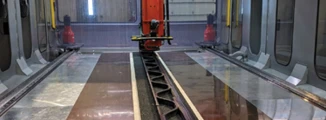
Expensive, long-lead time tooling can limit aerospace development. To help solve this challenge, Bell engineers reached out to Thermwood, developer of large-scale additive manufacturing (LSAM) technology.
The Thermwood team offered Bell Flight the capabilities of 60mm melt core technology for manufacturing large-bond tooling.
Bell responded by providing Thermwood a model of a closed-cavity blade mold measuring 240" x 14" x 17".
Basic tooling requirements were:
- Must be printed in one continuous run for vacuum integrity
- Surface finish must be 32rms or better
- Tooling must withstand 90psi at 360°F
- Tight tolerances, features to ensure proper mating of the two blade-mold halves
The process
Upon receiving the model and requirements, the Thermwood team began to print the tool in one continuous run using Techmer PM’s 25% carbon fiber-reinforced PESU (polyethersulfone), a material formulated for LSAM printing.
One tool-half was printed in 3 hours, 8 minutes, weighing 542 lb using the 60mm melt core installed on Thermwood’s LSAM system at its Southern Indiana Development/Demonstration Lab.
Continuous-cooling print process
With Thermwood’s room-temperature, continuous-cooling print process, the cycle time for each layer is determined solely by how long it takes a printed polymer to cool enough so it’s ready to accept the next layer.
Printing at the proper temperature achieves a fused, void-free printed structure that will maintain vacuum in an autoclave without a coating. The print head output determines how much material can be printed while the layer cools. Bigger print heads make larger parts, not necessarily faster print times.

The 60mm melt core has a maximum output of 480 lb/hr to 570 lb/hr, depending on the polymer. It can print more than 100ft of typical 0.830" x 0.200" print bead per minute. This high print rate, even with high-temperature material, allows orienting the print bead along the tool’s length where thermal expansion is lower, minimizing tool expansion and contraction with temperature changes.
Internal support structure
The tool’s internal printed structure supports the mold without touching the back of the mold cavity, allowing air to flow freely under the entire formed part in the autoclave, for easier, more consistent part-curing. Incorporating complex internal structures is possible with Thermwood’s LSAM Print 3D slicing software.
Multiple processes
The LSAM can print, trim, and drill to specifications. The team machined the printed, lower blade mold-half using the LSAM’s subtractive ability in 40 hours.
The Thermwood team will print the second half of the blade mold so Bell engineers can cure a full, molded blade within the complete additively-manufactured bond tool.

“This raises additive manufacturing to a new level, opening opportunities only dreamed of a few years ago,” says Ken Susnjara – Thermwood’s founder, chairman, and CEO.
LSAM advances – vertical layer printing, changeable melt cores, polymers tailored for LSAM processing – are opening new possibilities for additive production of larger, more complex components.
Bell Flight
https://www.bellflight.com
Techmer PM
https://www.techmerpm.com
Thermwood Corp
http://www.thermwood.com

Explore the Additive Manufacturing Guide Issue
Check out more from this issue and find your next story to read.
Latest from Today's Medical Developments
- Strategies to improve milling and turning for medical components
- Being proactive about your business despite uncertainty
- 10 challenges facing the manufacturing industry in 2025
- Optimizing production of high-precision components through collaboration
- An inside look at the defense maritime industrial base
- Why manufacturing, intralogistics companies need to embrace the cloud
- February 2025 US cutting tool orders total $198.6 million
- The Smoothest Surfaces For Your Toughest Materials