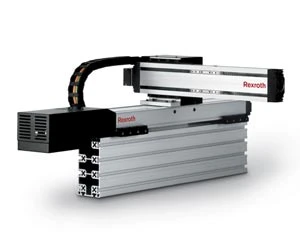
CMS Multiple Axis Motion Systems from Rexroth offer integrators and machine manufacturers a plug-and-play solution that has been precisely pre-configured to their specifications. This opportunity was grasped by special-purpose machinery manufacturer behr GmbH, who chose CMS motion systems to build an assembly line for medical equipment.
For Uwe Behr, the Managing Director of behr GmbH in Blaichach, Germany, this technology has many advantages to offer: "It is substantially less expensive than other solutions. And what is most important, Rexroth offers plug-and-play solutions with its CMS, which considerably cuts our project planning and start- up costs."
For a new assembly line designed for a medical technology application, behr used pre-configured multiple axis systems CMS from Rexroth. These one-, two- or three-axis solutions combine linear motion systems—based on Rexroth's proven Compact Module CKK—with motors, cables and servo drives, including the interfaces to all commonly used field bus systems. "This plant has been designed to automate the handling of optical lenses produced to order by a medical equipment manufacturer," says Markus Haberstock, Project Manager at behr. The challenge here was that the assembly system had to be planned and built to dovetail precision, with existing production facilities consisting of seven machines.
The work operations reflect the complex logistics required to manufacture using very small production runs. Three injection molding machines standing side by side produce eight parts in four different designs per cycle. These are die halves, which have the exact negative contours of precisely defined product variants. Pick-and-place systems position the dies, measuring 15mm in diameter in workpiece trays with 32 compartments. A conveyor system moves the filled workpiece trays to a transfer system from Rexroth for the next work step. There, four Cartesian motion systems slot the die pairs into towers – drum magazines with eight compartments for up to 100 dies each. In all, more than 300 storage cells are being used in the drum magazines.

Clean conveying: the assembly line with four Rexroth CMS multiple axis motion systems installed in a class 10,000 clean room.
"The CMS systems play a key role in sorting the dies," emphasizes Haberstock. What counts above all is high flexibility to cater to the many product variants. Rexroth supplies the four X-Y systems as complete units with motor and controller. In this application, the controllers communicate via Profibus with the master control system. The compact Rexroth Ecodrive Cs controllers and MSM motors offer high dynamics and achieve a very high positioning accuracy with their multiturn resolvers, generating 131,072 pulses per revolution.

Flexibility is key: the CMS sorts the die pairs prior to the next process step.
The behr systems have a useful stroke of 500mm in the X-axis, and 400mm in the Y-axis. The combined linear axes, based on the Compact Module CKK, were supplied in the lengths specified by the customer. The CKK modules consist of an extremely compact precision extruded aluminum profile with an aluminum cover plate. A continuous gap seal made of PU strip protects the internals. The CKK modules have two integrated ball rail systems. Large screw diameters and leads, and double floating bearings make it possible to combine high travel speed with high precision. The centrally arranged ball screw drive in tolerance grade 7 ensures a low-profile design, and with its zero-clearance nut system, delivers high positioning accuracies of up to 0.01mm, and a repeatability of up to 0.005mm per axis. The ball rail systems and the ball screw drive have one-point lubrication systems accessible from either side, thus minimizing maintenance. The aluminum fixed bearing block with two-row preloaded angular- contact ball bearings, and the floating bearing block with double ball bearings ensure backlash-free, dynamic motion. A locating feature and threaded mounting holes facilitate motor mounting. The perfectly matched motor/controller combinations achieve speeds of up to 1.0m/s and acceleration rates of up to 15m/s2, which assures a high level of efficiency and productivity.
In the behr assembly line, the CMS systems run in concert with a further servo axis for the tower. The machine frame is constructed from tubular steel. Aluminum profiles and guard elements were also provided by Rexroth. The multi-technology specialist supplies CMS motion systems complete with matching clamping fixtures and connecting plates for mounting to the aluminum profile struts from the basic mechanical elements range. This saves even more time.

Explore the April 2007 Issue
Check out more from this issue and find your next story to read.
Latest from Today's Medical Developments
- Tariffs threaten small business growth, increase costs across industries
- Feed your brain on your lunch break at our upcoming Lunch + Learn!
- Robotics action plan for Europe
- Maximize your First Article Inspection efficiency and accuracy
- UPM Additive rebrands to UPM Advanced
- Master Bond’s LED415DC90Med dual-curable adhesive
- Minalex celebrates 60 years of excellence in miniature aluminum extrusions
- Tormach’s Chip Conveyor Kit for the 1500MX CNC Mill