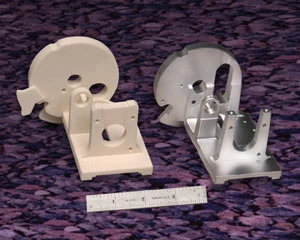
Manufacturing of high-precision components for a range of medical equipment can benefit from Graphicast's ZA-12 casting process. The Graphicast process - which uses permanent graphite molds to produce parts from ZA-12, a zinc-aluminum alloy - is an economical alternative to die casting, investment casting, sand casting with machining, and CNC machining of complete parts for production quantities from 300 to 30,000 parts per year. Graphicast's single-source production capabilities include in-house design, plaster model rapid prototyping, tooling and mold production, casting, and, if required, secondar y machining. Typical turnaround time from finished CAD design to first article samples is four to six weeks.
The production of a 4" x 3¾" cast and machined housing, one of four parts that Graphicast is making for a chemical analyzer, provides an example of the company's concurrent engineering services. For this job, Graphicast assisted the customer in converting the design, which was originally intended for CNC machining or plastic injection molding. As the design evolved, Graphicast provided plaster models of the part. When the customer was convinced that ZA-12 would provide better strength and lubricity than aluminum or plastic, Graphicast produced the mold and cast, and machined the parts at considerable savings over alternative processes.
ZA-12 zinc-aluminum alloy offers an excellent combination of physical properties, surface finish, and low cost. With approximately the same density as cast iron, ZA-12 alloy is harder, stronger, and better wearing than aluminum or bronze. It machines as easily as brass or bronze and more easily than cast iron or aluminum. Graphicast's exclusive LTA auto-pour technology produces castings with dimensional stability, low porosity, and exceptional consistency. No heattreating is required. Typically, graphite mold castings can be produced in volume with critical dimension tolerances of ±0.003"/in for the first inch and ±0 .001"/in for additional inches and surface finishes better than 125µ". Parts from the mold have a lustrous bright metal finish that, in most cases, requires no preparation or coating for corrosion protection. If desired, parts can be chromated, plated, painted, powder coated, or finished with electrocoated acrylic or epoxy to simulate black anodized aluminum.
Castings can include contours, var iat ion in sur face elevat ions, holes, and other precise features. Graphicast offers comprehensive design assistance, and state-of-the-art software facilitates any modification to draft or radii required to accommodate the casting process. Parts are cast to near net shape and can require no machining to meet tolerances. Secondary machining operations such as boring, drilling, and direct thread tapping are performed in-house on precision CNC machining centers with rotary axes. Dedicated fixtures, custom designed by Graphicast engineers, maximize repeatability and minimize cost.
Graphicast Inc.
Jaffrey, NH
graphicast.com

Explore the January February 2008 Issue
Check out more from this issue and find your next story to read.
Latest from Today's Medical Developments
- Supply Chain Power – A strategic program for executives
- Sunnen Products' PGE-6000 gage
- April Manufacturing Lunch + Learn with Iscar
- April Manufacturing Lunch + Learn with Insaco
- Laser cold marking for plastic medical device manufacturing
- Paperless Parts’ BOM Builder
- #58 - Manufacturing Matters - 2024 Metrology's Latest Advancements with Starrett
- Strategies to improve milling and turning for medical components