
The global medical devices market size was valued at $640.45 billion in 2024, and Precedence Research calculates it to reach $678.88 billion this year, with projections to near $1.147 trillion by 2034, growing at a compound annual growth rate (CAGR) of 6% during the forecast period. When looking at just North America, the medical devices market size reached $256.18 billion in 2024 and is expanding at a CAGR of 6.05% through 2034. When narrowing in on just the U.S., its medical devices market size was estimated at $180.02 billion in 2024 and is predicted to be worth around $328.65 billion by 2034, a CAGR of 6.2%.
While the U.S. shows the most CAGR through 2034 – due to an aging population, increases in chronic diseases, and accessibility to medical treatment – emerging markets are becoming key growth drivers, offering new opportunities for device companies.
In addition to emerging markets offering industry expansion, key industry trends will continue to lead the way in medtech such as digital technologies. Machine learning (ML) and artificial intelligence (AI) are used to enhance diagnostics, increase surgical precision, and improve patient care. Additionally, ML algorithms are being implemented to enhance surgical results when performing minimally invasive and robotic assisted surgeries. This increase in the use of AI and ML within medical devices and procedures requires medtech manufacturers to adhere to additional FDA and EU regulations since digital health software is involved.

A challenge remaining for medtech manufacturers is supply chain struggles. While much has eased in the past few years, companies continue to look to diversify suppliers, ensure inventory is sufficient, and – with possible tariffs soon – look to reshore or near-shore to avoid increases in raw materials and/or finished devices.
For the “2025 Life Sciences Outlook” the Deloitte U.S. Center for Health Solutions surveyed 150 C-suite executives from pharmaceutical, biotechnology, biosimilar, and medical device manufacturing companies across the United States, Europe (France, Germany, Switzerland, and the United Kingdom), and Asia (China and Japan) to learn about the industry’s concerns and priorities. Their findings show digital transformation is the likely driver of more changes this year. As the report notes, “Digital transformation remains a key focus in the life sciences industry, driven by advancements in cloud computing, generative AI, and other digital technologies. These innovations provide companies with new opportunities to enhance their products, services, operations, and strategic decision-making.”

Another area the Deloitte report notes is how evolving customer expectations could influence life sciences companies’ strategies as they navigate “increasingly complex relationships among a wide range of customers including consumers, hospitals, health systems, and healthcare professionals, whose needs, incentives, and expectations diverge.” This complex relationship is also leading consumers to change. The authors note that while health care professionals (HCPs) can be important influencers for health care consumers, many consumers are increasingly acting as CEOs of their health with some turning to gen AI when making decisions about their healthcare. Consumers are also becoming more selective about their HCPs, and often demand increased personalization of therapeutics, frictionless support services, and technologies.
While medtech remains a necessity throughout a lifetime, technology continues to keep the market changing and advancing while one thing remains – steady growth year after year.
Read on to learn insights from throughout the industry regarding the state of medical devices manufacturing and what these thought leaders see for 2025.
Cris Taylor,
President & CEO, INDEX

OF RESPECTIVE
COMPANIES
Mergers and acquisitions (M&A) continue to be a dominant factor in the health and growth of the medical manufacturing segment. During the past year, we have continued to see a significant number of these realignments internationally and domestically. In some instances, production has continued with very little impact at specific sites. In others, there’s been a push to identify and standardize best practices across geographically divergent facilities.
As medical companies have increased in size, the cost-benefit analysis of updating production processes has shifted. Whether a company’s producing parts internally or outsourcing them, larger part quantities change the math on when the benefits of implementing an improved production process outweigh the time and monetary costs of obtaining certification for it. Generally, the larger the company, the greater the upside to modernizing processes, so continued M&A likely bode well for providers of advanced manufacturing technologies.
The evolving nature of the operating room also portends significant changes for medical manufacturing. A rapidly expanding variety of AI-driven tools are being implemented to assist surgeons with a range of procedures. While some of these innovations represent software-driven, iterative enhancements to existing devices, others are bringing entirely new hardware into the operating room (OR). Industry-specific regulations will constrain the rate of integration of some of these devices, but many will eventually become standard, creating new demand for high-technology products capable of performing in a sterile environment.
During the next year, one of the greatest unknowns will be the execution of the new administration’s promised scaling back of government entities and regulations. This push for less bureaucracy could prove to be very positive if it results in more efficient processes. On the flip side, simply reducing headcounts within agencies to minimize costs could push things in the other direction. For example, a streamlined U.S. FDA approval process would enable medical manufacturers to more frequently improve product designs and production methods, while a standalone reduction in the number of FDA employees would encourage the opposite. As with all changes in government, medical manufacturers will do well to pay close attention to actions taken and the markets’ response to them. https://www.index-group.com
Steve Baier,
CSO and VP of Sales, HAIMER USA

Medical manufacturers are heavily involved in the high production of medical implants, which requires precision, efficiency, and consistency. Many of the materials machined, such as titanium, are tough on cutting tools, leading to accelerated wear. Short cutting tool life results in frequent tool changes, disrupting production schedules and increasing costs.
To address these challenges, medical implant manufacturers are increasingly turning to advanced tool management software providing a centralized solution for tracking and managing tool holder assemblies across all machine tools. By integrating tool life management capabilities, manufacturers can accurately predict when a tool change is needed, minimizing unexpected downtime and ensuring uninterrupted production.
WinTool from HAIMER is designed specifically to help manufacturers digitize and optimize machining operations while the software’s data-driven approach enables manufacturers to make informed decisions about inventory and tool purchases.
The implementation of tool management solutions offers benefits including improved production speed, reduced waste, and lower operational costs. Manufacturers often uncover hidden profit opportunities by identifying previously unnoticed inefficiencies. In today’s competitive market, adopting these technologies is essential for maintaining profitability and delivering high-quality medical implants on time. https://www.haimer.com
Joe Wilker,
Advanced Multi-Tasking Manager, Mazak
& Jared Leick,
Product Manager, Mazak

Two medical manufacturing trends will dominate in 2025: increased use of automation and a transition to components made from near-net shaped castings and those produced with additive manufacturing (AM).
To lower price per part, reduce operator intervention, and increase process stability, medical manufacturers will require automation for 24/7 unattended production. This automation must ensure process consistency, improve quality, help lower overall costs, and reduce scrap while boosting manufacturing capacity and workforce output. Additionally, automation must provide flexibility to adapt to any production application, including high-mix/low-volume and high-production scenarios.
Production speed and increased output requirements will drive more medical manufacturers to machine implants and other medical devices from near-net shaped parts. Doing so reduces waste and production costs by minimizing the amount of material removed during machining. Because the parts often require only finish machining passes to bring them to size, medical shops can eliminate roughing operations for faster production and run jobs at higher spindle speeds/feed rates.
Working from near-net shaped parts also means medical shops will continue to gravitate toward machine tools with higher speed spindles – those in the 20,000rpm range – and with full simultaneous 5-axis capability to access part features during finishing and provide smooth finishes on complex contoured surfaces.
Instead of interrupting production to turn or re-clamp a part during machining, a 5-axis machine allows medical shops to program the machine’s table to tilt or rotate for part feature access while gaining the benefit of error-free, consistent machine-controlled movement. These setup-time improvements alone contribute to much shorter lead times and increased repeatability preventing damaged or scrapped parts. https://mazak.com
Preben Hansen,
President, Platinum Tooling

The medtech industry has been very strong over the past few years and we believe it’ll only grow stronger in the coming years. Spending in the medical field is forecast to be one of the top areas for high-end machine tools and cutting tools.
Medical manufacturing is an area where investment in research and development is constant and always evolving. For example, medical technology continues to develop new products, such as wearable devices, and has allowed the progression of robots in the surgical environment. Additionally, items such as surgical tools, diagnostic equipment, implants, and medical device components are continually being improved.
As a result of these efforts, new machining processes need to be developed, translating into new machine tool purchases plus accessories to complement these machines. Many medical components are getting smaller, even micro, presenting challenges in workholding, toolholding, and required rpm. The highest standard for accuracy and consistency is essential in the medtech industry.
As a company, our focus is to provide precision machine tool accessories to address these stringent requirements. Tools for high-speed machining, such as speed multipliers, ensure cutting tools achieve optimal performance. Additionally, we provide solutions to achieve the highest accuracy in workholding and toolholding. Specialty products, with a runout accuracy under 2µm, are used extensively in medical manufacturing. Although accuracy is the most critical element, aesthetics also play an important role in the manufacturing process. High-precision tooling must be supplied to accomplish the proper finishes, including the correct knurl form used on many surgical instruments. https://platinumtooling.com/
Mike Moyer,
Vice President of Sales, Solar Atmospheres

Heat treating is a critical step in manufacturing many medical devices. These devices often incorporate metal parts where material properties must be optimized for specific service conditions. Heat treating is the most effective method to achieve this.
As medical device designs and technologies have advanced, so have the requirements for heat treating. These include precise furnace recipe control, bright finishes, minimal surface contamination, minimal distortion, and cost efficiency.
The most significant advancements in heat treating technology have been made in vacuum furnace systems. These systems lead the industry with innovative control systems, deeper vacuum levels, lower residual gas levels in furnace atmospheres, and improved efficiency.
Whether the material is 17-7PH, 300-series stainless steel, or titanium, today’s modern vacuum furnace systems are equipped to handle the task. Advanced control systems enable the achievement of technically challenging results, enhancing material properties. Innovative furnace designs minimize residual water vapor and other gases, reducing discoloration and surface contamination risks. Gas quenching, used in place of liquid quenching, further reduces surface contamination and distortion.
With these advancements, vacuum furnace systems are now more efficient and reliable, consuming less electricity while minimizing downtime and controlling costs. The implementation of MedAccred, a third-party, process-based accreditation by the Performance Review Institute (PRI), allows medical device manufacturers to confidently outsource to heat treat companies demonstrating excellence in quality systems and manufacturing capabilities.
Plato is often paraphrased as saying, “Necessity is the mother of invention.” Medical devices have come a long way since their inception, and heat-treating technology is no exception. What once was an art has evolved into a precise science, continually improving and advancing to meet the needs of modern industries. https://solaratm.com/
Rick Schultz,
Aerospace and 5-axis Program Manager, FANUC America

For 2025, there are tremendous opportunities for using the latest CNCs and related technology to service the changing medical device and equipment industry. With more customized joint replacements that fit the patient’s body more precisely, a retooling of medical device production is now becoming necessary.
Because the industry is moving away from using generic joint replacements, where a patient’s bone structure was altered to suit the device, and moving toward using custom replacement joints via scanning technology, medical device producers must also change their manufacturing operations. The process must now entail additive manufacturing (AM), CNC machining, and accurate CNC part programming to adjust to this custom joint replacement.
Importance of CNCs in AM – AM has been a game changer for the medical device production industry. Effectively producing highly engineered metal components through processes such as laser powder bed fusion (LPBF) on metal additive machines has been fundamental to fuel medical device replacement production and procedure advances.
However, more than just 3D printing is necessary to make the production process successful. CNC machining is still important for achieving tight tolerances, necessary polished surface finishes, and accuracy needed for customized metal joints. The key to this hybrid approach is using the new CNC technology and solutions available.
Machine tools with powerful controls with advanced functions for optimal 5-axis tool paths can help medical device producers get the most out of 5-axis machining. While it’s possible to do the required 5-axis machining with legacy controls or functions, the workflow is significantly simplified with modern CNC functionality.
CAM programming and the CNC – An integrated software solution for CAM programming and machine controls must be in place before any advanced CNC machining can occur. The CAM system determines the required tool path and approximates it with a sequence of points. The post processor translates those points to a specific machine and CNC application. Tools helping set up posts for optimal functionality can simplify this process. For instance, FANUC’s advanced functions like Workpiece Setting Error Compensation (G54.4) and Tool Center Point (G43.4/G43.5) can eliminate complex math from post processors and create machine-independent part programs. Thereby programming parts, not machines, the same part can be run on multiple machines, even those with mechanical differences.
Additionally, FANUC’s CNC Guide 2 and Surface Estimation Tool replicates real-world surface finish results in digital simulations to accurately check part shape and machining quality level. Prior to any real-world cutting, the software precisely estimates a part’s machined surface by using the position data of each axis then simulating the cutting to detect machining issues. Knowing this before cutting helps avoid wasting valuable time and materials produced with marks or other surface defects.
Key takeaways – The outlook for medical device production in 2025 is exciting with technological advancements coming together creating phenomenal industry changes. However, CNC machining is still as important to medical device production as it was years ago. Keeping up with the latest CNC technology and CAM solutions promises to be even more important going forward. https://www.fanucamerica.com/
Adam Hesse,
CEO, Full Spectrum

In 2025, the medtech landscape will be shaped by a wave of deregulation, driven in part by figures such as Elon Musk and the influence of the Right to Try law. This uncertainty may create new opportunities for disruption and innovation, but it also raises critical questions about the regulations enforced by the U.S. FDA, especially amid the possibility of funding cuts and personnel reductions. While lower bandwidth may streamline guidelines, cybersecurity and liability risks remain as crucial as ever – deregulation doesn’t eliminate accountability in healthcare.
In 2025, artificial intelligence (AI) will be essential to staying competitive in the medical device sector, enhancing the devices themselves and shaping their development processes. The trend is already clear, with FDA approvals for AI-related products rising significantly, from 650 devices in 2023 to 950 in 2024. As the hype cycle settles, focus will shift to real-world adaptation and the competitive edge AI provides in product and development.
In 2025, R&D investments in medical devices will accelerate as companies recognize delaying innovation could mean falling behind. Following a cycle of financial slowdown and layoffs, we’re about to see an uptick in R&D, fueled by a resurgence in medtech profitability. This renewed focus on R&D will be key to staying competitive. https://fullspectrumsoftware.com/
Mikhail Boukhny,
Senior Vice President of Research and Development, BVI Medical

As a seasoned expert in surgical ophthalmology advancements, I’ve witnessed technology transform patient care – and the pace of innovation is only accelerating. Entering 2025, artificial intelligence (AI) and enhanced surgical materials are redefining the field, enabling safer, more precise procedures while expanding accessibility worldwide.
AI: The new surgical partner – AI promises to be an active and rapidly evolving force in operating rooms (ORs). These tools can learn from previous procedures, provide real-time insights, and tailor workflows to each surgeon’s unique style, if the information is captured accurately. By streamlining preoperative planning and assisting intraoperatively, AI will enhance precision and reduce variability.
Although wide adoption of fully autonomous surgeries is probably 5 to 10 years away, AI will serve as a trusted co-pilot in the foreseeable future to enable surgeons to focus on the most critical aspects of their work while reducing errors. Moreover, integrating AI into OR systems can alleviate staff workloads, facilitate learning and speed turnovers, and increase efficiency in healthcare facilities.
Surgical devices: Versatility meets innovation – The tools and instruments surgeons rely on are evolving to meet new demands. Multifunctional devices, such as those combining cataract and vitreoretinal treatments in a single procedure, are reshaping ophthalmology.
Yet, the challenge lies in balancing cutting-edge technology with accessibility and affordability. Rising regulatory costs, and at best static reimbursement rates, demand smarter innovation. At BVI Medical, we’re addressing this with practical, impactful solutions such as our Endoscopic Cyclophotocoagulation (ECP) line for glaucoma treatment; laser microendoscopy offers the unique opportunity to view inside the eye and simultaneously treat anterior and posterior applications.
The road ahead – Innovation in surgery doesn’t happen in isolation. Collaboration among tech pioneers, medical device manufacturers, and healthcare providers drives the development of tools integrating seamlessly into surgical workflows.
As we look toward the future, AI-driven tools and enhanced devices will continue transforming surgery into a safer, faster, and more precise practice. The best is yet to come. https://www.bvimedical.com
Scott Lewis,
Turning Product Specialist, Sandvik Coromant

In the precision-centric world of medtech manufacturing, cutting tools are pivotal, facing exacting demands for reliability and consistent performance. Reliable and consistent tools drive innovation, sustainability, and efficiency, far beyond the cutting room.
Process security is crucial, as unpredictability costs more than money – it disrupts production and affects patient care. Tools must offer predictable and stable performance.
Surface integrity is also critical. High-quality finishes and minimal material damage during machining require sharp, precise tools tailored for specific materials such as medical-grade titanium and cobalt chrome.
Efficiency advancements lead to increased adoption of lights-out production, necessitating exceptionally reliable tools for unattended operations. These tools must be swiftly changed and set up to ensure continuous operation.
In high-volume medical shops, reducing the width of part-off inserts even slightly can lead to significant material savings over time, particularly as materials such as titanium are more expensive than steel.
Moreover, the partnership and support from tooling companies are as crucial as the tool’s performance. Such support bolsters customers’ confidence in managing their operations effectively.
Medtech manufacturing presents unique challenges where cutting tool suppliers must continually innovate and adapt. By providing tools that ensure process security, superior surface integrity, and adaptability to new materials, suppliers become vital partners in advancing the sector’s capabilities. https://www.sandvik.coromant.com
Kurt Ranka,
Managing Principal, Ducker Carlisle
& Jared Tate,
Managing Director, Ducker Carlisle

Feeling like you’re walking a tightrope with pricing strategies? You’re not alone.
Original equipment manufacturers (OEMs) in the medical device industry face myriad challenges when devising pricing strategies. From fluctuations in input costs such as labor and raw materials, to supply chain disruptions, customer and market sentiments, and insurance and regulatory hurdles, OEMs are encountering numerous obstacles nowadays.
With the economy gradually recovering from the pandemic-induced disruptions and near record inflation, OEMs are now facing the added challenge of responding to customer expectations for lower prices due to cooling inflation. Consumer psychology plays a role, and a common misconception is as inflation rates come down, prices come down. This may not be the case as cooling inflation means prices are still rising but at a lower rate than before.
Amid these developments, traditional pricing approaches may no longer suffice. Employing broad, scattershot pricing tactics, basic supply and demand strategies, and compliance with financial targets may pose risks as they often overlook market and product dynamics and fail to optimize pricing effectively. This approach may lead to overpricing some products while underpricing others, potentially alienating price-sensitive customers and impacting the company’s bottom line. Recent political discussions in the news cycle may imply an added threat of exposure to price gouging lawsuits.

A more agile and flexible pricing strategy is crucial, one accounting for market dynamics and your product’s value drivers while ensuring revenue creation and profitability.
Caught in the middle – OEMs are getting squeezed from suppliers, channel partners such as distributors and dealers, and end customers, in addition to the potential threat of price gouging lawsuits from legal entities.
OEMs in the medical device industry find themselves under pressure from various fronts – uncertainty in the outlook for reimbursements and government funding based on a potential change in administrations, continued low admission and elective surgery rates compressing provider budgets, interest rates remaining elevated compared to pre-COVID-19 levels impacting providers’ willingness to make investments, pressure to contain costs and show profitable growth, higher input costs of select raw materials and labor, fluctuating commodity prices, and customer demands for lower prices. The aftermath of COVID-19 continues to impact the medical device industry.
This dynamic of being caught in the middle isn’t unique to the medical device industry. Manufacturers nationwide are being pressured on one side by customers who want price reductions or stabilization, and on the other by high costs due to labor and commodity prices and high-interest rates.
Performance analysis: Impact of market- and value-based pricing – Through the application of a more advanced price strategy, many OEMs have observed typical benefits of increased incremental revenue of 5% to 10%, varying by industry and organizational maturity in implementing market- and value-based pricing strategies. In addition, other key benefits of the pricing strategy are no negative impact on customer pay quantities and addressing over-priced product/SKUs that negatively impact brand perception.
For example, a global medical device manufacturer sought to enhance its pricing strategy to better reflect the value of its innovative products and capture greater revenue potential. By incorporating competitive market data, detailed product attribute analysis (e.g., device functionality, durability, patient outcomes, and regulatory certifications), and understanding the key value drivers such as ease of use, clinical effectiveness, and brand reputation, the company shifted to a market- and value-based pricing approach.
Through this transformation, the medical device firm achieved a 5% improvement in revenue across its product portfolio. In addition, the company’s sales teams received specialized negotiation training to better communicate value to procurement groups.
The bottom line – Navigating the complexities of getting better pricing including understanding product value drivers and competitive and market insights can be time-consuming and daunting, potentially leading OEMs to retain the status quo. However, there’s an alternative approach: collaborating with an expert partner experienced in market- and value-based pricing strategies can facilitate the acceleration of additional revenue. https://www.duckercarlisle.com/
Dr. Stuart Grant,
Principal Consultant, Archetype Medical
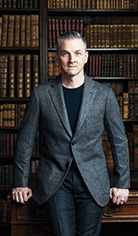
As we look ahead to 2025, several key trends and developments are poised to shape the medtech landscape. I believe one of the most significant changes will be a surge in venture capital investment, providing a much-needed boost for medtech product innovation. This cash injection will hopefully accelerate the development of cutting-edge technologies and solutions.
On the compliance side, companies will also be preparing for the new FDA Quality Management System Regulation (QMSR), set to take effect in February 2026. This is likely to be disruptive to companies that don’t already comply to ISO 13485 and the preparation phase will involve rigorous adjustments to ensure compliance, impacting operational strategies and quality assurance processes.
In terms of technology, the initial rush to integrate AI into every conceivable application is cresting. In 2025, I genuinely believe we will see a more measured approach, with a focus on evaluating AI solutions based on genuine clinical needs. Hopefully, this positive shift will ensure that these technologies deliver meaningful improvements in patient care.
Another trend to watch is the development of smaller, more versatile surgical robotic systems. These compact devices look set to enhance surgical precision and accessibility, making advanced robotic surgery feasible in a wider range of clinical settings. Additionally, extended reality (XR) technologies, including virtual reality (VR), augmented reality (AR), and mixed reality (MR), will further enhance robotic systems. These advancements will improve surgical training, planning, and execution, offering immersive and interactive experiences.
In the UK, there will be growing recognition that current MDR and NHS regulations may be stifling innovation and delaying patient access to new treatments. This realisation could – and should – drive a shift towards more flexible, FDA-style regulatory frameworks, fostering a more conducive environment for medtech advancements. Overall, 2025 promises to be a dynamic year filled with opportunities for innovation and growth in the medtech sector.
https://archetype-medtech.com/

Explore the January/February 2025 Issue
Check out more from this issue and find your next story to read.
Latest from Today's Medical Developments
- Unlocking GenAI's potential: Insights from the Supply Chain Horizons 2025 report
- Celebrating 75 years of innovation at Jorgensen Conveyor and Filtration Solutions
- Free webinar to offer expert advice on optimizing machining operations
- How collaboration between companies can elevate manufacturing
- AI meets innovation: Cambridge's device transforms heart screening
- Mazak and Premier Engineering team up for greater agility in Florida
- Struggling with inventory or supply chain pressures? Find answers in our free webinar
- Free webinar: Advanced manufacturing solutions to support the Navy