
Passivation removes free iron or iron compounds from the surface of stainless steel by means of a chemical dissolution process, reducing the chemical reactivity of its surface. Passivation facilitates the formation of a thin, transparent oxide film, which gives stainless steel its corrosive-resistant qualities.
Stainless steel possesses a variety of qualities that make it an ideal material choice for medical device manufacturers. Although there are 15 grades that are most commonly used, there are more than 150 grades. Stainless steel is relatively inexpensive, is a low maintenance metal, is 100% recyclable, and is resistant to oxidation, corrosion and staining. Stainless steel's ability to resist corrosion and stains is dependent upon the proper execution of one crucial step – passivation.
To date, electrochemical polishing (EP) is the most widely used and effective processes for passivating stainless steel. For some manufacturers and machine shops, the effectiveness of the EP process very well may be negated by its inherent drawbacks. The EP method is not without hazards. Perhaps the most adverse aspect of the EP method is the use of strong and often dangerous acids, which are heated to extremely high temperatures. Extensive training is needed by operators to learn how to properly and safely handle the chemicals, which can cause serious health problems, including chemical burns to the skin and eyes, and severe respiratory ailments. Additionally, EP operations cannot be integrated onto the shop floor, as they must be housed in a separate, properly ventilated area. The acidic electrolyte solution must be changed regularly, as it loses its effectiveness, and the subsequent disposal also poses environmental hazards.
With the process of passivating stainless steel primarily limited to EP, manufacturers and machine shops had, in the past, few alternatives. Extrude Hone, a Kennametal Company headquartered in Irwin, PA, offers a new pulse electrolytic technology, CoolPulse, for deburring, polishing and passivating stainless steel and other compatible metal components. Extrude Hone is the only U.S.-based company licensed to offer this proprietar y process.
VIABLE ALTERNATIVE TO ELECTROCHEMICAL POLISHING FOR PASSIVATION
The Extrude Hone CoolPulse process takes a significant step forward in electrolytic technology, performing five key advanced finishing functions all in one process. It deburrs, polishes, stress relieves, cleans and passivates, producing superior finishing and cleanliness results without compromising or stressing the structural or functional integrity of the component. On stainless steel, in particular, CoolPulse produces a highly reflective, mirror-like surface to such an extent that it appears to be chrome plated.

CoolPulse produces a surface that appears to be chrome plated.
While CoolPulse may be confused with EP because both processes involve immersing components in a bath and applying a low voltage DC current, the other characteristics of Extrude Hone's CoolPulse are entirely unique. One of the key distinctions between EP and CoolPulse is that the latter does not rely on a blend of dangerous acids or high temperatures. Instead, CoolPulse uses a specially formulated cold, near-neutral (pH 6.5) electrolyte solution, which is chilled between 32°F and 59°F. The solution is non-fuming and odorless, enabling a CoolPulse machine to be out on the manufacturing floor. The CoolPulse solution does not deteriorate with use and rarely, if ever, requires changing. The process re-circulates the solution through filters to extract any metal hydroxides, which renews it. As a result, manufacturers do not incur substantial costs for additional solution or for waste disposal.
During processing, a computercontrolled, pulsed, low-voltage direct current (DC) is applied between the stainless steel component and a stationary cathode. Close-fitting conformal electrodes are not required. As the electrical current flows, or pulses, through the cool electrolyte solution, it causes the ions to build up an electrostatic charge. A diffusion layer fills and protects the valleys of the part's surface structure while simultaneously creating a "peak effect," which allows the ions to concentrate on and attack these areas where the current is at its highest density — on the edges, burrs and recast stress risers. Special probe tooling can be used for direct processing to specific areas, such as internal features of a workpiece.

Ions concetrate on and attack areas where the current is at its highest density.
CoolPulse is capable of removing very rough surfaces – Ra of 2.5µm to 5mm and producing ultra-smooth surfaces down to 0.1mm – and is ideally suited for small- to medium-sized workpieces that may be inherently delicate or intricate by design.
Designed to function optimally at both low- and high-volume production rates, CoolPulse is significantly faster than EP. Average cycle times range from 15 seconds to 3 minutes, smaller components typically take 10 seconds to 15 seconds. At these rates, CoolPulse can process thousands of workpieces in a week.
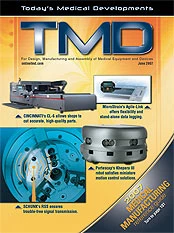
Explore the June 2007 Issue
Check out more from this issue and find your next story to read.
Latest from Today's Medical Developments
- HERMES AWARD 2025 – Jury nominates three tech innovations
- Vision Engineering’s EVO Cam HALO
- How to Reduce First Article Inspection Creation Time by 70% to 90% with DISCUS Software
- FANUC America launches new robot tutorial website for all
- Murata Machinery USA’s MT1065EX twin-spindle, CNC turning center
- #40 - Lunch & Learn with Fagor Automation
- Kistler offers service for piezoelectric force sensors and measuring chains
- Creaform’s Pro version of Scan-to-CAD Application Module