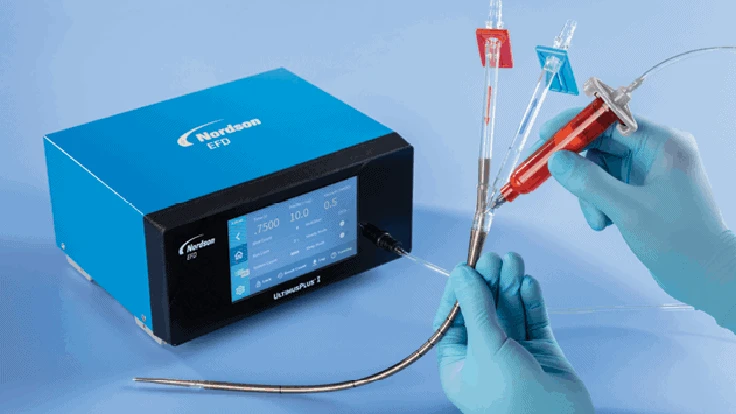
Nordson EFD

For critical dispensing requirements that demand exceptional process control, benchtop fluid dispensers often deliver high levels of precision dispensing. Features can include time adjustment as fine as 0.0001 seconds and full electronic air pressure regulation for operator lock-out of dispensing parameters. These applications require small amounts of adhesives, silicone, and other fluids that must be dispensed reliably and accurately in dosage, placement, and repeatability. Crucial to the products’ assembly, function, quality, appearance, and viability are the precise positioning and quantity of deposited fluids.
Despite the proliferation of robotics and machine/process interconnectivity in manufacturing, fluid dispensing in medical device assembly largely remains a semi- automated, pneumatic benchtop process. A technician often holds a fluid-filled syringe barrel connected to a dispenser, points the tip, and pushes the foot pedal to dispense fluid in a dot or line.
The nature of these medical devices warrants a more personalized, manual fluid dispensing approach in assembly, compared to more automated, robotic systems used in high-volume, low-mix operations.
Quantum leap for dispensing
Today’s pneumatic benchtop fluid dispensing advancements facilitate easier and more efficient operation while maintaining better dispensing parameter process control for more consistent outcomes.
Semi-automated desktop fluid dispensers can be compatible with Ethernet, the Industrial Internet of Things (IIoT), and the Cloud, enabling more direct machine/process interconnectivity. While beneficial where benchtop fluid dispensing systems are used in combination with robotic dispensing applications, enhanced connectivity can also benefit non-robotic pneumatic benchtop fluid dispensing. Improvements allow the benchtop dispense technician to use smart-factory digitization.
Incorporating these developments, Nordson EFD’s UltimusPlus line of pneumatic benchtop dispensers provide nine key capabilities.
1. Human machine interface (HMI)
UltimusPlus incorporates an HMI touchscreen control to input dispensing parameters and manage dispense process functions, bringing greater usability for operators and production managers. The touchscreen control enables faster setup than analog knobs and push-button controls.
The intuitive large-format screen also displays process information, simplifying setup and programming, allowing operators to focus on the process. It also reduces setup time for any new fluid dispensing operation.
2. Automated pressure regulation, full operator lock-out
Particularly with medical device assembly, it’s critical that fluid dispensing be administered precisely and in the same repeatable pattern on each component.
Pneumatic benchtop fluid dispensers typically allow operators to manually adjust pressure regulation. Today’s dispenser can fully lock out the operator, preventing manual changes to pressure regulation and other dispense parameters such as time and vacuum settings. Without an assigned password, the operator cannot change program parameters, improving process control at a lower cost of ownership.
Electronic pressure regulation provides full operator lockout and enhances dispense quality control by eliminating process inconsistencies caused by operator-to-operator variability.
3. Barcode scanning
The ability to switch between stored dispensing programs using only a barcode scanner allows the operator to change parameters for a new application without touching process parameters on the screen. Most medical device components have a unique barcode assigned to them as they move through the production/assembly process to keep track of the components throughout production, so when the new program barcode is scanned the dispenser settings automatically switch.
UltimusPlus also offers the option to scan the lot barcode directly into the dispenser’s memory, ideal when a factory is processing multiple parts throughout the day, and it adds complete part traceability.
4. Memory programs store project parameters
UltimusPlus permits the selection of time, pressure, vacuum, and other parameters for fluid dispensing on a specific project, as determined by plant and project requirements. These settings are locked and stored in the dispenser and can be called up at any time to run with the associated project. Up to 16 memory programs can be set up and stored in the dispenser’s memory.
Not having to maintain dispensing parameters in handwritten spreadsheets and notepads, and manually entering coordinates into the dispenser on subsequent runs, reduces or eliminates the possibility of human error.
5. Dispense log data
A digital dispense log automatically records parameter data – such as dispense time, pressure, vacuum, number assigned to identify the component part, and date, day, and time of each dispense cycle. The log can contain up to 10,000 lines of data and is manually downloadable through the dispenser’s USB port.
The dispense log supports stringent, documented process control, especially critical in life sciences applications that must meet U.S. Food and Drug Administration (FDA) requirements and/or those of other global medical device regulatory bodies.
6. Multiple shots, single cycle
The UltimusPlus reduces operator fatigue by minimizing repetitive movements while permitting multiple shots with a single dispense cycle.
Engaging this function via the touchscreen allows the operator to make multiple deposits with only one cycle initiated and one press of the foot pedal. MultiShot allows a single dispense cycle to make dozens or hundreds of shots with one foot pedal press. A pause is programmed to occur between each deposit, allowing the operator time to position the tip on the next part. The system essentially executes the exact same shot, based on the same time, pressure, and vacuum settings.

7. Sleep mode
A sleep mode can significantly reduce operating costs for plants using bottled compressed air, such as in cleanrooms in medical device manufacturing or in facilities operating dozens to hundreds of dispensers.8. Flash drive program download
A USB port permits outputting dispense reports to a flash drive, enabling distribution of dispense programs into and out of the dispenser. This can cut programming time considerably when multiple units are set up to dispense identical parameters on the same parts; one dispenser can be set up with multiple programs and those parameters are then output to a flash drive and loaded into the other dispensers, minimizing human error and expediting loading of dispense programs across the factory floor.
9. Smart factory integration
For robotic applications, UltimusPlus integrates smoothly with Smart Factory Industry 4.0 initiatives, encompassing Ethernet, machine-to-machine technology, IIoT, edge computing, and the Cloud.
The dispense cycle can be initiated by a centralized, customer-site-specific programmable logic controller (PLC) as part of a large, in-line operation. When the production line needs to move from making one type of part to another, the PLC will remotely trigger the dispenser to change the program and dispense a different deposit pattern.
Engineers designed the system to meet the most stringent fluid dispensing needs of today’s highly precise medical devices and to embody the essential components to integrate with the ongoing evolution of the smart factory.
Nordson EFD
https://www.nordson.com/en/divisions/efd


Explore the September 2020 Issue
Check out more from this issue and find your next story to read.
Latest from Today's Medical Developments
- MedTech Innovator welcomes five new industry partners
- First Article Inspection for quality control
- The manufacturing resurgence is here – are you ready?
- Workholding solutions for your business
- ZOLLER events will showcase the company’s cutting-edge innovations
- THINBIT’s MINI GROOVE ‘N TURN Acme threading inserts
- CMMC Roll Out: When Do I Need to Comply? webinar
- Metabolic research uses Siemens gas analyzers to deliver results with 99.9999% resolutions