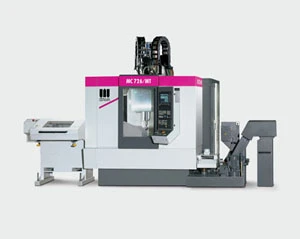
The mill/turn machines and vertical machining centers produced by German machine tool builder, STAMA, focus not only on machining cycles but on minimizing the number of individual operations needed in order to increase productivity while lowering production costs.
As the manufacturer turned its attention to development of its new System 7 milling/turning center, a driving force in its creation was to meet customer needs for twin-spindle and single-spindle work to be economically processed on the same machine.
Previously when the work involved small and medium batches, the economics of using a multi-tasking machining center weighed against it. As a result, the work was handled on a number of machines. Perceiving a market need, STAMA looked to produce a machine for shorter production runs. The machine would have to be capable of milling, drilling, thread cutting, external/internal turning, facing, and contouring.
"Compounding our challenge," says Gerhard Ulmer, the company's director of sales, "we had a great demand for high accuracy under production conditions, because our automotive and our medical customers require it. True position of 0.02mm under 1.67 Cpk conditions are typical for our twin spindle machines. With some of the extreme alloys our customers process, holding that standard would not be so easy to achieve."
The answer to these challenges is System 7, a machining center on which a single five-axis milling spindle is combined with one or two turning spindles and trunnion-mounted workpiece positioning for true six-sided, fully-automated machining of blank bar stock or from a chuck.
The machine has a high degree of motion control and accuracy and is multifunctional. It has the capability to machine one piece with two spindles; run separate smaller parts on each spindle independently; change tooling on one spindling while the other is machining; and for true six-sided machining, one spindle has the ability to act as the rotary actuator for the workpiece. All of this is accomplished with relatively short set-up and changeover times
Obviously the selection of the right controls was critical to the succ ess of the d esign and operations of the System 7. The choice for STAMA is the Siemens SINUMERIK 840D with NCU (Numerical Control Unit) 573.5, a CNC with op en architecture. The PC-based design is capable of h andling up to 31 axes and 10 channels.
In addition, motors, po wer supplies an d driv es from Siemens were also incorporated in the System 7, which is a turnkey package. In order to speed cutting a nd finishing time for p arts, the milling/turning center incorporates Siemens TRAORI software suite. The uniqu eness of the software is that it's based on th e transformation orientation that drives cutting motions relative to the position of the workpiece, not the NC program. Ulmer explains that, "We did some modifications of their software for the particular needs of our customers, but the base model and the flexibility of the Siemens CNC package made this supplier the o nly cho ice for STAMA on the System 7. It's the first true control package for a mill/turn machine in the world."
Important to Ulmer and the STAMA developers is that the Siemens c ontrol is b oth robust and safety-conscious. Both characteristics are of utmost importance for producers of me dical devices. Of further consequence for the medical market is the sturdiness of the System 7 and the ability of the CNC to detect out-of-tolerance tools. As Ulmer notes, when cutting cobalt chromium, Nitinol (nickel titanium), and other alloys commonly used in the production of medical implants, surgical tools, and instruments, tool wear is a rule rather than an exception.
Coop eration of Siemens engineering was vital to the development process on this new milling/turning center. ""I can say without hesitation that th e Siemens CNC was key to the development of the System 7 as well as our System 8, designed for the larger workpieces and chucks," c on cludes Ulmer. "It is a true example of simultaneous engineering on our part and theirs, to devise the best result. Moreover, our customers report a true 30\% reduction in part cost with the System 7 and that's really the best result from this entire process." TMD
Learn more about STAMA at www. stama.com and more about Siemens at www.SiemensCNC.com.

Explore the July August 2006 Issue
Check out more from this issue and find your next story to read.
Latest from Today's Medical Developments
- Kistler offers service for piezoelectric force sensors and measuring chains
- Creaform’s Pro version of Scan-to-CAD Application Module
- Humanoid robots to become the next US-China battleground
- Air Turbine Technology’s Air Turbine Spindles 601 Series
- Copper nanoparticles could reduce infection risk of implanted medical device
- Renishaw's TEMPUS technology, RenAM 500 metal AM system
- #52 - Manufacturing Matters - Fall 2024 Aerospace Industry Outlook with Richard Aboulafia
- Tariffs threaten small business growth, increase costs across industries