
Is your quality system helping or hurting your bottom line? Many medical device manufacturers look at managing quality merely as a means of avoiding compliance issues – a mentality that can lead to increased inefficiencies and out-of-control costs.
Quality and compliance
While medical device companies grapple with an ever-expanding array of large-scale industry trends (the world’s aging population, emerging markets, increased regulation, healthcare reform), they can’t afford to ignore an essential issue that hits even closer to home: their own quality management. An effective quality management system (QMS) does much more than satisfy compliance requirements, standards, and directives from the world’s leading regulatory agencies, such as Food and Drug Administration (FDA) (21 CFR parts 820 and 11) and ISO 13485. A first-rate QMS software solution that automates and connects quality processes from design control to post-production audit, and provides a web-based, centralized repository for all documentation, improves operational efficiency and agility, which in turn has a dramatic impact on profitability.
Decreasing cycle times
The implementation of an effective QMS increases revenue by allowing an organization to implement product enhancements quicker and reduce risk. But most importantly, it can shorten the time between a product’s conception and when it hits the market. Efficient quality management increases speed to market by decreasing the amount of time required for the myriad of compliance and business activities associated with new product development in a regulated environment.
QMS fundamentals
When launching a new line extension or introducing a product evolution, an effective QMS is invaluable. There is an undeniable correlation between the effectiveness of a company’s QMS and its ability to quickly analyze and assess the efficacy of each component of its existing products. Near the beginning of a project, engineers start with a detailed complaint and failure analysis of the previous generation. This work is greatly facilitated and more complete when the QMS is well established and efficient.
Manufacturers typically face risk-related device design challenges such as the Six M’s: machinery, material, manpower, Mother Nature, measurement, and method. A company must continually take into account, based on intended use, how a device is affected by these risk factors. A robust QMS system that provides a simple and consistent process for assessing risk helps medical device manufacturers navigate the rough roads of medical device development. The company with the most effective QMS is best equipped to assess and mitigate risk before a product ever gets out the door. Design teams are able to work in a consistent manner from the point of inception, rather than correcting mistakes later when it is far more costly.
Supply chain
Components that go into a medical device must be monitored and quality-assured for compliance purposes, so QMS can have a significant impact on suppliers and supply chain management. A QMS provides consistency and extends collaboration, communication, and approvals to include multiple facilities, vendors, and suppliers, regardless of geographic location. A company’s QMS is only as effective as its ability to unite the supply chain and bring suppliers into the design and development process. The earlier this takes place, the better, because as with any quality process, problems are more expensive and time consuming to fix later. Such problems are magnified when dealing with suppliers, so improving communication and helping them provide materials more efficiently will help accelerate the product’s time to market.
A company-wide QMS solution
Checks kept in place by a QMS system reduce the likelihood of recalls that can damage a brand’s reputation.
“Addressing quality is just like driving,” says Walt Murray, director of quality and compliance advisory services at MasterControl. “You can’t just be defensive; you must be offensive to survive.”
There is no more important step a medical device company could take to realize profits sooner without compromising compliance than implementing an effective and efficient QMS solution.
MasterControl
About the author: MasterControl Executive Vice President Matthew M. Lowe can be contacted through www.mastercontrol.com.
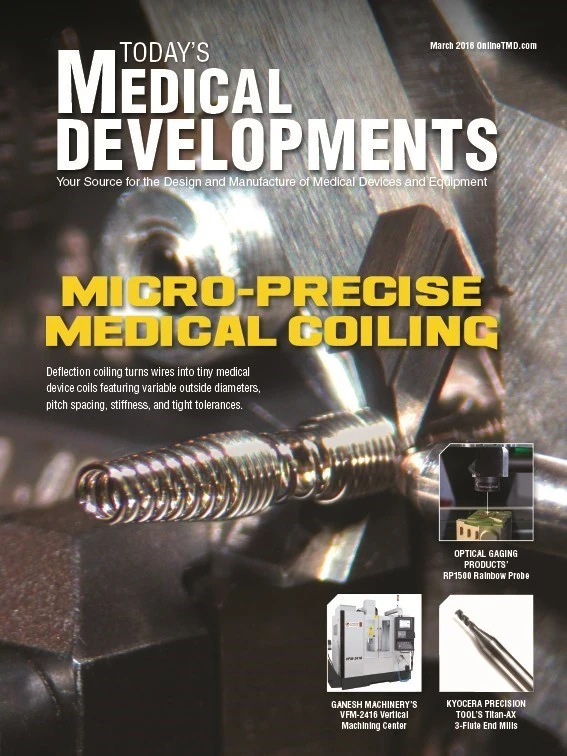
Explore the March 2016 Issue
Check out more from this issue and find your next story to read.
Latest from Today's Medical Developments
- MedTech Innovator welcomes five new industry partners
- First Article Inspection for quality control
- The manufacturing resurgence is here – are you ready?
- Workholding solutions for your business
- ZOLLER events will showcase the company’s cutting-edge innovations
- THINBIT’s MINI GROOVE ‘N TURN Acme threading inserts
- CMMC Roll Out: When Do I Need to Comply? webinar
- Metabolic research uses Siemens gas analyzers to deliver results with 99.9999% resolutions