For years, carbon fiber has brought amazing strength-to-weight ratio to the aerospace and automotive industries. Today, however, this valuable composite material is becoming increasingly common in the production of consumer goods thanks to improved, more cost-effective manufacturing techniques. Most recently, carbon fiber has become the heart and literally the sole of OESH shoes, possibly the world’s most comfortable footwear.
OESH shoes, the brainchild of Dr. D. Casey Kerrigan, a Harvard University-trained physical rehabilitation doctor with additional training in mechanical engineering and biomechanics, use a series of patented, tight U-shaped carbon fiber cantilevers oriented in the midsole that are specifically designed to reduce foot and leg injuries.
These carbon fiber cantilevers enable each OESH midsole to flex and release, similar to a diving board, at exactly the right time – not at the moment of impact, but when the foot is fully planted and, in tune with the rise and fall of the peak forces throughout the body.
Traditional athletic and comfort shoe midsoles consist of foams, gels, or air-filled bladders, making them less effective than OESH as they do not properly compress and release with a person’s movements. Furthermore, midsoles made of foam begin to wear down very quickly, while the carbon fiber cantilevers effectively respond to a person’s body weight, stride after stride for more than a million cycles, without even beginning to fatigue.
![]() |
According to Kerrigan, who has spent more than 20 years studying gait, shoe comfort is all about creating true compliance under the foot and following a foot’s natural position, which are both achievable with the carbon fiber cantilevers. “Most shoe designs try to control or correct the foot, and that can actually do more harm than good,” she notes.
While her research and medical training led to the OESH concept, her engineering skills gave her the knowledge to design and build some of the equipment that helps make the revolutionary carbon fiber cantilevers. However, she considers her Maxiem 1515 JetCutting Center from Omax Corp., the crown jewel of her manufacturing process, as it accurately cuts each of the carbon fiber cantilevers, eliminating the need for secondary machining.
Kerrigan and her husband, Robert Kusyk, took the word shoe and turned it upside down and inside out to create the OESH name, and launched the shoe line from their small factory in Charlottesville, VA, in 2010. Online sales of their shoes began in December of that same year, and they immediately found themselves swamped with thousands of orders from women who were tired of their legs and feet hurting.
Today, with sales surging, OESH footwear continues to sell exclusively through www.OESHshoes.com, allowing the company to communicate, directly, with its customers all over the world.
“It currently requires all we can do to keep up with our online demand,” Kerrigan states.
However, to maintain a strong grass roots message, the OESH factory is open to the Charlottesville community on Mondays, Wednesdays, and Fridays, from 11am to 2pm, so Kerrigan and her staff can talk with customers, one by one, as they fill local orders.
As of now, OESH only makes all-purpose trainer shoes and sandals for women, priced at approximately $195 a pair, but the company plans to enter the male shoe market within the next year or so. Because each shoe size requires a separate mold, and they are expensive, it will take OESH some time before a full range of sizes for both genders are available.
Kerrigan wanted to start with women’s shoes because females have twice as many musculoskeletal problems as males. In addition, her research, highlighted on the television program 20/20, shows a link between high heel shoes and knee arthritis.
“Women have always had the poorest choices in comfortable shoes; therefore, I felt it was my responsibility to cater to them first,” Kerrigan notes.
OESH currently has the capacity to make approximately 300 shoes per day. Manufacturing of the carbon fiber cantilevers – the most complex parts of each shoe – occurs at the OESH factory. Manufacturers in China make the soles and linings of the shoes, shipping the parts to the Virginia plant where full assembly takes place. Because OSEH is located near the University of Virginia, where Kerrigan is a former chair, college students often make up the majority of her employees. According to Kerrigan, her goal is to one day have OESH shoes 100% American made.
OESH’s carbon fiber cantilever manufacturing process begins with filament winding where a specified amount of carbon fiber and a specified amount of resin spends 20 minutes wrapping around a mandrel to gain inside shape. OESH has several mandrels running simultaneously, and each mandrel supplies enough carbon fiber material to support up to 14 pairs of shoes, depending on shoe size, of course.
After winding the material, each mandrel goes to an oven press where it gains its outside shape. A regular pizza oven then bakes the carbon fiber material until fully cured. Next, the mandrels make their way to the Maxiem 1515 JetCutting Center that applies 50,000psi direct drive pump technology to cut the cantilevers. Kerrigan enjoys the quick turnaround of the cantilevers because with the Maxiem 1515, there is not the hassle of tool changes or complex fixturing.
Engineered for optimal efficiency, the Omax-proven direct drive pump on the 1515 delivers more than 90% of the electrical input power to the cutting nozzle, providing higher cutting speeds than other pumps with the same size electric motor and power consumption.
“If you are going to cut a lot of carbon fiber, you do not want to use a saw because that produces a lot of unwanted particle dust,” Kerrigan explains. “Waterjet machining is clean, safe, and efficient.”
![]() Top: Dr. D. Casey Kerrigan says that abrasive waterjet cutting on the company’s OMAX Maxiem machine provides clean accurate cutting of the carbon fiber material. Bottom: A completed carbon fiber cantilever assembly for OESH athletic shoes; this is what allows the effective response to a person’s body weight, stride after stride. |
Offering a small footprint of 8ft 9" x 8ft 2", the Maxiem 1515 fits nicely into the OESH facility and comes with an X-Y cutting travel of 5ft 2" x 5ft 2". The 1515 is also a highly robust solution for OESH because Omax uses coated steel covers to protect the machine’s advanced Intelli-TRAX linear drive technology.
Kerrigan can easily control the 1515’s jet stream while it is cutting, thanks to Omax’s Intelli-Max Standard Software Suite, which is the core functionality of Omax’s waterjet-specific control software. The software can calculate the precision of the velocity of a toolpath at more than 1,000 points per inch.
According to Sandra McLain, vice president of marketing for Omax Corp., the Intelli-Max control software enables the Maxiem 1515 to cut the highest tolerance parts in the fastest amount of time, at a lower cost than any other industry standard abrasive waterjet machine.
“When I was researching waterjet machines, I was amazed at how expensive they can be,” Kerrigan says. “I made the right choice with the Maxiem 1515 because it gives me exactly what I need at a very fair price. Plus, Omax representatives are always ready to help me if I need it.”
After cutting of the carbon fiber cantilevers by the Maxiem, they go into a top-loading washer in order to smooth out the edges. The manufacturing process ends in a dishwasher where proper cleaning of the cantilevers occurs prior to going into the midsoles of the OESH shoes.
OESH definitely has a unique product and many happy customers – just look at the testimonials on oeshshoes.com – but Kerrigan likes to keep business more on the modest side. After all, she is a doctor by trade who believes in high quality, personal care, and she wants OESH to be a means of helping people one person at a time. While Kerrigan has no desire to become a mogul of the shoe industry, she is willing to add capacity to her factory, including a new Maxiem machine if need be, to give OESH fans more of what they want.
Omax Corp.
Kent, WA
www.omax.com
OESH Shoes
Charlottesville, VA
www.oeshshoes.com
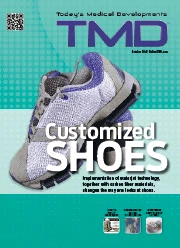
Explore the October 2012 Issue
Check out more from this issue and find your next story to read.
Latest from Today's Medical Developments
- Tariffs threaten small business growth, increase costs across industries
- Feed your brain on your lunch break at our upcoming Lunch + Learn!
- Robotics action plan for Europe
- Maximize your First Article Inspection efficiency and accuracy
- UPM Additive rebrands to UPM Advanced
- Master Bond’s LED415DC90Med dual-curable adhesive
- Minalex celebrates 60 years of excellence in miniature aluminum extrusions
- Tormach’s Chip Conveyor Kit for the 1500MX CNC Mill