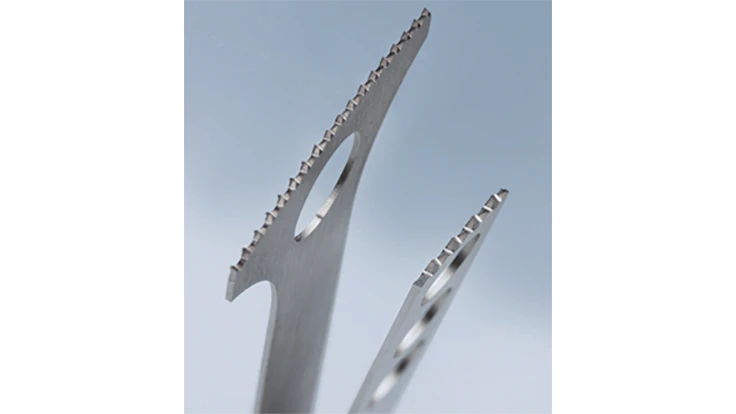
Rollomatic

1. What kind of surgical drills are on the market?
A substantial portion of medical cutting tools are bone drills with conical, split, 3-flute, or trocar drill points. Available drill bodies include solid stainless steel, tubular drills for removing drill debris, and cannulated bodies with trocar points.
Surgical drill point angles are lower in comparison with industrial drilling tools, ranging from about 90° to 55°.
2. What other medical cutting tools are used?
Bone saws usually use reciprocating or oscillating action. Perforators for cranial surgeries drill into the skull to form an opening to route a skull plate.
Orthopedic burrs made from stainless, tool steel, and carbide are used for joint repairs and surgeries. Shank types include tubular, solid, welded, or a two-piece construction.
Rotary shaver blades, run on powered handpieces, remove tissue and debris and perform bone resection. An outer stationary tube with a small window toward the front of the tool, and an inner rotating tube with a smaller window in the identical position, have the shape of cutting teeth. When moved against each other, they perform a grabbing action, moving debris up the tube with suction.
Bone taps prepare the thread in the bone for inserting an implant and an implantable screw. Spherical cutters and hip rasps prepare the hip socket and femur for hip-joint replacements.
3. How are surgical cutting tool quick-disconnect features machined?
The basic shape of the tool is often machined on Swiss-type lathes, including the driving notch – which is the quick- disconnect and driver feature at the end of the shank. The latest designs demand higher accuracy than machining can provide, so feature grinding is necessary. Peel grinding machines can simultaneously grind the cylindrical part and the features, adding flats, hexagon with corner radius, plunges, gashes, and recesses.

4. What types of super-abrasive wheels can be used for grinding stainless?
Electro-plated CBN wheels use a mono-layer of abrasives attached to a hardened steel wheel for more porosity and less heat generation than bonded wheels. The wheel can be manufactured in any profile, allowing profile grinding.
Common diamond wheels don’t suit steel grinding. As the Swiss diamond wheel manufacturer Diametal SA puts it, “Steel has a high affinity to carbon. Since diamond consists of pure carbon…the high temperatures produced in the grinding process cause the steel to extract carbon atoms from the diamond, eroding the diamond-grinding grit.”
5. Why is 6-axis tool grinding best for grinding surgical cutting tools?
A grinding machine with 3 linear and 3 rotary fully interpolating axes offers the highest flexibility. The inclination of this double-ended grinding spindle is indispensable for grinding drill points with point angles down to 55° as well as on long instruments.
Normally, two wheel packs are sufficient, so it’s not always necessary to have a wheel changer. The 6th axis flips one of the two wheel packs into grinding position in less than 2 seconds.
If a wheel changer can be avoided, then the cycle times over a long batch run become more attractive.
FOR MORE INFO: http://www.rollomaticusa.com

Explore the April 2019 Issue
Check out more from this issue and find your next story to read.
Latest from Today's Medical Developments
- Researchers invent soft, bioelectronic sensor implant
- HEULE’s DL2 tooling
- Application Park shows off diverse robotics applications
- Join our editors for a look at the manufacturing industry in 2025
- Surface Roughness, Texture, and Tribology Short Course
- There’s still time to register for our January 22 additive manufacturing webinar!
- EMO: Made for game changers
- Thomson’s encoder options for stepper motor linear actuator online selection tool