Headless Bolt, Simple Ball-Lock Mechanism
The Loc-Jaw System for fourth and fifth axis machining is a design requiring no material preparation. Serration of the rails and gripper towers provide a solid and easily adjustable clamping range of 0.5" to 4.0". The low profile grippers hold on only 0.100", allowing full access to all work surfaces including the bottom face. Design of the base is to adapt, easily, to most machine tables with a precision bore provided for a centering disk. A single support bolt reinforces the gripper towers for rigidity and increased workholding capacity.
Described as a headless bolt with a simple ball-lock mechanism, the Loc-Down’s design is for quick locating of parts for high speed machining applications. The Loc-Down System can also be a simple low cost solution for quick-changing fixtures on tombstones and pallet changers. The Loc-Down System is very user friendly, requiring only a drilled and tapped hole (½-13 or M12) in the base plate and a drilled hole with an internal groove machined on the workpiece. Custom bushings are be available for mounting fixture plates. Loc-Down saves the time required to remove, completely, a hold down bolt with less tooling interference.
Mitee-Bite Products LLC
Center Ossipee, NH
www.miteebite.com
Next Generation MTM Capabilities
Always focusing on programming parts quickly, accurately, and efficiently, the next generation of GibbsCAM’s MTM (Multi-Task Machining) solution helps users implement the full capabilities of complex MTM machines, including 5-axis rotary head and Swiss-style machines. MTM machines pose special challenges to users, including programming machines with multiple spindles and turrets cutting multiple parts simultaneously. GibbsCAM’s signature, easy-to-learn and use interface walks customers through such complex part programming. Enhanced graphics enable users to see an accurate simulation of the part requiring machining, providing full visualization of errors like tool interference and gouges long before the part gets to the shop floor, preventing costly mistakes.
The design of GibbsCAM MTM is specifically to address the CNC programming requirements of multi-task machine tools, providing powerful programming tools that are easy to learn and use with ultimate flexibility and configurability. Defining of the machining processes is easy with GibbsCAM's intuitive GUI, which provides seamless access to both turning and milling capabilities. GibbsCAM's associativity allows updating, easily, of operations, when modifications occur.
Multi-task machine tools now incorporate substantial live tooling support, enabling milling operations that are more extensive. GibbsCAM MTM can combine with any of the GibbsCAM milling options to support a multi-task machine tool’s complete range of milling operations.
Similar to other types of multi-task tools, Swiss-style machine tools represent some of the most complex MTM configurations available. GibbsCAM MTM supports Swiss-style multi-task machine tools and provides an easy-to-use tool for programming these complex devices.
Gibbs and Associates
Moorpark, CA
www.gibbscam.com
Achieve Maximum Torque in Minimum Space
The newest addition to the maxon family of motion control products are the 22mm and 32mm right angle gear heads. Development of these compact, lightweight, and high torque gear heads provides an adjustable 360° right angle output for the most demanding applications.
The 22mm and 32mm right angle gear heads are available in either a 4:1 or 31:1 ratio, which can mount directly onto many of maxon’s brushed/brushless motors or stack on different ratios of maxon’s GP22 and GP32 planetary gear heads. This results in a wide range of achievable gear reductions. The motor and gear head combinations are ideally suited for a variety of applications, particularly where an output shaft needs to be perpendicular to the rotor axis.
The Spiroid technology incorporated in the gear head design offers a number of performance benefits:
- Extremely high torque transmission
- High stiffness / low deflection with large applied loads
- Back-drivable (4:1 ratio) and non-back drivable (31:1 ratio) versions
- Absolute output shaft position achievable with encoder mounting option
- Compact size
- Output shaft can orientate 360° at any time
- Low backlash
- Up to 3:1 contact ratio, and
- Quiet operation.
maxon precision motors inc.
Fall River, MA
www.maxonmotorusa.com
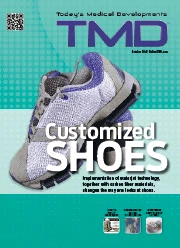
Explore the October 2012 Issue
Check out more from this issue and find your next story to read.
Latest from Today's Medical Developments
- Betacom, Siemens launch 5G network platform to accelerate manufacturing innovation
- Starrett’s AVR400 CNC vision system
- US cutting tools orders decreased 2% from November 2024
- SMW Autoblok's Manual Jack connection kit
- MedTech Innovator welcomes five new industry partners
- First Article Inspection for quality control
- The manufacturing resurgence is here – are you ready?
- Workholding solutions for your business