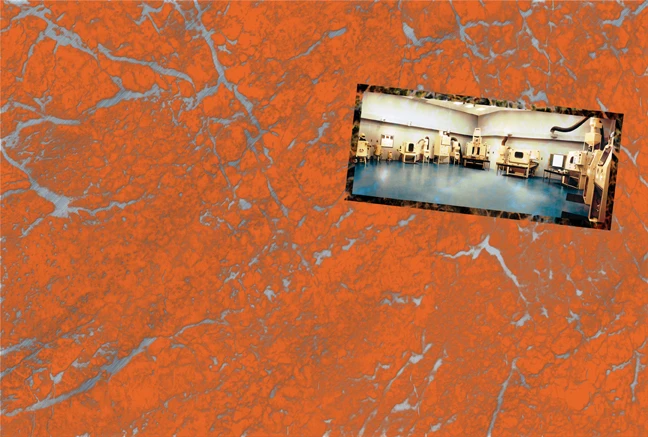
Within the field of medical devices, abrasive blasting plays both cosmetic and functional roles. Its ability to create precise textures, for instance, is exploited in a number of ways. By adding small hills and valleys to surfaces of implants and fasteners, blasting increases the parts areas. This strengthens adhesions to coatings as well as bone and/or tissue. Surface profiling also improves the performance of clamps, electrical blades and various other devices while providing an assist to operating teams by minimizing glare from implants and instruments under surgical lighting.
Strengthening spinal rods and other metal implants is another job performed with blasting. Called shot peening, the process involves bombarding surfaces with spherical media to create compressive residual stress, which in turn produces dramatic gains in fatigue life and stress tolerance. In fact, the aircraft industry, which relies heavily on peening, reports strength increases of 40% and fatigue-life extensions of 10 times in some instances when the process is properly applied.
Another major blasting application involves removing unwanted residues including heattreat scale, flash and burrs without damaging the product from which the material is being removed.
Not unlike surgery, most blasting jobs in the medical field require precise control. Whether the task is producing a specific texture, peening to a prescribed intensity, or removing residue without substrate damage, blasting's ability to perform successfully depends on the proper coordination of multiple variables.
Operating Principles
Blasting alters surface and sub-surface characteristics by bombarding workpieces with angular or spherical particles referred to as "media." Energy can be imparted to the media either mechanically or pneumatically. For large-scale manufacturing operations where "targeting" is not critical, mechanical systems, which employ a spinning wheel to fling media at work surfaces, offer the advantages of speed and efficiency. On the negative side, these systems lack the precision and flexibility normally required in finishing medical devices. Consequently, they play almost no role in the field.
Pneumatic systems, by contrast, can be configured to clean tiny areas like human teeth or immense ones like the sides of oil tankers -- and almost anything in between. These systems rely on either a "suction" or "pressure" arrangement to accelerate media through a feed line and nozzle toward the work surface. Although both setups depend on compressed air to energize the blast process, they work in different ways.
Suction-blast systems use the venturi principle to induct media from a storage hopper to a blast gun where the discharge is focused on a workpiece. This approach offers a number of advantages, including low initial cost and amenability to automation. For example, configuring suction systems to perform continuous media refills or support multiple blast guns (a key feature in automated equipment) is normally a straightforward undertaking.
Although the same level of sophistication is available with pressure-blast systems, it typically comes at a higher cost, mainly because more components must be pressurized. Nevertheless, pressure offers major advantages in terms of speed, efficiency and precision.
With pressure systems, the media-storage tank operates at a pressure equal to that in the air-blast line and a valve controls the rate of media flow. When the system is actuated, media is gravityfed into a high-velocity air stream and then propelled through a nozzle at the work target. Because media is accelerated continuously as it moves through the feed line, more velocity is imparted per unit of compressed air than with a suction system. Depending on application specifics, pressure systems can perform four times as efficiently as their suction counterparts. In addition, they provide more precise control over a broader pressure range and work more effectively with light media such as plastics and bicarbonate of soda.
Configurations
Industrial blasting requires enclosures to prevent abrasives, dust and residual debris from spreading into the workplace. Consequently, blasting is performed within blast rooms, where the operator and workpiece are contained, or within a blast cabinet that enables control from outside of the blasting enclosure. Rooms, however, which range from makeshift structures housing a blast "pot" to finely engineered production facilities, are rarely used in the manufacture of medical devices. They are designed to handle locomotives, artillery and other parts too large for cabinets.
Blast cabinets, on the other hand, play roles ranging from the microcleaning of stents to the shot peening of spinal rods. In its most basic form, the cabinet consists of an enclosure in which an operator, using sealed gloves that protrude into the work area, manipulates parts in the path of a blast stream. Production-grade cabinets, whether driven by suction or pressure, normally include a mediarecycling device that recovers "good" shot or abrasives while removing dust and fines - an essential feature in any process aiming for economy and repeatability. In addition, these cabinets can be upgraded with accessories for automating blast coverage and duration, as well as movement of workpieces within the blast envelop. Motors to drive turntables or fixturing, powered lances that penetrate recessed areas, and rotary blast heads with multiple moving nozzles serve as basic examples.
Often, users choose to automate certain functions with standard equipment to reduce capital costs. The addition of a nozzle oscillator to a stock cabinet, for instance, can free the operator from having to manipulate the nozzle manually. Likewise, part rotation can be combined with nozzle movement and timing devices so workpieces can be processed automatically in cycles. Although these techniques are relatively simple and inexpensive, they can produce subconsistency. Many one-of-a-kind blasting jobs are today being automated with off-the-shelf components.
Dedicated Systems
The deburring of cannula tips on hypodermic needles demonstrates blasting's prowess in the dedicated mode. A needle manufacturer, faced with a bottleneck of burrs between its grinding and ultrasoniccleaning stations, solved the problem with an automated blasting machine capable of breaking the bottleneck and dovetailing with work flow. Designed to accept the strips on which needles are ganged for grinding, the machine deburrs cannulas of various lengths and gauges at rates exceeding 20,000 pieces per hour. Because the system "sharpshoots" by positioning nozzles in three planes to within 0.001-in and 0.01º, masking is not required.
Blasting's versatility continues to grow in proportion to the capabilities of information-processing systems. Cheaper and more sophisticated controls have made automation less expensive, because one machine can now process different types of parts without extensive manual adjustments. To "program" a workpiece, operating instructions related to nozzle movements, blast pressure and duration, and part movement are entered via a control board. Once blasting parameters for a specific part have been defined through testing, they can be stored in memory and retrieved with pushbutton ease.
The blasting process benefits from computer controls for a variety of reasons, foremost being the many variables affecting results and, not to be overlooked, the need for documentation of blasting histories on medical devices, directly associated with human health. TMD
Empire Abrasive Equipment
Langhorn, PA
empire-airblast.com
Jerry Conover is the Automated Systems Manager for Empire Abrasive Equipment Company.

Explore the June 2006 Issue
Check out more from this issue and find your next story to read.
Latest from Today's Medical Developments
- Birk Manufacturing achieves ISO 13485 recertification
- SW North America's BA 322i twin-spindle CNC
- The role of robotics in precision medical device manufacturing
- Swiss Steel Group’s UGIMA-X machinable stainless-steel sets
- #51 - Manufacturing Matters - The Impact of M&A in MedTech 2024
- Visual Components: 25 years of simulation and programming software innovation
- Zimmer Biomet announces definitive agreement to Acquire Paragon 28
- Discover an innovative technology for EMI/ESD/TVS suppression