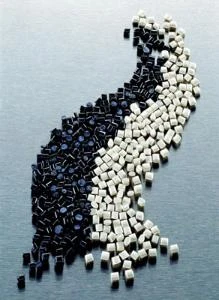
New advanced biomaterials, specifically developed for in vivo implants, are increasingly being leveraged by device manufacturers to develop high quality implantable devices. At the forefront of these advances in medical engineering are two poly- etheretherketone poly- mers, PEEK-OPTIMA and PEEK- CLASSIX, manufactured by UK based Invibio Inc.
Medical device manufacturers are realizing these bio- materials not only offer ways of developing better medical devices, but also help reduce the time and expense associated with regulatory approvals. Their increase in use is attributed to a unique combina- tion of strength, stiffness and toughness, together with bio- compati- bility and the ability to be repeatedly sterilized with out the degra- dation of their mechanical properties.
Highly Reliable Biomaterials PEEK-OPTIMA polymer is used in the development of pharmaceutical applica- tions and implantable medical devices having blood or tissue contact for more than 30 days. Since its introduction to the med- ical market, this material has gained the confidence and acceptance of the medical community as a highly reliable implantable biomaterial. The material has been used in the development of hip stems, spinal fusion cages, suture anchors for arthroscopy, dental bridges, abutments and healing caps, intracardiac pumps and heart valves. PEEK-CLASSIX polymer is a US Pharmacopoeia Class VI thermoplastic and in contrast to PEEK- OPTIMA it is designed for medical device applications requiring blood or tissue contact of less than 30 days, including catheters, surgical instruments, analytical equipment, blood management and drug delivery systems. This material is one of the most chemically resistant polymers available and exhibits a superior combination of strength, stiffness and toughness making it ideally suited for limited contact medical device applications.
A Material for Better Implants Exceptional biomaterials make high quality medical devices. PEEK-OPTIMA polymer can be formulated using a variety of additives, such as barium compounds for controlled radiopacity, or reinforcing carbon fibers for increased strength and stiffness. This offers versatility and adaptability unavailable to traditional metallic materials. These advantages are key in the increased use of PEEK-OPTIMA in load bearing implant applications.
As an example, matching the material's stiffness to that of bone is important for orthopaedic implants. Bone requires stimulus from mechanical stress to maintain its structure. Metal implants, with a substantially higher modulus than cortical bone, can cause a phenomenon known as "stress shielding", which is commonly believed to lead to bone mass loss, implant loosening and subsequent failure.
In part it is this ability to tailor the mechanical properties of the material that led spinal device manufacturers to use the polymer in the development of pioneering cervical and lumbar fusion cages. Other advantages include the material's compatibility with modern imaging technologies, such as MRI and CT.
PEEK-CLASSIX polymer can be repeatedly sterilized using conventional sterilization methods including steam, gamma radiation and ethylene oxide processes without the degradation of its mechanical properties. It is characterized by extreme hydrolytic resistance, even at elevated temperatures.
For this reason the material has been used in the development of laparoscopes, endoscopes and other surgical instruments which require repeated sterilization.
Reducing Expenses and Time to Market
For manufacturers of medical devices, time to market is a critical factor. Invibio's PEEK-OPTIMA polymer has been tested to industry standards and Device (MAF) and Drug (DMF) Master Files containing these results, as well as additional testing and extensive data concerning the polymer and its manufacturing methods, are lodged with the FDA. Making this information available to device manufacturers can help reduce the time and costs involved for device clearance with regulatory agencies.
Several medical device manufacturers have leveraged this information to dramatically reduce their application's time to market by more than year and have realized significant cost savings as a result.

Explore the May 2005 Issue
Check out more from this issue and find your next story to read.
Latest from Today's Medical Developments
- Tariffs threaten small business growth, increase costs across industries
- Feed your brain on your lunch break at our upcoming Lunch + Learn!
- Robotics action plan for Europe
- Maximize your First Article Inspection efficiency and accuracy
- UPM Additive rebrands to UPM Advanced
- Master Bond’s LED415DC90Med dual-curable adhesive
- Minalex celebrates 60 years of excellence in miniature aluminum extrusions
- Tormach’s Chip Conveyor Kit for the 1500MX CNC Mill