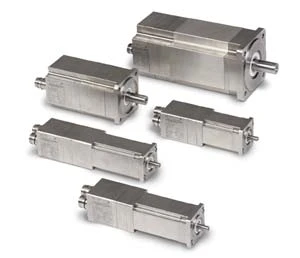
Today's medical equipment requires precise control and performance. Applications in this field call for rapid acceleration, accurate speed regulation, and pinpoint accuracy. Precise control improvements that have been accomplished up to now have been made possible with the application of servomotors, devices that continually contribute to technology advancements. Servomotors are used worldwide in applications which require smooth, precise control. These fea- Medical Equipment Improvements With Servos John Mazurkiewicz, Baldor Electric Ft Smith, AR tures are also associated with servos in a variety of medical equipment and applications. The servomotor is designed to provide precise control, and "performance," for example, drive a load and get it into position faster, smoother, and with more precision. Servomotors feature abilities like smoothly moving a patient into position, rapidly packaging pills, and positioning a tool with pinpoint accuracy. These same features are important in many other medical applications. A short list of some medical applications includes centrifuges, medical scanners, medical packaging, X-ray tables and cameras, and medical robots. But what makes the servomotor different than other motors? The answer is in the servomotor's design, its use of a feedback device, and how it is manufactured. These elements provide the servomotor with its base advantages. Servomotors are designed specifically to have smaller diameters while maintaining the same output HP or torque. For example, a typical one horsepower AC induction motor would be 19 cm (7.6 in.) in diameter, whereas a SCR rated motor would be 12 cm (4.7 in.), however, a brushless servomotor still comes in smaller at 9 cm (3.5 in.). Smaller motor diameters lead to smaller rotors, which reduce rotor mass, or inertia. This allows for faster acceleration positioning. Faster operation reflects directly to the bottom line of an application, for example, how fast white blood cells are counted, or how many pill containers can be packaged per hour. Another benefit of the servomotor is that it is coupled with a feedback device. Examples of feedback devices include tachometers, resolvers, and encoders. While a tachometer provides speed information only, resolvers and encoders provide speed as well as positioning information. These feedback devices, coupled with servomotors, provide a literal "closed loop" package. Figure 1 illustrates a comparison. In the open loop, the drive command goes out to the motor, but notice there is no information coming back to the control to indicate motor speed or position. In the closed loop, the drive command goes out, and a feedback signal comes back. Since this feedback signal provides an objective means to monitor or measure the procedure, it gains the ability to make corrections. Because of this, the servomotor with a feedback device in a closed loop system provides for greater accuracy in machining. This accuracy reveals itself in the quality of the An example of a Servomoter positioning a tool with the speed and precision required in the medical field. end result; how smoothly the x-ray table moves the patient, how accurately the scanner is positioned, or how precisely a medical robot positions instruments. The manufacturing of the servomotor incorporates special material design selection and unique winding of the motor. Materials are selected to allow servomotor operation at elevated winding temperatures of 155OC (other typical motors are designed to operate at 90-125OC). The higher temperature material ratings improve product life and reliability. As a result, this also improves the quality of the equipment into which it is designed. Additionally, in winding a servomotor more wire is fitted within the steel laminations. A servomotor typically will have a "slot fill" of 75-80% (most motors will only have a 65% fill). This allows the servomotor to provide extra torque, and improves efficiency, allowing for usage of a smaller, lighter motor, that can deliver higher performance for equipment such as medical beds and blood centrifuges. If equipment requires stainless steel parts servomotors are available with this feature, though many equipment designers aren't aware of it. Servomotors with all stainless steel housings are protected against various environments, are durable, and easy to clean. The housing and end-caps are designed with 304-grade stainless steel, the shaft 416; these motors employ FDA compliant shaft seal (complies with food industry standards), H1 bearing grease (classified incidental food contact), and the nameplate is laser etched. Some medical applications require gearing, and there are stainless steel gear heads available to compliment these operations. The gears have low backlash 10 arcmin maximum, which provides accuracy for the equipment and precision in a host of applications. Servomotors have numerous improvements/advantages over typical, traditional motors. They are designed to respond quickly for improving processes. Sorting or packaging pills or filling containers, servos provide accuracy coupled with speed in systems including positioning lasers, operating robots, and spinning blood centrifuges. Servos are designed to provide more torque and higher efficiencies for equipment, whether counting white blood cells, pumping blood, or operating centrifuges. Though these are just a few examples of tasks Servos complete with ease, their applications are broad and bound to expand as new services require higher precision, speed, and accuracy. Servomotors represent the best long-term equipment investment among choices available now. TMD Baldor Electric Company Forth Smith, AR baldor.com

Explore the September October 2006 Issue
Check out more from this issue and find your next story to read.
Latest from Today's Medical Developments
- HERMES AWARD 2025 – Jury nominates three tech innovations
- Vision Engineering’s EVO Cam HALO
- How to Reduce First Article Inspection Creation Time by 70% to 90% with DISCUS Software
- FANUC America launches new robot tutorial website for all
- Murata Machinery USA’s MT1065EX twin-spindle, CNC turning center
- #40 - Lunch & Learn with Fagor Automation
- Kistler offers service for piezoelectric force sensors and measuring chains
- Creaform’s Pro version of Scan-to-CAD Application Module