![]() producing titanium medical parts – two mating parts for a two-piece connector for a kidney dialysis system. |
Established in 1972, family-owned Advance Turning and Manufacturing, Jackson, MI, has seen a lot change in the job shop industry. Then, competition was more local; today, the 150-person AS9100:2009 (Rev C) and ISO 9001:2008-certified company finds it is competing with shops from just about anywhere in the world. Its work is evenly split between aerospace parts, such as hydraulic fittings, and medical components, such as parts for powered surgical instruments, heart and lung by-pass equipment, and dialysis systems of titanium, stainless steel, and plastic. In the shop’s CAD files there are about 8,000 active part numbers, 85% of which is bar feed work.
“For most of what we do, we work at how to make changeovers seamless and smooth, how to go from part A to part B most quickly,” states Frank Lusebrink Jr., vice president, Advance Turning and Manufacturing. “With short runs, we may spend more time setting up than cutting it. That is a lot different approach than you have with high volume continuous manufacturing.”
The company is finding it has an advantage for longer run, higher efficiency, high-precision work, such as medical parts involve. To do that kind of work, Advance engineers discovered that EMCO Maier, Novi, MI, had a turnkey solution that fit very well. Advance learned of EMCO Maier at IMTS while looking for an economical way to produce large volumes of small plastic parts.
“We were doing a plastic part on a cell made up of two traditional lathes and a mill and struggling with quality issues due to the multiple setups. We saw the EMCOTurn 420 dual CNC lathe at an IMTS a few years ago and decided to buy it off the show floor,” Lusebrink says.
“When we saw it, we knew our application was just right for it,” Lusebrink states. “We had not seen too many machines like this, and we had checked out many machines.”
So far, the machine has had a good run at Advance, turning out more than 1.25 million parts since installation. The machine holds tolerance extremely well, and once it is up and running, it will run for hours and hours no problem, Lusebrink reports.
The EMCOTurn 420 is a 25mm bar capacity, dual CNC lathe for simultaneous complete machining of two parts. It is designed with two main and two opposing counter-spindles, each with C-axis positioning, and two 12-position tool turrets (top and bottom) carrying VDI quick-change pre-settable toolholders which are paired with a main and counter-spindle. Up to four tools in each turret can be driven. Each subsystem has its own parts catcher to match parts with measurement data. It is really two machines on one base, and easy to operate as a conventional CNC lathe as it is controlled by an easy-to-use Siemens 840D CNC.
![]() |
Keeping up with Changes
The plastic part the EMCOTurn was originally purchased to produced is moving on, so Advance is in the process of re-tasking its now three EMCOTurns (having subsequently purchased two EMCOTurn 420 machines) with a couple of medical parts made of titanium. The company knew how well the machines did with the plastic part, but was unfamiliar with their capability in metals. The staff at Advance Turning was pleasantly surprised.
Advance now has three EMCOTurns producing titanium medical parts, and mating parts for a two-piece connector for a kidney dialysis system. One of the CP2 titanium parts has a belly-shape within its ID.
“As we repurposed EMCOs for the titanium parts, which we have been doing on a single spindle machine, we found that they do the same quality, same production, in one-third less time. We previously would have put the parts through a cell of turning machines and a mill, but the EMCOs do the parts in one setup, one machine. Tolerances are about 0.002" with a 6cpk to 8cpk. The EMCO’s are plenty tough enough to machine the titanium,” Lusebrink states.
For the titanium parts, each turret is setup identically, 11 tools in each 12-position turret with one of the stations carrying a dual toolholder. The two pairs of spindles operate identically.
“There is a lot more to the EMCOs than we thought. The dual-spindle, dual-turret means that within one cycle we are dropping two parts,” Lusebrink says. “From a floor space and efficiency standpoint, we love these machines.
“With two turrets in each EMCOTurn, we are getting more production out of them than we can with our other multi-machine cells. Other cells at Advance may changeover five to six times a day with attendant downtime for the changes; but we use the EMCOs’ very successfully for longer runs of high value parts,” Lusebrink claims.
The automatic part exchange between spindles and an automatic part catcher makes it possible to complete two parts at a time in a single cycle so the machines are assigned parts with a longer run, which for the company is about 5,000 to 6,000 pieces per month.
“Most of Advance’s processes are designed for flexibility, not production efficiency, such as you would want on higher volume jobs,” Lusebrink says. “So we go after applications where we can be the best at lowering the cost of parts to our customers while providing top quality. Focusing on longer runs will allow us to optimize the best process.”
The EMCO’s are fitting into this strategy very well – you might say they are powering it at Advance.
![]() |
The EMCO Maier Philosophy Salzburg, Austria-based EMCO is one of Europe’s leading machine tool manufacturers. Its two commitments – “Made in the Heart of Europe” and “Design to Cost” – are the main factors in the success of the international company, which represents excellent production quality and functional design. |
Mass Production
Set up as a turnkey for the plastic parts originally, the operators at Advance did not really have to learn the control. But with the change to a different range of parts, they needed to learn the Siemens CNC.
“At first the Siemens control was unfamiliar. Because the project was turnkeyed, we did not have to learn the CNC. When we moved the new parts to the EMCO’s, we had EMCO come back and give us a little training. The CNC is a blend between conversational and straight G-code. Plus we found out the control takes time out of the process because it acts faster than others,” says Bob Renfer, operations manager, medical part production.
“The control is simple once you learn the macros,” Renfer says. “Once you program a feature, you do not have to program it again. Once you recall the name, that part of the program can be added to the process. That saves us a lot of time. I am very comfortable with the control and feel I can handle any part that fits within the working area.”
“When we decided to move the part to the EMCO there was a little trepidation, but we are now very comfortable with it,” Lusebrink says. “Like most shops, we do not always take enough time to take a look around to see what is new and improved in manufacturing technology. But, learning the capabilities of the EMCO has really helped our operation. It is great having the support of EMCO to help us use the technology to stay ahead.
“Going forward, we are looking for runs that make sense on the EMCOs. We feel they will be very important to us in the future as we find more high-value work to run through them,” Lusebrink concludes.
EMCO Maier Corp.
Novi, MI
www.emcomaier-usa.com
Advance Turning & Manufacturing Inc.
Jackson, MI
www.advanceturning.com
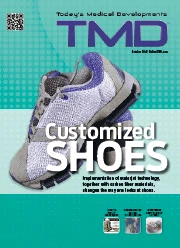
Explore the October 2012 Issue
Check out more from this issue and find your next story to read.
Latest from Today's Medical Developments
- Montagu to merge Tyber Medical, Intech and Resolve Surgical Technologies
- Americhem’s EcoLube MD PFAS-free internally lubricated compounds
- German robotics and automation in a downturn
- Blueshift’s AeroZero
- November USMTO grow from October
- Platinum Tooling’s custom and special tooling
- Top 5 global robotics trends 2025
- Accumold’s micro molding innovations