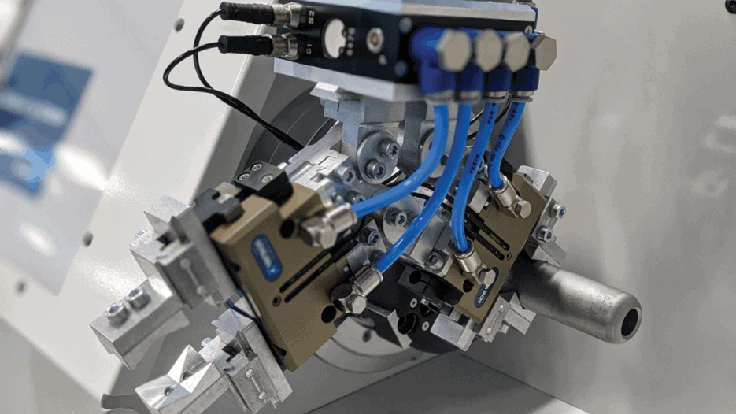
Schunk

As manufacturing facilities reopen and more people return to the workplace, there’s still a huge amount of uncertainty concerning the global Coronavirus. Many states aren’t through the worst of it, and there are fears of a second wave. The hardest thing during the pandemic is the ever-changing playing field. How can anyone make investments to plan for a future that changes daily? Instead, most companies are simply navigating through what’s in front of them today.
Questions and answers about how to prepare for a future outbreak will be different for each industry or company, but some broad topics can be considered, so you can be in the best position to adapt to whatever the rest of 2020 and beyond may look like.
1. Flexible automation solutions for unknown futures
SCHUNK addresses this with its new Flex Grip Tools program – a modular End-of-Arm-Tool system for lightweight and ease-of-use robots. With a little forward planning, a modular system allows an application to be adapted or a different type of workpiece to be easily accounted for, often without any further CAD work.
2. Plug & Work solutions to start automating
If you are thinking of automating some of your manufacturing processes, now is a good time. It’s easier than ever to get started with many complete Plug & Work portfolios that are directly compatible with robot arms from different manufacturers. SCHUNK is the world’s first manufacturer of these products and offers an extensive range of standardized components for various cobots and lightweight robots.
3. Creating a local supply chain
Supply chain uncertainty throughout the pandemic has caused great concern for many. SCHUNK worked with a partner to help a company pivot its manufacturing output to produce N95 masks. The company’s now able to do its part to keep the U.S. production of medical masks moving, even if the supply chain suffers further disruption in the future.

4. Reduce machine downtime, streamline processes
It’s always a good time to consider reducing machine downtime and increasing output, especially now. One of the best ways to safeguard future manufacturing is to ensure that downtime and part changeover time are streamlined. One way is to think about quick change pallet systems with very high repeat accuracy, allowing the next part to be set up outside of the machine while the previous part is running, reducing idle machine time between parts. The SCHUNK VERO-S quick change pallet system is modular with more than 1,000 variants for precise workpiece clamping.
5. Reduce need for outside contact during installation
Bringing outsiders into your building to install or maintain equipment is a concern. Think about implementing a solution that your own in-house team can easily install and maintain with virtual support from the supplier. SCHUNK USA recently partnered with Ready Robotics to create an automated process for ventilator component production that could be installed quickly and managed in-house with little production downtime. It was implemented by its own people to limit virus exposure.

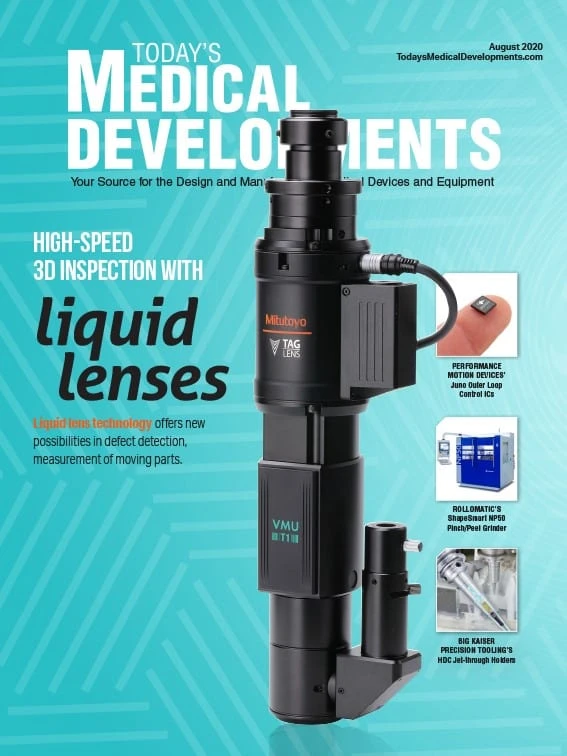
Explore the August 2020 Issue
Check out more from this issue and find your next story to read.
Latest from Today's Medical Developments
- AI meets innovation: Cambridge's device transforms heart screening
- Mazak and Premier Engineering team up for greater agility in Florida
- Struggling with inventory or supply chain pressures? Find answers in our free webinar
- Free webinar: Advanced manufacturing solutions to support the Navy
- A 30-year journey through CAM: Insights on simulation technology
- Behringer Saws’ HBE663A Dynamic horizontal bandsaw
- North America's supply chains face sharp decline due to tariffs
- Experience precision: GF Machining Solutions' CUT F Series wire EDM