A Quality Management System (QMS) is a framework for how you design, develop, manufacture, and distribute a product. It’s also how you take customer feedback and what you do with that feedback, impacting how you continually improve your business and product.

In the medical device industry, a QMS is essential because it’s required for device approvals in most countries by FDA 21CFR820 (US) and ISO13485 (OUS). Having a QMS also provides consistency and efficiency in a business, documenting procedures for most major areas.
Regulations require a QMS, however, it’s up to the manufacturer to determine how to meet requirements.
It must be efficient, or no one will want to follow it. And it must be adaptable, or employees will find alternatives, derailing any efficiency and consistency built into the QMS.
Consider current industry trends and regulations:
Risk-based QMS – These systems are no longer one-size-fits-all. Less product safety risk should lead to a less rigorous path to meet requirements. Your QMS should reflect the risk associated with your product.
Software-based QMS – Once reserved for stable, mature, large corporations, more software-based QMS solutions are present in mid- to late-stage startup companies, largely because of their inherent efficiency, traceability, and paper reduction.
Social media – Whether it has a presence on social media or not, your company can be responsible for statements made on these platforms. It’s important that your QMS is poised to contend with social media.
Supplier management – In today’s mergers and acquisitions, it’s becoming harder to know who your suppliers really are. And what about the suppliers’ suppliers? The rise in outsourcing has made it more difficult to ensure the quality of your supply chain, so the QMS must be able to navigate these ever-changing waters.
Regulatory environment – Regulatory changes domestically and internationally, such as Unique Device Identifiers (UDI), European Medical Device Regulations (EU MDR), and Medical Device Single Audit Program (MDSAP), have been introduced. More changes are expected, so a QMS must be flexible enough to adapt.
4 steps to adopting the right QMS for your business:
STEP 1: EVALUATION
To understand your business needs and the regulatory requirements, consider:
- How many people process complaints
- What other tasks are they performing
- Product risk
- Current complaint handling
- Anticipated challenges – more products, higher or lower risk products, fewer or more complaints, processing people, distribution to more countries
Information needed
- Regulation requirements – Domestic, foreign requirements
- Metrics – Complaint trends, process bottlenecks
Budget
- System, implementation, validation, maintenance, licensing, support costs
STEP 2: ASSESS THE CAPABILITIES
- Ease of use
- System changes – Adaptable in-house or by provider
- Employee access – By person, department, user profile; read/write, read-only
STEP 3: TIMING THE PROCESS
- Setup
- Validation
- Implementation
- Maintenance
STEP 4: PROCESS EVALUATION
After you’ve implemented your complaint- handling system and have experienced some run time with it, evaluate the process.
Is your system helping identify complaint trends?
– If not, determine what additional information and/or reporting is needed
Is your system feeding complaint information back into the quality system to facilitate continual product improvement?
– If not, determine what information must get to which part of the organization and implement a defined process for information transfers
– Information is transferred through automated reports, periodic presentations, notification of received, and/or investigated complaints
Are you getting the expected efficiencies?
– If not, identify the bottlenecks and determine necessary changes
– Sometimes, you must simplify the system to make it efficient
Is your system facilitating compliance?
– If not, determine where the gaps are and identify essential changes
Is your system adapting to your business needs?
– If not, consider simplifying your system to provide the necessary flexibility
– Periodically re-assess the system and make continual improvements as necessary
Omnify Software
http://www.omnifysoft.com
EarLens
http://www.earlens.com
Adapted from an original article by Rasean Butler, Director of Quality, EarLens, and Chuck Cimalore, CTO, Omnify Software
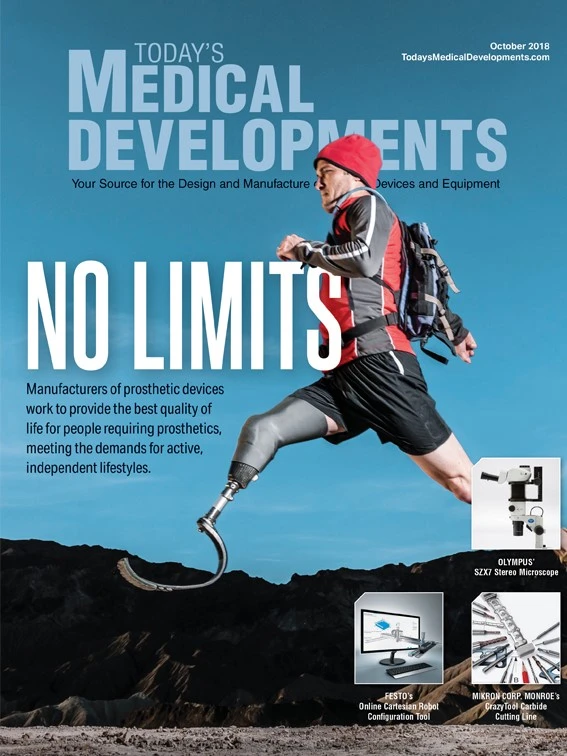
Explore the October 2018 Issue
Check out more from this issue and find your next story to read.
Latest from Today's Medical Developments
- HERMES AWARD 2025 – Jury nominates three tech innovations
- Vision Engineering’s EVO Cam HALO
- How to Reduce First Article Inspection Creation Time by 70% to 90% with DISCUS Software
- FANUC America launches new robot tutorial website for all
- Murata Machinery USA’s MT1065EX twin-spindle, CNC turning center
- #40 - Lunch & Learn with Fagor Automation
- Kistler offers service for piezoelectric force sensors and measuring chains
- Creaform’s Pro version of Scan-to-CAD Application Module