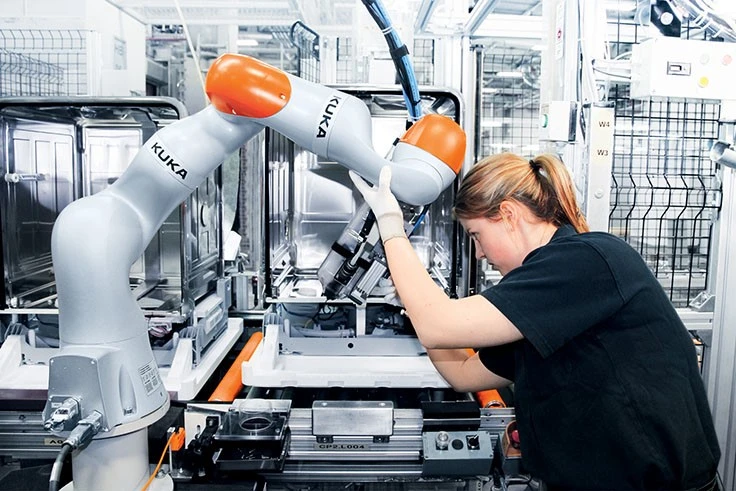
3D printing is used to develop state-of-the-art prototypes, but the potential for far greater impact is just being unlocked as manufacturers discover opportunities to move the technology from research and development (R&D) to the factory floor.
According to a recent report, the 3D printing industry grew more than 20% last year – surpassing $7 billion total value. No other industry has had a bigger hand in the expansion of 3D printing than medical.
From introducing much-needed customization to cutting costs, 3D printing has the opportunity to bring several benefits to medical professionals and patients across the world.
Making things personal
Prior to the emergence of 3D printing, consumers received implants – knees, hips – that adhered to set standards. While such devices help patients lead better lives, there’s room for improvement since one size simply doesn’t fit all. To better meet patients’ needs, doctors and physicians are trading in mass-produced implants for those designed and manufactured with specific measurements in mind; this is where customization makes all the difference.
A study from Arthroplast Today found patients with customized knee implants experience fewer problems than those who have standard implants:
- 5% of customized implant patients need to visit a rehabilitation center
- 15% of standard implant patients need rehabilitation
As 3D printing technology continues to improve, patients will gain greater post-surgery success as surgeons will choose a 3D-printed implant that’s an exact match, removing much of the discomfort accompanying implants while delivering greater freedom of movement.
Bringing down costs
Nearly all manufacturing professionals expect to see an increase in medical applications for 3D printing. In addition to patient customization, 3D printing has the potential to minimize costs. The manufacturing costs for creating customized and standard knee replacements are nearly the same, but patients with customized knee implants save an average of $913 in medical bills.
For patients from war-torn countries, lower costs can be lifesaving. Each year, 26,000 people fall victim to landmines that are often left behind long after a conflict has subsided. Plenty of time and money is dedicated toward providing relief to those physically impacted, and among the most effective solutions is 3D printing.
By paving the way for low-cost prosthetics, 3D printing has helped disabled patients regain mobility.
Whether it’s a limb or brace, there’s no limit to how 3D printing can aid those in need. And, as 3D printing technology progresses, customized prosthetics will be produced at a fraction of the cost of standard medical devices.
Picking up the pace
With 3D printing, medical professionals may have the opportunity to take action sooner rather than later, especially in emergencies when there is no more than a few minutes to assess the situation.
Last fall, engineers at MIT created a desktop 3D printer that’s 10x faster than existing printers. This uptick in speed – hours not days for an implant – promises to go a long way toward saving lives. Too often patients lose time traveling to care sites better equipped to handle a specific emergency, especially in remote areas. 3D printing can help deliver advanced capabilities to more hospitals and medical centers.
Anatomical models that are produced through 3D printing can also enhance surgeon education and preparation. Doctors can use the models to closely study fracture patterns or generate new surgical strategies. The added insight paves the way for better care, shortening operation times, reducing patient trauma, and treating more patients.
As 3D printing technology continues to push the boundaries of what modern medicine can accomplish, manufacturers have just scratched the surface of what’s possible. Medical device and equipment manufacturers need to take advantage of the benefits 3D printing brings to the table. Manufacturers that embrace 3D printing technology stand to deliver the customization, cost savings, and speed today’s medical professionals require.
Kuka Robotics
www.kuka.com
IMTS 2018 Booth #236200

Explore the August 2018 Issue
Check out more from this issue and find your next story to read.
Latest from Today's Medical Developments
- Tariffs threaten small business growth, increase costs across industries
- Feed your brain on your lunch break at our upcoming Lunch + Learn!
- Robotics action plan for Europe
- Maximize your First Article Inspection efficiency and accuracy
- UPM Additive rebrands to UPM Advanced
- Master Bond’s LED415DC90Med dual-curable adhesive
- Minalex celebrates 60 years of excellence in miniature aluminum extrusions
- Tormach’s Chip Conveyor Kit for the 1500MX CNC Mill