere is this more evident than in the medical field. Surface finishes are critical. Sharp edges or shards on a workpiece or failure of a bone screw to lock into a secure position can result in potential agony for the patient and years of litigation for the hospital and manufacturers involved.
On the other hand, commodities such as bone screws must be produced at affordable prices and high productivity.
Bone screws - typically made of 316 stainless steel - are produced by the millions in the United States to strict demands for tolerance, surface finish, cleanliness and packaging. Typical bone screws range in length from 6mm to 80mm and have outer diameters from 2mm to 8.5mm.
Surface finish requirements tend to fall in a 0.4µm to 0.8µm range with dimensional tolerance of ±0.025mm.
Not so many years ago, typical bone screw manufacturing consisted of three separate processes. First a lathe would cut blanks from bar stock. Then, another lathe would create the threads. And third, a machine would handle the other screw features such as cutting the socket head in the cap screw. Traditionally, the screw head featured a hex-shape, comprised of sharp corners that required a broaching operation. With broaching, the material actually gets compressed out of the way, which, to an extent, influences the integrity of the material and creates a potential for small burrs on the exit side of the cut.
The next process to come into use was when a new hexalobular screw hit the market. This star-shape locking system with rounded radii in the corners and on the edges allows high torque to be transmitted without damage to the screw head. This design enabled screw manufacturers to achieve better productivity using machining, which is a faster process than the traditional broaching.
However, the process is patented and requires royalty fees that not every screw manufacturer is willing to pay.
Today, there are still multiple operations to create a bone screw, but they are typically performed on multi - spindle Swiss turn machines that have both turning and milling capability with threading of the screw body first and milling of the head second. Now the lathe is automatically fed stock to create a blank and the threads are then created. To achieve the hexalobular screw head, there is a pre-drilling of the center circle to lessen the load on the endmill, where milling becomes the final operation.
This milling process is faster than broaching and produces better quality parts and longer tool life, but it does add a fourth process - the predrilling of the hexalobular shape - to the operations. This is a process that Seco Tools application specialists have found to be unnecessary.
REAL-WORLD RESULTS
In a recent customer application, creation of the threads on the stainless 316L stock was taking 3 minutes, whereas the milling/drilling cycle was taking over twice that time; anywhere from 6.5 minutes to 7 minutes. This defeated the purpose of the multitasking capability. Initially, Seco came in and ran a drop-in test where they simply substituted their Jabro solid carbide endmills with a competitive product. The exact same data was run, yet the customer was able to produce more than 1,000 parts with a single set of endmills versus the competitor's total of 70 pieces.
Working more closely with the customer, Seco discovered that synchronicity of the machine was the company's crucial issue, since this is the advantage of the multi-spindle capability. So, Seco decided to remove the second drilling operation, which was taking over a minute in cycle time.
Instead they went right from threading to milling using the Jabro mini-endmills to achieve diameters as small as 1/12". Additionally, they increased the feedrate to three times the previous drilling rate, and to eight times faster on the finishing cycle. This resulted in the milling being achieved in only 2.5 minutes to 3 minutes, now making it faster than the threading operation.
By taking advantage of a 60,000rpm sub-spindle, the customer was able to feed a 0.020" diameter endmill at an alarming 29ipm. The company was still able to get about 300 parts per edge, achieving four times the tool life and 50% cycle time reduction as compared to the four-step methodology.
Seco Tools
Troy, MI
secotools.com

Explore the August 2009 Issue
Check out more from this issue and find your next story to read.
Latest from Today's Medical Developments
- German robotics and automation in a downturn
- Blueshift’s AeroZero
- November USMTO grow from October
- Platinum Tooling’s custom and special tooling
- Top 5 global robotics trends 2025
- Accumold’s micro molding innovations
- Methods Machine Tools, Multiaxis, announce AI solution investment
- MGS to showcase global expansion and healthcare CDMO expertise