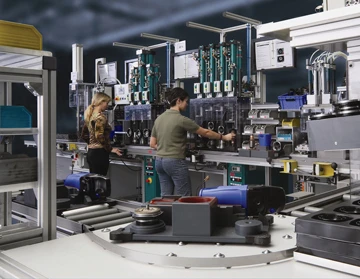
The global trend towards "lean production" continues to gain strength. This manufacturing concept provides an optimum framework for efficient, competitive production and is based on a philosophy of consistent waste avoidance.
The basic components of lean production fall into the following categories:
- Inventory reduction
- Elimination of downtime
- Reduction of floor space requirements
- Error avoidance
- Elimination of inefficient processes
- Avoiding overproduction
- Shortening transport route
Granted, the lean approach is not the solution for all manufacturing problems. But it does offer a uniquely flexible solution for assembling more complex products. Here are nine basic lean manufacturing principles that should help you evaluate lean manufacturing solutions for your own applications.
Continuous Flow
The preferred shape of the lean workcell is U-shaped. Each subprocess is connected to the next in order of process. With the worker in the interior of the U, minimum movement is required to move the workpiece or assembly from one workstation to the next.
Ultimately, one of the goals of the lean workcell is to eliminate all nonvalue- added movement; hence its Ushape. When the operator finishes the process, he/she simply turns around and is back at step one. The workpiece may be moved from one value-added operation to the next. Although very heavy parts may be transported on belt conveyors, manual push or gravity conveyors are ideal for moving parts between workstations. They are not complex and are easy to connect end-to-end, which makes it easy to move workstations within a workcell.
The curved "corners" of the Ushaped workcell can pose a problem -- use of a ball roller transfer should facilitate part movement through the corners of the U-shape.
Lean Machines/Simplicity
Since continuous-flow, one-at-atime manufacturing is another goal of lean manufacturing, it is important that each workstation or machine be designed to fit within a minimal envelope to ensure elimination of excess flat space at the workstation or machine. This is done to avoid the possibility of storing parts or subassemblies at the machine. Storing parts increases work in process and results in "batch" processing, which subsequently defeats the purpose of lean manufacturing. In addition, smaller, minimal size workstations and machines eliminate unnecessary steps taken by the worker between subprocesses.
Finally, significant floor space may be saved by properly sizing workstations and machines. Each machine base or workstation should be designed to optimize assembly subprocesses, which in most cases will vary from workstation to workstation. This customization can be achieved with virtually any structural material although preference should be given to material that is reconfigurable and reusable, such as extruded aluminum, bolt-together systems.
Moreover, in a continuous improvement environment, all workstations and workcells must be easy to modify as process improvements are identified. In addition to their superior flexibility in layout and design, lightweight aluminum structures are easier to move when reconfiguration is necessary. Casters may be quickly mounted to the Tslotted profiles to allow movement without the use of fork trucks or other lifting equipment.
Workplace Organization
A smooth, uninterrupted flow of completed workpieces is the desired result of a properly designed lean workcell. Nothing can slow or stop this flow faster than the loss or misplacement of tools. Thus, all tools used at a workstation should have their own holder. There should be exactly as many holders as there are tools so that the absence of a tool is quickly noticed.
To minimize downtime, backup tools should also be available at any automated workstations. These tools should be out of the worker's way until a failure occurs at the automated workstation.
The ready availability of workcritical information also adds to efficiency in a workcell. Supplying the right information at the workplace, such as assembly processes, work instructions, repair procedures, or even production targets, allows workers to make the right decisions and act on them on the spot, limiting downtime often spent chasing down a busy supervisor.
Parts Presentation
Naturally, during the average work shift, additional parts will be required for the workcell. Traditional methods of re-supplying workstations are not useful in a lean workcell. Workers should go about their work with the minimum number of interruptions. Therefore, all parts should be supplied to each workstation from outside the workcell. The use of gravity feed conveyors or bins fits the simplified design of the lean workcell.
Parts bins should load from behind (outside the working area of the workcell) so that workers may continue production without interruption. Gravity carries the parts to the worker's reach area. Bins should also be reconfigurable.
Although bins are ideal for small parts, many assemblies require larger parts. These may be delivered in bins or boxes. Again, parts should be delivered to the workcell without entering the work space. Gravity feed conveyors serve this purpose well. In the event that scrap or containers must be removed from the cell, an additional gravity feed conveyor may be mounted in the reverse direction. In instances where parts are very heavy, lift assist devices are recommended.
Reconfigurability
A properly designed lean workcell must be easy to reconfigure. In fact, the ability to change the process and go from good part to good part as quickly as possible is a must. The faster the changeover, the less production time is lost.
Quick-change fixtures are one way this can be accomplished. With a good quick-change fixture, changeover can be accomplished in a matter of seconds. A number of different fixtures may be stored at the workstation and swapped as the situation requires.
At times, due to process changes or other factors, a lean cell must be quickly reconfigured or even moved to accommodate assembly of a new product. In the event that a machine or workstation must be changed, the ability to move each component of the workcell quickly becomes extremely important. Lockable casters on machines or workstations provide the mobility necessary for rapid and efficient changeover.
QualityOne result of one-at-a-time manufacturing is a decrease in quality problems. As each part is produced, visual inspection by workers can verify that it is correctly assembled. If verification is required through gages, they should be mounted to the machine or workstation and be easily replaced. Quick release of fixtures using star knobs or locking levers is a necessity.
There may be time when a quality problem cannot be easily fixed. A flawed process or malfunctioning machine may be the source of the quality problems.
In the case of a flawed process, the structural framing system allows changes, no matter how great, in a minimum amount of time. Once again, bolt-together construction solves a major problem in minimum time.
A malfunctioning machine may also be easily replaced, particularly if quick disconnects for all pneumatic or electric lines are provided when the lean cell is designed. In addition, no pneumatic or electrical connections should be present between machines in the lean cell. These would slow the changing of the machines within the cell.
Once the machine has been disconnected from all power sources, it can be easily transported if mounted on lockable casters.
Ease of reconfiguration and changeover eliminate any reluctance on the part of workers or management to try to "make do" with machines or processes that are "almost" right. This change in attitude can contribute greatly to true quality production.
Maintainability
Ease of service is another requirement of a lean cell. Long down times cannot be tolerated in a pull-through system. When customer demand exists, the product must be produced. A modular structural framing system provides the ultimate in maintainability.
Components can be replaced or reconfigured in a matter of minutes. Bolt-together construction ensures machine stands, guards, workstations or parts presentation equipment can be serviced in a matter of minutes. Even entire machine bases can be rebuilt in a minimum amount of time.
The structural framing system also provides a source for common components for all machine bases, guards and workstations. With standardized components, a minimum number of tools are required to maintain a structure. With a structural framing system, three or four simple hand tools are sufficient to build or repair any structure. Another benefit is that common components eliminate the need for a large inventory of spare parts. It is possible to standardize on one size of aluminum profile, one or two connectors, and a few accessories to create virtually any structure.
Finally, no finish work is required with an aluminum structure. No welding or painting is required. Repairs can be accomplished in the minimum amount of time.
Ease of Access
Using an aluminum framing system as the foundation of a lean cell, all necessary work components can be mounted in easily accessible locations because each surface is a potential mounting surface. Parts bins, tools, shelves and fixtures can all be positioned in the optimum location for efficient work. The T-slot on the framing system's surface also allows quick repositioning of pneumatic or hydraulic components if clearance space is critical.
Components may be added quickly to any workstation and easily repositioned to insure accessibility for each worker. In addition, entire guards or individual panels can be removed quickly with simple hand tools, enabling service technicians to perform maintenance in a matter of minutes.
Ergonomics
Finally, workers must be protected from ergonomic problems. Any properly designed lean workcell must, by definition, be ergonomically designed. Maintaining the work at the ergonomically correct height throughout the workcell is always important. Although it is frequently not taken into consideration, designing for the average worker height is also a necessity. Since average heights vary from country to country, the height of a machine or workstation must be easily changed if there is any chance that a workstation may be shipped from country to country.
Lift assist devices must be considered where the weight of parts or boxes of parts exceeds lifting standards. In this case, pneumatic, hydraulic, or electric devices may be used, but it is important to keep in mind that simpler is better in lean manufacturing cells. In order to prevent delays in manufacturing caused by faulty design, a software package that allows testing of the ergonomics of a workcell before it is constructed can be a powerful tool. Use of such a software package lets you settle ergonomic issues in the design stage rather than on the factory floor, providing significant potential savings in both time and money.
Final Considerations: Hybrid Systems
With all of its promise, the lean cell may not be the answer to all assembly needs. At times the U-shaped configuration simply does not fit the existing facility or process, and a change from automation or semi-automation to lean cell manufacturing could be counterproductive.
In keeping with the flexibility requirement for lean manufacturing, there may be times when a hybrid system rather than a pure lean system is best for the manufacturing process.
Hybrid manufacturing systems combine the economies of the lean system with the safety and efficiency of an automated system. The result is a system in which some assembly is done manually while more dangerous or ergonomically difficult tasks are accomplished by machine.
In a hybrid system, workstations or cells may be combined with nonsynchronous assembly conveyor systems to achieve desired production goals. The synergy between these two technologies can produce results far beyond the capabilities of either technology alone. It is also possible to accomplish assembly in a lean cell and to have operations that are purely automated take place off line. In this case, the automated portions of the process supply subassemblies or parts to the lean cell. Here, although the technologies are separated, both are still required to accomplish the task at hand.
The key to hybrid implementation is construction with components which are easily reconfigured. Bolt together technology fits the description perfectly. Flexible assembly systems using aluminum framing as the main structural element allow companies to mix and match manual and automatic operations at will, and to change them at any time in the future. The result is a workerfriendly, economically-sound system designed for optimum production.
Today, lean production is generally associated with manual production systems. Such systems are currently in trend and are successfully integrated into numerous assembly processes and in various sectors of industry. Lean production does not, however, eliminate automated transport. Transferring parts manually can cause a drop in quality or a loss of valuable time resulting in an increase in per piece costs.
Finding the most economically efficient transport solution depends on the following production factors:
- Batch size and variety of models
- Production life cycle
- Part weight and size
- Cycle time
When does automation make sense?
Automated production or the automated transfer of parts is always the best choice if one can cut costs and increase process reliability when compared to a manual solution. In other words, the savings gained through automation must offset the higher investment costs. In many situations, the best solution is a combination of manual workstations linked by automatic systems. Finally, certain production processes are simply economically unautomatable - for example when quantities are too small or the product mix changes too frequently.
Efficient transport ensures economical production
Each production process involves materials or workpieces which are transported from point A to point B. However, as no value is added to the product during transport, investments in this part of the process chain are usually ruled out from the offset. This is a serious mistake: the manual forwarding of parts from one station to the next as well as the coordination of individual production processes represents a critical factor in terms of time and cost. Therefore, the efficiency of a transfer system is also a key factor in assessing the economic viability of a production system.
Cost comparison of individual systems
It is possible to create an example to serve to compare the costs per transfer cycle of a manual material transfer system, a "pick & place" solution and an automated transfer system. For both of the automated solutions, the comparison assumes a straight-line depreciation over a period of five years and 3500 operating hours per year (two-shift operation).
When all relevant factors are considered for a system with a 10 kg part weight, the manual solution performs well for cycle times > 35 sec. However, this applies only to lowwage countries. Automated transfer systems clearly represent the most cost-effective solution when shorter cycle times are required.
Other advantages of transfer systems
Avoiding overproduction
- Transfer systems can be used to regulate production cycles, thereby supporting the flow principle and ensuring continuous production based on the volume of customer demand.
Accelerating production
- Reduces transfer and handling time in comparison to manual transport.
Higher, more consistent product quality
- Gentler handling of product surfaces and exact precision when processing parts, due to the stable position of the workpiece on the pallet.
Flexible application
- Extremely small, very large, and even sensitive parts can be transported safely.
- Can be integrated into existing - even manual - production lines without difficulty.
- Easy to expand or adapt to changing production requirements
No "out-of-the-box" solution
For the reasons mentioned above, there is no easy answer as to which is the most efficient transport solution for lean production. A rash decision against automation without an honest evaluation of its potential benefits risks causing waste - and this is exactly what lean production seeks to avoid.
Individual factors throughout the production process must be considered carefully before a decision is made - whether in favor of the manual transport of parts or automatic forwarding via transfer or handling systems. At Rexroth, customers profit from the knowledge that goes far beyond single-system solutions, and from a range of products which covers all aspects of lean production. Whether manual production or automatic transport systems -- the solution is available. TMD
Karl Wojcikiewicz is the Product Manager for Structural Framing & Workstations at Bosch Rexroth Linear Motion and Assembly Technologies.
Rexroth supplies manufacturers worldwide with a broad range of ergonomic components ideally suited for lean manufacturing: easily customized workstations, tool holders, information boards, parts bins and a broad range of workstation accessories. Combined with the Rexroth Aluminum Structural Framing System, these components let manufacturers build exactly the work environment required to match the parts, workers and workcells to their manufacturing processes.
Bosch Rexroth Corporation is also a leading supplier of power and free non-synchronous assembly conveyors. With its family of products, hybrid lean manufacturing systems are available from a single source, with completely interchangeable structural components. Visit www.boschrexroth.com.

Explore the June 2006 Issue
Check out more from this issue and find your next story to read.
Latest from Today's Medical Developments
- Birk Manufacturing achieves ISO 13485 recertification
- AdvaMed’s Medical Innovation Agenda for the 119th Congress
- SW North America's BA 322i twin-spindle CNC
- The role of robotics in precision medical device manufacturing
- Swiss Steel Group’s UGIMA-X machinable stainless-steel sets
- #51 - Manufacturing Matters - The Impact of M&A in MedTech 2024
- Visual Components: 25 years of simulation and programming software innovation
- Zimmer Biomet announces definitive agreement to Acquire Paragon 28