
Hip replacement, one of the most performed elective surgeries, is projected to grow more common in the decades to come. Manufacturers have developed innovative technologies to improve prosthetic implant quality while lowering cost per part.
Many key implant components are produced using metal 3D printing, but to achieve optimal per-part cost, workshops must look beyond additive manufacturing (AM) technology and consider the complete manufacturing process chain.
AM is often critical in orthopedic implant production due to its ability to create new types of functional geometries. This is especially true of acetabular cups, dome-shaped components that fit into the hip socket. Capable of producing intricate internal part geometries by building parts layer-by-layer, 3D printing can build trabecular structures – porous surfaces that mimic the appearance and biological functionality of bone for superior osseointegration.
Geometric complexity requires precise AM techniques, and the best solutions use powder bed fusion. Two technologies stand out among today’s 3D metal printing solutions – electron beam melting (EBM) and laser powder bed fusion (LPBF), both of which have distinct advantages and disadvantages for medical parts.
An electron beam with a large spot size and high power makes EBM productive and efficient in terms of per-part costs. EBM also allows for easy and almost support-free stacking.
While EBM’s greater build speed has made it more common in many medical workshops, LBPF can be more competitive when manufacturers optimize part manufacturability by integrating automation and conventional manufacturing strategies.
To develop this approach, GF Machining Solutions, a hardware and software solutions provider, collaborated with Monza, Italy-based Hofmann Srl, a medical device manufacturer specializing in orthopedic implants. Together, they reconsidered the three stages of the manufacturing process for acetabular cups and found solutions to optimize workflow.

Design stage
Stacking strategies are especially useful in AM, as building parts layer-by-layer achieves a more efficient exposure-to-recoating ratio. This maximizes the laser-on (active) time and minimizes the impact of the recoating (inactive) time on part cost.
The stacked strategy enables manufacturers to build significantly more parts per job – up to 450 units with GF Machining Solutions’ DMP Flex 350 – reducing the impact of machine setup and turnaround time on part cost. The stacked approach also enables designs optimized for multiple parts without using significantly more material than the amount necessary for a single layer of parts.
Supports can be handled easily using automation with the stacked strategy. When combined with System 3R BuildPal, this design enables automated post-processing operations to be performed on each stack of parts, eliminating manual finishing. This also reduces machine setup and changeover time at the finishing stage, minimizing idle time compared to traditional finishing setups that machine and finish each part on its own.
GF Machining Solutions offers comprehensive software to support these support structures with AM workflow features. 3DXpert offers several ways to optimize design structures, including the ability to quickly design and edit lattice structures that can be saved for later use.


AM stage

3DXpert software allows manufacturers to design supports that eliminate the need for manual post-processing of part stacks, which can instead go directly to the machining stage following AM build. This support strategy allows for depowdering the stack after the build cycle, as well as proper and secure separation of individual units at the machining stage. These supports can be used outside of the build chamber instead of being discarded in the usual fashion. Their geometry can also be used to clamp a part in turning operations.
The System 3R BuildPal automation solution eliminates the need to separate parts from build plates, an operation that usually adds to part cost. It’s replaced in this approach with a cost-efficient turning operation. The System 3R BuildPals are separated from the part stack during the first machining operation following the AM process, and the plates can be easily refurbished for reuse.
Machining stage

While AM offers new and exciting possibilities for complex implants and biomedical products, components still need further machining and finishing. This usually requires expensive workpiece fixturing devices for clamping and referencing these components in subsequent processes.
System 3R offers a range of pallet sizes as a solution for this issue. Using a conventional lathe, manufacturers can cut each pallet from the stack directly, allowing the separated BuildPals to be used for further AM work while post-processing continues.
Following pallet separation, each stack is machined to finish the functional surfaces of the parts to meet high accuracy and surface finish requirements. For each part of the stack, the inner concave geometry is finished, then the base and side surfaces, and then the unit is separated from the stack. Lastly, the outer interfaces are machined.
Final part

To achieve the most cost-effective process, consider the part-production cycle holistically, with a focus on part manufacturability from the beginning of the design process. The lowest ownership and per-part costs do not come from the fastest machine for a single process, but from systems that work together seamlessly for the short lead times and high part quality.
This can best be accomplished with turnkey systems that combine additive and subtractive technologies with process expertise and software available from original equipment manufacturers (OEMs) such as GF Machining Solutions. The increased productivity of this stacked hip cup process comes from innovations at every stage of production – design, printing, validating, and finishing – as well as optimized setup and part changeover. By bringing various manufacturing technologies, including DMP metal printers, System 3R tooling, and 3DXpert software, into a single, fully integrated workflow, GF Machining Solutions allows workshops to achieve significant per-part cost savings.
GF Machining Solutions
https://www.gfms.com
Hofmann Srl
http://www.hofmann.it
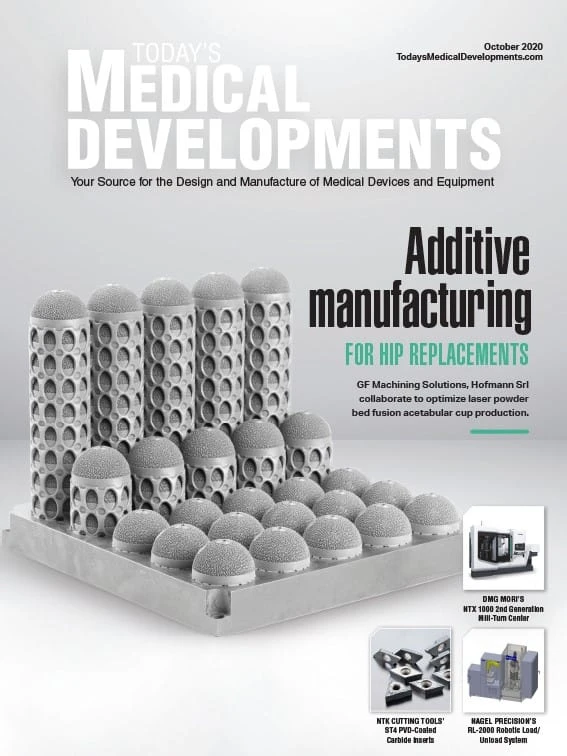
Explore the October 2020 Issue
Check out more from this issue and find your next story to read.
Latest from Today's Medical Developments
- STUDER looks back on a solid 2024 financial year
- HANNOVER MESSE 2025: Tailwind for industry
- Find out the latest developments in tool path strategies for machining
- Building, maintaining the Navy’s next generation of maritime platforms
- Pioneering battery-free cardiac implants
- KBC Tools & Machinery marks its 60th anniversary, Founder’s Day
- Address the challenges of machining high-temperature aerospace components
- Elevate your manufacturing operations with April’s Manufacturing Lunch + Learn